Circular Solutions for Packaged Waste
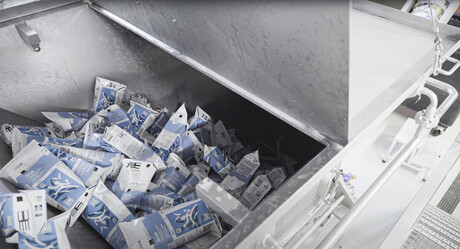
Australia’s food and beverage industry is increasingly focused on improving sustainability by reducing waste and moving to make processes more circular. Efficiently managing production waste, especially packaging and filled containers that cannot be sold due to quality control standards, is a key challenge. Whether in brewing, dairy processing, or other beverage production, ensuring rejected materials are properly separated and recovered is critical to reducing environmental impact and lowering disposal costs.
WEIMA PUEHLER technology enables Australian manufacturers to process waste more effectively in-house. The hydraulic dewatering and compaction presses provide a comprehensive solution for separating liquids from solids and significantly reducing the volume of packaging waste. These machines are especially relevant for handling aluminium cans, PET bottles, milk cartons and liquid paperboard.
Emmi has relied on depackaging technology for two decades
At the largest Emmi location in Switzerland, in Ostermundigen, they have been familiar with PUEHLER draining and compressing technology for over 20 years. Thanks to the successful collaboration, Emmi is relying on WEIMA as a partner for its new system with a PUEHLER press as a key component at another large location, where milk, cream and butter are primarily produced.
Deputy Site Manager Hans-Peter Steuri explains: “We process around 190 million litres of milk and about 60 million litres of cream. Before using the PUEHLER press, we had to manually open every full piece of waste packaging. That was hardly productive. With WEIMA, we have finally found the right partner for our task.”
Steuri aptly described the stringent demands that the new PUEHLER ReWork press meets: “As a food manufacturer, hygiene is the be-all and end-all. WEIMA machines are user-friendly to maintain, have CIP cleaning and comply with strict hygienic design specifications. In addition to the high throughput, the WEIMA system requires significantly less space than those of other providers — a clear advantage for us.”
Emmi’s ReWork facility pays off in many ways. It is not only particularly economical and efficient but above all sustainable in dealing with resources. WEIMA PUEHLER G.300 thus actively supports the Swiss dairy processor in its ambitious environmental goals — away from a linear economy and towards a recycling-based circular economy.
New Belgium Brewery finds WEIMA solution faster, safer and cleaner
New Belgium brewery, Colorado, experienced a significant surge in productivity after adding a second canning line to its packaging facility. This necessitated a more effective waste management solution to keep up with their increased production. Capable of processing an impressive 12,000 to 20,000 cans in a 12-hour shift, the WEIMA PUEHLER G.200 has seamlessly integrated into their operations, offering enhanced efficiency and waste diversion.
“Our previous press was not made for liquid and beer spills. With the G.200, we have a stainless-steel system that we can hit with caustic foam and water, without worrying about rust or paint issues,” says Soren Daugaard, Manufacturing Excellence Site Lead. Danny Banister, Packaging Manager, highlighted the ergonomic and efficiency gains facilitated by the WEIMA machine. “Operators can now use equipment instead of hand-loading into our crusher, resulting in significant time savings and improved efficiency.”
Smaller machine makes the most of valuable floorspace
The WEIMA PUEHLER E.200 offers a more compact, economical option for dewatering and compaction. Designed for smaller-scale operations or businesses with limited space, it’s enhanced by lockable rollers, allowing the machine to be easily positioned wherever it’s needed.
This was the case for Fiddlehead Brewery in Vermont, where quality control during canning occasionally results in underfilled or otherwise “out of spec” cans, which must be removed from the production line. Historically the company had employees manually opening and pouring out beer cans for a couple of hours each shift. This work, while necessary, was both monotonous and impractical. “Efficiency is particularly important to us, but we also want our employees to enjoy their work. Emptying the cans was very time-consuming and we knew there had to be a better solution,” said Jon Moorer, Fiddlehead’s production manager.
The E.200 drainage press now gives the brewery more flexibility while freeing up its employees to do more meaningful and essential tasks. Out-of-spec rejects are now automatically ejected from the conveyor, allowing the rejected cans to fall directly into the hopper of the E.200. The completed discs of compressed aluminium save space on the production floor and make recycling the valuable metal more manageable and profitable.
Effective Waste Management for Circular Manufacturing
Both the WEIMA G.200 and WEIMA E.200 offer innovative solutions for waste management in the Australian food and beverage industry. The G.200 excels in high-volume applications, processing large quantities of material with high efficiency. On the other hand, the E.200 is a compact and cost-effective solution for smaller-scale operations or those with limited space. These machines have proven effective in reducing waste, improving recycling efforts, and providing a sustainable alternative for waste management in the food and beverage industry. Both machines offer robust designs, user-friendly controls, and low-maintenance operation, critical for multi-person operation and shift work often found in food and beverage production.
With success across Europe and in Northern America, it’s time these high-performance machines streamline waste management and contribute to a circular economy in Australia. Contact CEMAC technologies for more information: (03) 8400 6066 or info@cemactech.com.
Safer, Smarter Labelling from PPC
As awareness of food allergies grows and regulations around food safety become more stringent,...
Stay Ahead of Food Safety Regulations with PPC's Allergen Management Labels
PPC's card printer-based price tag solution allows users to produce hygienic, food-safe...
Boxes on demand: machine revolutionises packaging practices
No more time wasted making boxes and no more issues with box warehouse logistics, the Boxway...