We've expanded what we can do, so you can too!
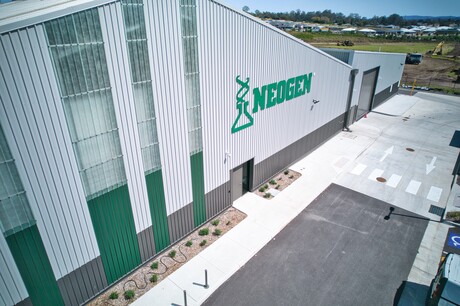
A little over a year ago, two global leaders of the food safety industry became one when 3M’s Food Safety Division joined Neogen. As the transition nears completion, the full benefits to local food and beverage manufacturers are being realised.
Neogen’s Division Sales Manager ANZ, Hashitha Perera said the acquisition of 3M Food Safety built upon the company’s already significant leadership position by bringing the total number of employees to over 2,500 worldwide, with a presence in more than 140 countries.
“Neogen is all about harnessing the power of science and technology to help provide a safe and reliable food supply for everyone,” he said.
“We sometimes use phrases like ‘from paddock to plate’ or ‘farm to fork’ because we offer products and services for primary producers through to food and beverage manufacturers.
“From a food safety perspective, we have increased our footprint in food diagnostics as part of this integration.”
Perera said the merger had also expanded Neogen’s local presence in Australia and New Zealand.
“The entire ANZ 3M Food Safety sales and technical team came over to Neogen in September 2022,” he said.
“So, we have a broader portfolio, a larger team, more capabilities, experience, knowledge and expertise.
“It has been a successful year since that transition. We have since expanded the combined team throughout Australia and New Zealand to better support the market.”
Neogen’s Marketing Manager, Anthony Watkins said both companies were already industry leaders in food safety, but the merger had resulted in greater opportunities for customers.
“Today, Neogen can offer a far wider range of high-quality solutions to address specific needs, we have access to some of the absolute best scientific and technical minds and facilities in the world, and we can offer even better locally based distribution and service from an experienced team who understand the industries they support.
“Our network of technical experts has doubled since the acquisition. We now have more than 300 scientists and engineers around the world, who are working to make food safety simpler and more effective,” he said.
Perera reiterated the benefits that have been created by bringing two expert food safety teams together to work on a global and local scale.
“We have global presence with local support,” he said.
“We explain that all the time to our customers. We highlight the global knowledge, especially for our global customers. We have some customers who operate in significant parts of Europe, North and South America, Asia, Australia and New Zealand.
“Maintaining those relationships at a global level is a benefit for our customers.
“But equally beneficial is having people here on the ground, in Australia and New Zealand, who can provide technical advice and support where it’s needed, when it’s needed. And who can draw on those global resources more efficiently because they understand how to apply them to local requirements.”
“As with everything, the knowledge base of two organisations put together creates more advantage for our customers who we can service even better than we did before.”
Perera said that after the merger they took the best aspects of each business and combined them in the new organisation. Effectively bringing the best of both worlds together and extending their capabilities to benefit customers.
One such advantage was being able to offer a wide range of solutions that not only satisfy specific testing requirements but also help improve efficiency by providing faster results.
“From manufacturing facilities to commercial labs, one of the key focus areas for them is to obtain a micro, allergen, chemical result in the shortest period of time,” he said.
“For example, a product may have a 10-day shelf life and you need to test the product before it can leave the manufacturing facility for the supermarkets.
“That turnaround time for the testing has traditionally taken three to five days.
“If you give that rapid result in as little as 14 hours, then you effectively extend the shelf life for retailers, which is a more viable option from a commercial standpoint.
“Similarly, we have solutions for hygiene monitoring that can give you reliable and actionable information in seconds, which means less downtime in factories and greater productivity.”
With Neogen’s acquisition of 3M Food Safety, the local food and beverage industry now has greater resources to draw upon and access to an unparalleled level of locally based service and support.
To find out how your business can benefit — visit Neogen Australasia.
Smart AI solutions shaping Australia's food future
With Australia approaching a federal election in the coming months, the government is stepping up...
Detection and Quantification of Lactose in Dairy Products
The Neogen Megazyme K-LOLAC test kit is a widely used enzymatic assay for the quantitative...
Complete processing lines for savoury snacks: challenges and opportunities
The global savoury snack market faces several challenges and opportunities.