Seamless Power and Data Transmission: Optimising Bottling Plant Performance with Kubler Slip Rings
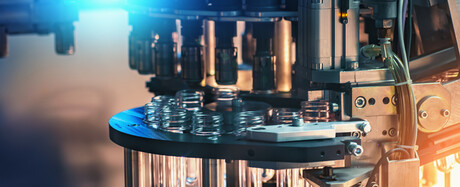
The Challenge of High-Speed Bottling Lines
In modern bottling plants, efficiency is everything. Every stage of production — from forming bottles to filling, sealing, and labelling — relies on high-speed automation. The faster and more precise these processes run, the greater the output, the lower the waste, and the higher the profitability.
However, the dynamic nature of bottling lines presents a major technical challenge: seamless power, data, and fluid transmission in rotating environments. Many of the critical components in bottling plants, such as rotary tables and carousel systems, operate on continuously moving platforms. If power or data transfer is disrupted, even momentarily, it can cause operational slowdowns, product inconsistencies, or complete system failures — leading to costly downtime.
This is where slip ring technology comes in. Slip rings are electromechanical devices that allow continuous transmission of electrical signals, power, and even media (such as compressed air or fluid) from a stationary source to a rotating component. They play an essential role in ensuring uninterrupted, high-speed operation in bottling plants.
The Role of Kubler Slip Rings in Bottling Operations
Kubler, a global leader in industrial automation components, has developed high-performance slip rings designed to meet the rigorous demands of the food and beverage sector. With a combination of precision engineering, robust durability, and hygienic design, Kubler Slip Rings help bottling plants achieve uninterrupted performance while maintaining stringent industry standards.
Key Processes Supported by Slip Rings
Kubler Slip Rings are integrated into multiple stages of the bottling process, ensuring efficiency and reliability:
- Stretch Blow Moulding — The foundation of PET bottle production. Slip rings enable the seamless transmission of power and control signals to high-speed rotary systems, ensuring consistent bottle formation.
- Rinsing & Inspection — Hygiene and quality control are critical in food and beverage processing. Slip rings support real-time data transfer for automated rinsing and inspection systems, ensuring each bottle meets safety and cleanliness standards.
- Filling — Precision filling is essential to prevent waste and ensure consistency. Slip rings enable accurate volume control by facilitating continuous signal transmission between sensors and filling mechanisms.
- Capping & Labelling — High-speed capping and labelling require synchronised motion control. Slip rings provide uninterrupted power and data flow to the capping heads and labelling stations, ensuring each bottle is sealed and branded correctly.
The Kubler Advantage: Precision, Performance, and Durability
Kubler’s modular technology system ensures maximum flexibility, offering customisable configurations to meet the specific needs of different bottling plants. Key features include:
1. Interference-Free Signal Transmission
Modern bottling plants rely on real-time data exchange for machine coordination. Kubler Slip Rings ensure error-free signal transmission, supporting Ethernet and other industrial communication protocols crucial for synchronised plant operations.
2. Integrated Media Lead-Through
Kubler's slip rings can transmit compressed air or liquids alongside electrical signals, eliminating the need for additional components and simplifying bottling plant operations.
3. Modular and Customisable Design
Kubler offers modular slip ring configurations, allowing for tailored solutions based on the number of transmission channels required. This adaptability ensures that slip rings can be precisely configured for different bottling plant setups.
4. High Degree of Protection
Kubler Slip Rings are designed for harsh industrial environments, featuring aluminium or stainless-steel housings for enhanced durability and longevity. Their robust design ensures extended operational life with minimal maintenance.
5. Specific Slip Ring Models for Different Process Steps
Kubler offers specialised slip rings optimised for key bottling processes:
- Blow Moulding: The SR160 and SR250H slip rings ensure uninterrupted power and data transmission during PET bottle formation.
- Filling: The SR120 and SR160 slip rings enable precise, interference-free signal transmission for high-speed filling operations.
- Sealing & Labelling: The SR120 slip ring provides seamless power and data transfer for control tasks in sealing and labelling stations.
The Impact: A More Efficient, Reliable Bottling Line
By integrating Kubler Slip Rings into their automation systems, bottling plants benefit from:
- Uninterrupted power and data transmission — reducing operational downtime and communication failures.
- Greater process efficiency — enabling high-speed, high-precision bottling operations.
- Lower maintenance and extended lifespan — minimising servicing needs and reducing long-term costs.
- Compliance with food-grade hygiene standards — meeting stringent industry regulations.
For plant managers and engineers seeking to optimise performance, enhance reliability, and reduce bottlenecks, slip ring technology is a critical investment.
Learn More
Discover how Kubler Slip Rings can enhance the performance of bottling plants. Read more about the solution here.
Smart AI solutions shaping Australia's food future
With Australia approaching a federal election in the coming months, the government is stepping up...
Detection and Quantification of Lactose in Dairy Products
The Neogen Megazyme K-LOLAC test kit is a widely used enzymatic assay for the quantitative...
Complete processing lines for savoury snacks: challenges and opportunities
The global savoury snack market faces several challenges and opportunities.