Enhancing warehouse automation with system architecture
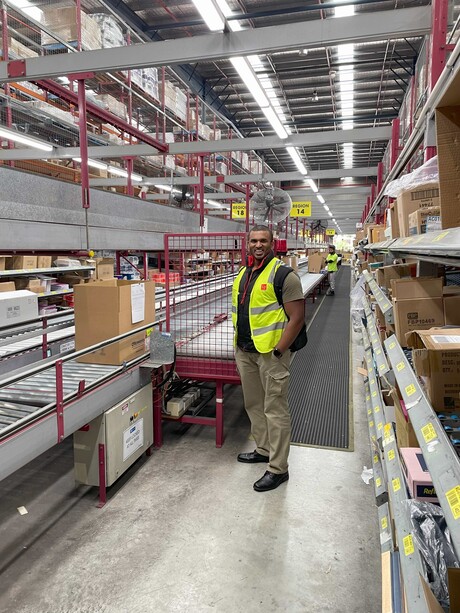
Addressing the demand for dedicated Industry 4.0 and IoT-focused podcasts, Open IIoT— a cohort of Australia’s most prominent automation brands — has launched the ‘Industry 4.0 and Beyond’ Podcast, featuring the group’s signature style of ‘cutting through the jargon’.
Having recently reached the milestone of 1000 downloads, the podcast releases episodes monthly and features Jozef Ceh of SMC Corporation Australia and New Zealand and Wade Leslie of KUKA Robot Automation as moderators, with representatives from other Open IIoT member companies (Beckhoff Automation, NORD DRIVESYSTEMS, Balluff and Argus) as guests.
To ensure a diverse range of perspectives and expert industry insights, the members are regularly joined by customers and partners from a multitude of industries and manufacturing sectors as they discuss new technologies and the unique challenges and benefits of Industry 4.0 implementation.
One such case study discussed on episode 11 of Industry 4.0 and Beyond is that of the collaboration between Open IIoT member Harry Mulder of Beckhoff Automation and Lucky Thommadura of Layer Seven Automation, a provider of cutting-edge warehouse and factory automation solutions.
It involves the successful transformation of a high-profile distribution centre in North Rocks, Sydney. The centre was grappling with an outdated system and Layer Seven Automation was tasked with finding a futureproof solution to improve efficiency, flexibility and connectivity while minimising costs. They found that solution in Beckhoff’s Industrial PC (IPC).
The challenge
The distribution centre was facing a challenge with its old Dexion system, consisting of 700 m of conveyor line and 28 diverter stations, which had worked well for many years. But the controller boards started to fail one by one and it became clear that it was reaching the end of its life. It was a propriety system and new parts were expensive, so management decided something had to be done.
Layer Seven Automation found the solution to this challenge in Beckhoff’s C6920 IPC, which linked to all the diverter stations via the company’s EtherCAT network and seamlessly merged Windows-based systems with a virtual programmable logic controller (PLC). This set-up offered numerous benefits, including faster operational processes, real-time program testing from multiple locations, cloud-based capabilities and third-party connectivity.
The project was executed in phases, starting with replacing the boards at each diverter station with Leuze scanners. The use of these advanced scanners with built-in I/O points streamlined wiring and simplified the design, while the EtherCAT network provided speed and reliability.
Key outcomes
The solution delivered outcomes, including:
- Fast program execution times: The IPC offered rapid deployment capabilities, including network updates, an essential feature for a logistics centre in a post-COVID environment.
- Easy programming: Even employees with minimal industrial programming experience were able to quickly get up to speed with the user-friendly interface of the Beckhoff IPC.
- Real-time data capture: The new system captured raw barcode data from scanners, decoded it in real time and executed logic for each zone, ensuring efficient box routing and diversion.
- The benefits of a Windows OS: The IPC’s Windows operating system allows users to create their own programs and messaging systems to run concurrently with the control program.
- Robust event logging: Every box detection was recorded as an event in Beckhoff’s TwinCAT event log and Layer Seven’s event log. This was facilitated by RabbitMQ, a message queuing program, chosen for its suitability over MQTT for this specific application.
- Enhanced visualisation: Data from the Beckhoff controller was extracted via ADS protocol, allowing real-time visualisation of operations. This data can be sorted into databases and message queues, facilitating dynamic reporting and analysis.
- Operational efficiency: The system enabled the distribution centre to manage peak occupancy zones effectively, thereby optimising resources and reducing operational bottlenecks. It also allowed for better reporting for management, although this capability is not yet finalised.
- Cost savings: The new architecture proved highly cost-effective, replacing the need for multiple replacement boards with a single, efficient controller solution.
- Data security: The Beckhoff-based solution provided enhanced security by isolating the EtherCAT network, limiting exposure to potential threats.
Future plans
Layer Seven Automation plans to implement redundancy in the form of a hot standby CPU for increased system availability. Additionally, they intend to optimise the system execution load to accommodate web services for visualisation purposes. The use of ADS to extract data for further processing and integration into ERP systems like SAP and MS-Dynamics is a key part of these plans.
This case study outlining the innovative architecture implementation at the distribution centre serves as a testament to the power of automation and efficient system design. By leveraging Beckhoff’s IPC technologies and strategic planning, they achieved enhanced operational efficiency, real-time data insights and a cost-effective solution for future scalability.
Hear more about this innovative project, directly from the real-life implementers on the Industry 4.0 and Beyond podcast, available at https://openiiot.com.au/open-iiot-podcast/.
Phone:
Timmer quickLIFT and heavyLIFT vacuum hose lifters
Timmer has a range of vacuum hose lifters for safely lifting and lowering heavy goods.
Key Technology Iso-Flo, Impulse, Zephyr and Marathon vibratory conveyors
Key Technology introduces high-capacity vibratory conveyors for advanced food-handling applications.
Sidel RoboAccess_Pal S robotic and cobotic palletising solution
RoboAccess_Pal S, Sidel's latest robotic and cobotic palletising solution, will be in action...