The taste of sweet success
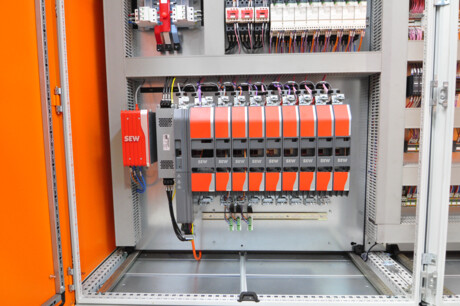
The need for an all-in-one solution for automation tasks comes from a single source, SEW Eurodrive’s MOVI-C covers complex motion control applications helping a confectionary machine achieve optimum results.
When a candy manufacturer in the United States needed a specific machine to manufacture soft-gummy candies they turned to JH Tester, who have been providing machine control solutions for over 10 years to the candy manufacturer.
Located in the western suburbs of Sydney, JH Tester Industrial Automation has been in operation for over 35 years. Family-owned and operated, the company was started in 1980 by John Tester providing technical service and support to the textile industry. Over 20 years ago, JH Tester transitioned its focus to the design and manufacture of automated systems for a variety of sectors, including manufacturing, food and beverage, building, mining, infrastructure, and water processing.
“Our specific strength is motion and motion control — anything that has servo controls is our sweet spot,” Tester said. “And we also have strengths in PLCs and HMIs. We pride ourselves on providing innovative simple automation solutions to often complex challenges in the manufacturing sector.”
Four modules — one solution
Designed and built in Australia, the confectionary machine features 18 MOVI-C Movidrive Modular axis controlled by the SEW Eurodrive MOVI-C Controller motion platform. “We’ve had a very close relationship with SEW ever since they entered the variable speed drive (VSD) market in Australia — around 30 years ago. The quality and reliability of their products and services make them an obvious choice for us,” said Tester.
The MOVISUITE software package offers a powerful but flexible programming package that provides planning, commissioning, operation and diagnostics software, electronic control and monitoring devices, mechanical drives and gearmotors in an all-in-one solution. All components can be fully integrated into most automation concepts, fieldbus topologies and network standards.
The MOVI-C CONTROLLER motion platform receives setpoints for single-axis or coordinated motions, and determines the motion path for the connected application axis, thereby taking care of tasks such as phase-synchronous operation, electronic cam function or kinematics. Predefined software modules are used to implement the motion control drive function quickly and reliably with the aid of graphical editors. Over 50 kinematic models provide for a broad range of mechanical configurations already being covered. Data is stored via a data exchange function on a memory card in the MOVI-C controller.
All drive functions of the motion control topology are available in the module automation topology. In addition to the graphical editors for the drive functions, automation tasks associated with the higher-level master controller can also be implemented in part or in full in a straightforward and flexible approach using the programming system in the MOVI-C controller.
Tester said, “The all-in-one integrated features of the MOVI-C motion package made it an obvious choice for the project.”
“Because it is a highly integrated solution, the MOVI-C was perfectly suited for this specific confection machine application, the heart of which was the motion platform that our internal software design engineer developed,” said Tester.
“The MOVI-C is a neat package — it is a compact practical solution,” said Tester. “Because of the MOVIDRIVE Modular dual axis control mounted in one hardware platform, you don’t need to occupy vast cabinet space to house it. Moreover, it reduces the switch gear and auxiliary components required.”
And, he said, it is also highly energy efficient. “It shares a common powerbase, which means that if any axis is in re-generation, or generating power, I can actually use that power by another axis.” This means that if one axis is slowing down or putting power back into the DC bus, other axis can utilise that power. With effective project planning, this it is possible to have a smaller power section than the collective sum of the control axis, if all axis are not motoring simultaneously, offering a significant savings from an OEM perspective.
Aside from the smarter power solutions, and compact design platform, the MOVI- Movidrive Modular also presented performance enhancements with motor resolution of 65,536ppr which has proven to offer exceptional motor performance. Another important aspect for implementing this hardware was the integrated safe circuit with level PLe performance.
The simplicity of the MOVI-C MOVISUITE software package allowed easy integration for the entire hardware package. “It also has only one platform to program for the 18 axis — it uses a common master virtual encoder to coordinate many axis, making it highly-coordinated,” said Tester. “The end product, in this example the confection machine, is therefore highly user-friendly and meets our standard for creating simple solutions to complex challenges.”
“High rates of productivity can be achieved with the application of the MOVI-C,” Tester said, with up to 2.5 tonnes of candy per hour able to be produced by the confection machine. The centrally-coordinating, multiple electronics cam curves enables multiple axis synchronisation for a virtual axis. “Because it is a highly integrated automated solution, we have very precise cam arrangements. While, normally, you’ll see clients using mechanical cams, we are using electronic cams to more effectively tie axis together,” Tester said.
“And the cams can be changed on-the-fly, which allows configuration of the machine while it is actually working. It means that we can change and modify the cam while the motor is running, modify the time unit of the machine and modify the lathe profile of the pumps during operation. These things are ordinarily very difficult to do while a machine is in motion. So on-the-fly updating of cams is a big advantage in this package.”
If there are issues with the drive, they can be swapped for others, while the SEW MOVI-C controller can download the parameters in the drive and reconfigure a drive with a minimum of disturbance. “This kind of flexibility eliminates downtime. You don’t have to stop the machine to load up a cam profile,” Tester said. “And this, once again, creates higher productivity and higher efficiency in all sorts of ways.”
Using the latest technology integrated into the MOVI-C product range has provided many advantages for JH Tester. “We were ahead of the market using such innovative new technologies. We have had a close relationship with SEW for a long time now, and they’re a great company to work with,” Tester said.
“As we develop new solutions with their products, we are now piloting many advanced and cutting-edge industrial automation solutions with SEW. So, it is a very fruitful relationship that works very well for both of us.”
The MOVI-C’s Ethernet connectivity also means that JH Tester can also deliver high-level after sales support with remote access. “We remotely monitor the machine and make sure it is functioning efficiently and as designed for purpose.”
Indeed, customer service and support on both a local and international level is something that JH Tester prides itself in providing to the manufacturing sector. “We reduce complexity in what can be very complex systems; we’ve simplified the cabinets; we provide high speed communications on the motion platform. The resultant benefits are simplicity and power,” said Tester.
“And, using the MOVI-C, it is very configurable for the end client: it is a stable, reliable, powerful platform that is energy efficient, that doesn’t stop when we change cams, that gives you real-time statistics on what it is doing, as well as real-time power consumption and real-position monitoring of every axis. SEW use ‘smart’ IoT enabled-encoders, so positional data is retained during a power cycle,” Tester said.
According to Darren Klonowski, National Product Manager at SEW Eurodrive the new innovative MOVI-C Automation System is a game changer: “MOVI-C® is the complete solution for your automation tasks. With the four modules; MOVISUITE® engineering software, MOVI-C controller technology, compact or modular inverter technology and centralised or decentralised drive technology, SEW Eurodrive provides a comprehensive modular automation solution from a single source,” said Klonowski.
Smart AI solutions shaping Australia's food future
With Australia approaching a federal election in the coming months, the government is stepping up...
Detection and Quantification of Lactose in Dairy Products
The Neogen Megazyme K-LOLAC test kit is a widely used enzymatic assay for the quantitative...
Complete processing lines for savoury snacks: challenges and opportunities
The global savoury snack market faces several challenges and opportunities.