Decarbonisation in food processing
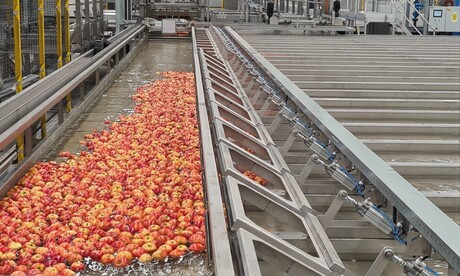
Heat pumps and thermal energy storage lead the charge to net zero.
When one of Australia’s largest fruit growers, WF Montague, was designing its greenfield apple and stone fruit packing facility in Narre Warren, Victoria, energy efficiency was central to ensuring a state-of-the-art facility that delivered efficiency, sustainability and competitiveness.
As is often the case in food and beverage production, however, the company faced a challenge. The heat demands for cleaning and waxing fruit prior to cold-storage far exceeded the small amount of waste heat available from the Ammonia refrigeration system used for its controlled-atmosphere cold rooms. Burning gas in boilers was the typical solution used by Compac — the processing equipment supplier, but the cost of a gas connection and the negative impact on Montague’s decarbonisation plans meant this solution was not feasible. The decarbonisation of heat requiring a transition from gas to electricity is a significant challenge when high-temperature hot water is required and there are few solutions.
The perfect match: heat pumps and thermal energy storage
The design engineers for the project’s refrigeration systems, Liquid Ice Refrigeration, worked with Compac and Australian heat pump manufacturer Glaciem Cooling Technologies to design and deliver a high-temperature heat pump system that provides the large amount of hot water required. The system provides the hot water with a very high efficiency, the by-product of heating the water is free cooling for the main ammonia/glycol cooling system. As a result, when the heat pump is heating water the ammonia refrigeration plant is not required. This reduces the power required for refrigeration and reduces the operating cost and extends the life of the ammonia compressor.
Often process needs result in a mismatch between heating and the cooling demands. Typically this happens in winter when the cooling loads are low. Most heat pump systems would cool the ambient air during this time which is non useful cooling. Glaciem’s unique design incorporates Thermal Energy Storage (TES) as a cooling source instead of air. TES is a system that uses a phase change material to store energy. When the heat is extracted from the liquid in a TES System, the contents of the system change from liquid to solid. Essentially this is storing “cold”. It is like a ‘thermal battery’ charged with cold thermal energy — rather than electricity — when the heat pump extracts the heat from it. The cold stored in this process is very dense and can be discharged at another time as you would use the power in an electrical battery, but with better efficiency. A TES system also has a life of about 30 years and can be charged and discharged without the degradation effect common with electrical batteries. This provides a way for the cooling to be used at a different time to offset the refrigeration demands of Montague’s refrigeration systems.
Glaciem heat pumps use CO2 in a “refrigeration cycle” to move heat out of a heat source and deliver it in a form that is useful for applications at higher temperatures. Heat pumps improve the quality of the heat using mechanical energy — a set of compressors which produce about three times the thermal energy for each unit of electrical energy utilized. The result is the production of significant volumes of hot water at 83°C. This replaces the need to burn gas, drastically reducing CO2 emissions. The Glaciem CO2 heat pump operates with high efficiency even in the coldest of Narre Warren days, unlike many heat pump designs which would not work efficiently in cold ambient conditions including Ammonia heat pumps.
The operation of the system is controlled by Glaciem’s forecasting, optimization and control system which ensures the TES is charged and discharged for optimal energy use. For other Glaciem TES users the system allows them to optimize behind-the-meter solar PV generation or Power Purchase Agreements (PPAs) to maximise the use of renewables and to shift load to take advantage of variable energy costs (price arbitrage). It enables heat pumps to concurrently cool and heat when their demand for cooling happens at a different time to their demand for heating.
Overall, the result of this approach is a reduced energy cost and a reduced carbon footprint. As the sector looks to meet ever increasing carbon reduction targets, CO2 heat pumps integrated with thermal energy storage are a critical part of the hybrid energy systems designed for the heating and cooling needs of most food and beverage production processes.
Bespoke system design for optimal efficiency
As with Montague’s and all of Glaciem’s projects, the CO2 heat pumps are customized to suit the exact mix of heating and cooling demands of the application for the best efficiency. These designs not only ensure optimal efficiency at “design load” (the peak energy required), but also “part loads”. Part loads are common in most applications for most of the year. Part loads occur when the ambient conditions are not as extreme as the peak conditions designed for or when production loads are lower. This means a large amount of thermal energy produced by a small amount of electricity — providing much better performance than electrical boilers and traditional HFC chillers.
The system is built with premium components and is delivered as a complete, tailored package to the same refrigeration and mechanical services contractors who provide other systems on site. In the case of Montague, refrigeration contractor Oomiak installed, commissioned, and integrated the system with the Ammonia refrigeration plant on-site, specific to Glaciem’s designs.
Size and scale are also challenges for off-the-shelf heat pumps which tend to provide a lower temperature water, adding complexity and cost to many industrial and commercial applications. The heating demands at Montague’s Narre Warren site are met with a heat pump capable of producing high-temperature water and 1100 kW of heating, from a single CO2 heat pump, believed to be the largest CO2 heat pump in the Southern Hemisphere. The system is controlled by a Schneider PLC with a state-of-the-art human-machine interface (HMI). The HMI allows site operators and contractors to view the current operations of the system, the state of charge of the TES system, the internal operations of the heat pump including compressor status, energy use, energy flows, temperatures and pressures. People unfamiliar with the physical layout of the system can see a visualization of the actual system layout with the major components and their status described with overlays. Conditions needing attention are highlighted in red. Further, the heat pump’s Internet of Things (IoT) design means all of this can be viewed remotely, allowing Glaciem engineers in Adelaide to monitor and manage the system and support the onsite activities of service and maintenance engineers.
A path to decarbonisation
The project has resulted in Glaciem providing Montague with a way to deliver its hot water demands with optimal energy efficiency, and to eliminate the need to burn gas (or other fossil fuels). Montague is set up to meet its decarbonisation objectives without the need to tackle the complex transition from gas to electricity in the future.
System specifications:
Heat Pump Specification | Glaciem GHP-6626 CO2 high temperature heat pump |
Design Demand Load Heating | 716kW @50°C - 83°C | 1100kW @35°C - 83°C |
Design Demand Load Cooling | 726kW @ -4°C |
Refrigerant: | R744 (CO2) |
COP (Heating and Cooling) | 3.8 |
Dimensions | 6500Lx2400Wx2387H mm |
Thermal Energy Storage System | 2 x Glaciem DYN900 TES Systems |
Storage Capacity | 4000kWh |
Phase Change Material | -6°C PCM |
Charge Rate | 200kW@10 hr |
Discharge Rate | 200kW@10 hr |
COP (Discharge) | 40-70 depending on the discharge profile |
Dimensions | 6418Lx2772Wx3330H mm |
Flexible Biogas Solutions For The Food Sector
Anaerobic Digestion can be used to treat organic waste and produce renewable energy that can be...
Flexible Biogas Solutions For The Food Sector
Anaerobic Digestion technology can treat organic waste on-site to produce renewable energy that...
Plug and Play Solutions for a Greener Future
Are you encountering large trade waste and energy costs? Are you watching dollars literally go...