Pressure & temperature measurement instrumentation selection factors
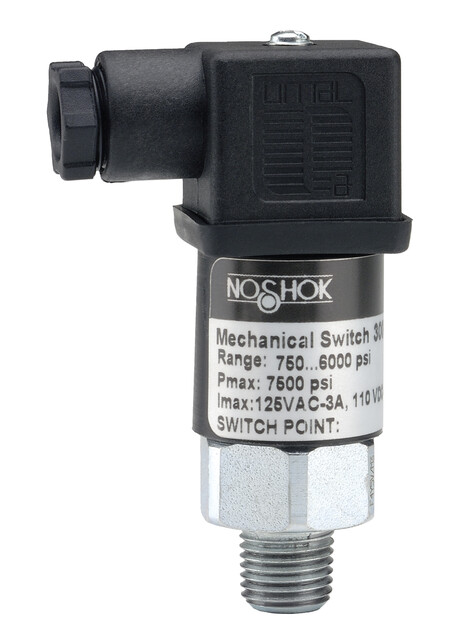
There is a vast variety of pressure and temperature measurement instrumentation, with countless options and specifications. When deciding on the best instrument for your application, there are several key factors to consider which can help prevent costly errors, inefficiencies and lost resources in the future.
Review this checklist of the main points to consider when selecting the pressure or temperature measurement instrument which will provide the proper performance and longevity in your specific application.
1. Accuracy
How important is accuracy in your application? In some industrial applications, repeatability may be more important than accuracy. Linearity and hysteresis may take precedence over accuracy in applications where process pressures vary widely. If accuracy is a very important factor, such as in low-differential, critical pressure applications, you’ll need to select an instrument that meets these requirements. As an example, a thermocouple may be chosen over a Resistive Temperature Measuring Device (RTD) in a temperature measurement application because it is more cost-effective, rugged and provides a wider range of measurement, while an RTD might be chosen if accuracy, repeatability and long term stability are the most important factors.
2. Measurement Range
An instrument’s range must be matched to the requirements of the application. For example, to ensure optimal control and monitoring of vapours, a Vapour Recovery Unit must have reliable instrumentation in place that is capable of accurately measuring low pressure. On the other end of the spectrum, if you have a high pressure application such as a water jet, you’ll need an instrument that can measure pressures of 60,000 to 80,000 psi.
3. Environment: Vibration, Pulsation, Hazardous Locations
The environment of the application is a critical consideration when selecting pressure or temperature measurement instrumentation. Construction materials can be specified for harsh environments where the instrument may be subject to weather or temperature extremes, or corrosive media. To address applications where pulsation or vibration are a factor, fill fluids, Maximum Indicating Pointers, orifices or snubbers can be selected.
Vibration due to pumps, motors and other rotating equipment can cause excess wear and possible premature failure of internal working parts of a pressure or temperature measurement instrument. Vibration also causes difficulty in accurate reading of the instrument, due to pointer oscillation. One of the most common causes of failure is exposure to continuous vibration. It would be good for the user to be aware of these conditions and work with your supplier for a solution.
Process pulsation can occur around the discharge of pumps as well as quick operating valves. Many users assume that liquid filling the case of the instrument will fully address pulsation. Although liquid filling the case helps to dampen the effects of pulsation, it often does not fully address this process condition. Pulsation dampeners are installed upstream of the inlet to the instrument. Some common approaches are a piston-type snubber, a sintered metal snubber, or a threaded in-flow restrictor in the inlet of the instrument.
A needle valve installed upstream of the instrument that is “pinched down” or slightly opened, is another common practice to address pulsation. It is not recommended to rely solely on a needle valve to address pulsation, due to the fact that the user could inadvertently open the valve and thereby negate flow restriction. In clean fluids (gases or clean low viscosity liquids) a threaded orifice/flow restrictor or a sintered metal snubber is the most cost efficient way to address pulsation. In dirtier and higher viscosity fluids a piston snubber is usually recommended.
In hazardous environments, the user should be aware of ATEX, IECeX approval requirements for electronic measurement devices. The user may also need to be aware of the various approaches to the application, which could include Intrinsically Safe installations, or Non-Incendive and Explosion-Proof installations.
4. Temperature Factors
It is important to consider both the process and the ambient temperature when selecting measurement instrumentation.
As an example with pressure gauges, for every 100 °F shift in temperature from which the gauge is calibrated, the user can experience up to a 2% additional error in reading. The cause is the change in the elasticity or spring rate of the Bourdon tube element with temperature. While it is difficult to circumvent the influence of ambient temperature, we can address the influence of process temperature. In the case of elevated process temperatures, the user will need to dissipate heat before it comes in contact with the measuring element of the instrument. In applications where the user is measuring steam, the common practice is to install coil or pigtail syphons to dissipate process heat.
Another common practice is to install a diaphragm seal with capillary to separate the instrument from the high heat source. There are many options available with fill fluids in the seal and capillary system to withstand elevated process temperatures. In severe cold ambient conditions, the user may elect to heat trace their instrumentation. Some common methods for heat tracing can be electric or steam.
For temperature measurement applications, the materials used in RTDs and thermocouples have temperature limitations which can be an important consideration. The sensing element used in RTDs generally contains a platinum wire or film, a ceramic housing and ceramic cement or glass to seal the sensing element and support the element wire. In general, platinum sensing elements can be exposed to temperatures up to approximately 1200 °F. Other materials such as Nickel, Copper and a Nickel/Iron alloy can also be used, however, their temperature limits are quite a bit lower than Platinum.
Thermocouples are another common way to measure a process temperature, but the user needs to be aware of their temperature limitations as well.
5. Location & Mounting Requirements
The location of the instrument in the process can be a significant consideration. Oftentimes the instrument must be mounted in a location that is not convenient for user interface. Possible solutions can include utilizing a swivel adaptor mounted to the inlet of the instrument to orient the instrument more toward the user, diaphragm seals and capillary to bring the indication closer to the user, or transmitters can be installed to allow a commonly used signal to be transmitted to a receiving device such as a digital indicator or PLC.
6. Type of Process Medium
The process mediums that are commonly measured include gas, liquids and vapours which can be corrosive or benign. Careful consideration must be used with regard to chemical compatibility with the instrument’s materials of construction.
7. Type of Indication or Feedback Desired
In virtually all process variables that are measured, the user can elect a mechanical or electronic approach.
With a mechanical approach, the user often requires a local indication. Examples include a pressure gauge or bimetallic thermometer which provide a dial or a pointer reading. Other examples might be a level gauge or flow meter that provide local indication.
With an electronic approach, a transmitter or a switch can be utilized to provide a commonly used signal to a receiving device for remote monitoring and control.
8. Type of Engineering Units Required
The user will need to determine what units of measurement are required for the application. There is a wide array of engineering units that can be used for all process variables, to include temperature, pressure, level and flow.
In summary, it is essential to prioritise the requirements of the application before you make the investment in a measurement device. Addressing these 8 factors can help in achieving a successful measurement outcome.
For further information contact AMS Instrumentation & Calibration Pty Ltd on 03-9017 8225, or Freecall (NZ) 0800 442 743, alternatively on e-mail: sales@ams-ic.com.au or visit our web site at www.ams-ic.com.au.
Smart AI solutions shaping Australia's food future
With Australia approaching a federal election in the coming months, the government is stepping up...
Detection and Quantification of Lactose in Dairy Products
The Neogen Megazyme K-LOLAC test kit is a widely used enzymatic assay for the quantitative...
Complete processing lines for savoury snacks: challenges and opportunities
The global savoury snack market faces several challenges and opportunities.