Beyond Dairy: Bega's Commitment to Safety
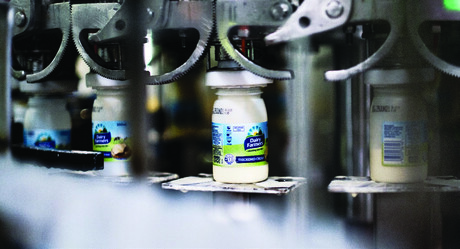
Bega Group is a well-known name in the Australian dairy and food industry, celebrated for its iconic products like Bega Cheese, Vegemite, and Peanut Butter. With a rich history dating back to 1899, Bega has become a breakfast staple across the nation. In 2020, Bega made a major acquisition expanding its production sites from 9 to 21 plants nationwide. This acquisition brought new challenges for Bega, particularly in standardising and ensuring the safety and efficiency of operations across all plants.
How a Bega product is made
Most Bega products are cow’s milk-based and so the process begins with the intake of raw milk. The production process involves several intricate steps with a high level of automation. Let’s take the famous Bega Cheese for example. The milk undergoes pasteurisation to ensure safety and quality before being mixed with rennet and cultures to start the curdling process. The curds are then cut, cooked, and moulded. Ageing takes place in controlled environments until it reaches maturity which typically lasts between 6 to 18 months before moving to the packaging stage and finally being dispatched.
The key concern lies in the packaging process involving fast-moving parts and complex machinery. This is also where personnel are in closest proximity to the machines and potentially more exposed to hazards, especially when operating filling machines, packaging machines, case packers and palletisation systems.
Partnering with Pilz for Safety
To support Bega’s Safety Principles, Pilz were commissioned to conduct plant assessments across their 21 sites. “There’s a belief in Bega that every safety incident is preventable.” In support of this belief, Bega saw opportunities to improve hazard awareness and further develop safety systems.
Pilz Australia conducted thorough plant assessments on 21 Bega sites, each with varying potential hazards and areas for improvement. The plant assessment encompasses an on-site evaluation of the machinery’s condition, followed by a formal presentation of findings.
Using a structured risk assessment approach, Pilz was able to gather sufficient data to assess key compliance and safety factors. All machines were assessed using a multi-parameter analysis, providing an estimate and priority list of the safety requirements needed for each machine.
On average, about 150 assets were assessed at each site, with each asset having 8–10 recommendations for improvement. The comprehensive assessment resulted in thousands of recommendations and actions to enhance safety across all sites.
Following these assessments, the Bega team underwent several training sessions on Machinery Safety conducted by Pilz, with more ongoing.
Key courses included the MachineSAFE Comprehensive course, which covers the fundamentals of international and local safety standards, risk assessment methodologies, and the application of safety components. Another notable course was the renowned CMSE (Certified Machinery Safety Expert) training, a globally recognised qualification programme that deepens expertise in complex safety systems and prepares participants to become certified machine safety experts.
Having certified experts in the field provides numerous benefits, including enhanced credibility, peace of mind, and assurance of compliance with safety regulations. It also ensures that the team is well-equipped to handle complex machinery safety challenges, thereby reducing the risk of accidents and improving overall operational efficiency.
This initiative aims to enhance the Bega team’s capabilities and foster a holistic approach to supporting a culture of safety within the organisation.
Customer Statement
The Pilz team’s knowledge and expertise live up to the brand promise. It’s what you expect. Their detailed assessments gave us valuable insights from both a business and practical standpoint. We discovered numerous hazards that we were previously unaware of. Having experts in the field conduct these assessments improved hazard awareness, especially for those in Operations. Plus, their support didn’t stop after the assessments — they were always available to help.
— Neil Roberts, Group Risk Engineer, Bega Group.
Through comprehensive plant assessments, Pilz has identified and supported mitigation of numerous hazards and Bega’s continuous improvement journey. By prioritising safety, Bega continues to uphold its reputation for quality and reliability, ensuring that its products remain a trusted choice for consumers.
Find out more about our Machine Safety and Security Services
How Bottoms Up Beer saves $12,000 a month with Fishbowl
Unique drafting beer system Bottoms Up Beer handles its ever-increasing order volume with ease...
Welcome to the Family — Neogen Petrifilm Bacillus cereus Count Plate
Last year marked the fortieth anniversary of Neogen® Petrifilm® Plates.
Seamless Power and Data Transmission: Optimising Bottling Plant Performance with Kubler Slip Rings
The Challenge of High-Speed Bottling Lines