Tasting the Success of Operational Excellence: Poppy's Chocolate
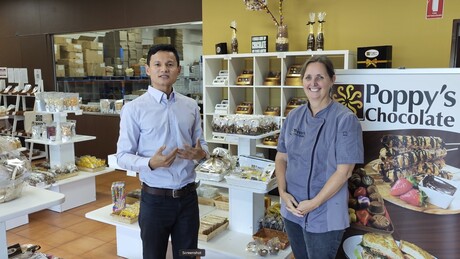
Background
Poppy’s Chocolate is a Queensland chocolatier, specialising in crafting exquisite chocolates and confections. Poppy’s Chocolate has become synonymous with high-quality ingredients, artisanal craftsmanship, and a dedication to creating delectable flavour experiences.
The Challenge
Poppy’s has been growing steadily and implemented a number of changes to support the growing business. Migrating to more robust and reliable digital systems and introduction of customer service agents to increase customer service, Poppy’s has over 300 active SKUs with around 70 high-volume lines.
The scheduling system used a manual trigger which feeds into a digital system for the weekly schedule. The schedule then drove the planning decisions for the following week. The scheduling system was struggling to keep up with demand and needed to be redesigned.
With 150 SKUs of raw materials, the control of raw materials was also unstructured with a weekly stocktake triggering the replenishment process, which was very manual and time consuming.
The Solution
A Kanban system was developed to effectively manage inventory, both incoming and outgoing, enabling tracking of finished goods production and the procurement of new raw materials. To familiarise the staff with the new visual management system, each team member received concise shopfloor coaching sessions.
To achieve a balanced production flow, a visual scheduling system for chocolate manufacturing was introduced. Additionally, TXM Senior Consultant, Justin Tao, implemented the TXM Lean Daily Leadership Process (LDLP) by utilising visual management boards displaying key metrics from previous days and weeks. Daily stand-up meetings were also introduced to foster a culture of continuous improvement.
The Results
Lynda and her team are now able to reliably fill orders quicker, more accurately and with less resources. Some of the tangible impact included:
- Achieved increased operational efficiency enabling a reduction in the number of operators from 11 to 5.
- Improved capacity to meet client orders during peak periods such as Christmas and Easter holidays.
- Implemented visual management schedules and standardised work processes, resulting in enhanced system comprehension and usability.
- Implemented production levelling and supermarket practices to effectively manage inventory, mitigating issues related to stockouts and overstocking.
- Leveraged the visual management system and implemented Lean daily meetings to significantly enhance team performance.
Meet us at APPEX 2024 at stand D210 or Contact TXM Lean Solutions via txm.com or call us directly 1800319552.
Smart AI solutions shaping Australia's food future
With Australia approaching a federal election in the coming months, the government is stepping up...
Detection and Quantification of Lactose in Dairy Products
The Neogen Megazyme K-LOLAC test kit is a widely used enzymatic assay for the quantitative...
Complete processing lines for savoury snacks: challenges and opportunities
The global savoury snack market faces several challenges and opportunities.