Smart intralogistics without muting sensors
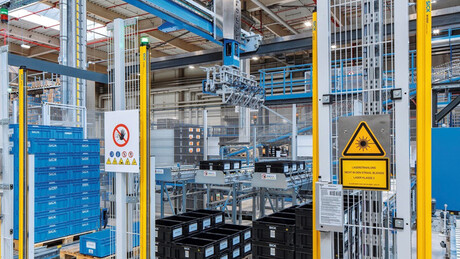
TGW Logistics has gained more flexibility in every respect by using the Safe Entry Exit safety system from SICK. In addition to reliably distinguishing between people and material, this also helps to alleviate space problems in tight plant layouts without additional muting sensors.
If you ask Tobias Czempinski, Director of R&D Smart Robotics & Technical Lead at TGW Robotics, why he wants to mostly do away with muting sensors in the future, you get a clear plea for the use of smart intralogistics solutions: “We were constantly on the lookout for a system that could handle the safety requirements using software. Although we have been working in the Siemens safety world for a long time, the mounting, alignment and reading in of the muting sensors was still a big task. We wanted to move the functionality to where we have to deal with it anyway, which is in the software.”
TGW-Robotics, based in Stephanskirchen in Upper Bavaria, is a wholly owned subsidiary of the Austrian TGW Logistics Group. As specialists for robotics applications connected to logistics processes, the automation engineers relied on AI, algorithms, self-teach systems and automated error handling.
Saving hardware — gaining security, transparency and time
With this in mind, TGW customer Heinrichsthaler Milchwerke in Radeberg also installed an automated central palletising system for cheese products. This is directly connected to the production processes and has doubled output to 100 pallets per hour. At the repalletising station, the TGW gantry robots are equipped with the Safe Entry Exit solution from SICK for safe human–machine collaboration behind grids.
In this case, an existing process signal that cannot be easily manipulated is used to initiate the muting function.
As soon as the transport goods have passed the protective device, it is immediately ready again to protect humans from hazards. The control simultaneously evaluates multiple material gates and provides the relevant diagnostic data for Industry 4.0 applications.
Tobias Czempinski greatly appreciates the fact that this safety concept works without the usual muting arms: “What we liked about the concept from the very beginning was that you can save on the entire hardware, ie, the muting sensors. This is not just about the costs, but also about the considerable time saved by eliminating mechanical mounting. After all, cabling and adjustment can become a problem for the commissioning engineers at the construction site if things get more complicated in practice than expected in theory.”
Furthermore, from a control point of view, this solution saves on additional binary inputs and thus lowers costs: this means saving two safe inputs with cross muting and four safe inputs with sequential muting. “This adds up in large facilities like the Heinrichsthaler plant with eight palletising lines and a throughput of 40,000 cartons per day,” Tobias Czempinski emphasises.
Planning production and distribution centres: the more compact, the better
When designing extensive production and distribution centres, planners focus on creating layouts that are as compact as possible. This often means that the space necessary for the safety technology is lacking. For Tobias Czempinski, one thing is clear: “Every half metre needed for additional photoelectric sensors is hotly contested. We have a lot of machines that work with the inline principle, and for muting sensors we would theoretically need an additional half metre each in the infeed and outfeed. With usually ten lines and thus ten palletising machines next to each other in the hall layout, the need for conveying lines increases tenfold. That's why our customers and also our colleagues at the TGW Group are very interested in the sensor-free muting solution from SICK.”
Smart AI solutions shaping Australia's food future
With Australia approaching a federal election in the coming months, the government is stepping up...
Detection and Quantification of Lactose in Dairy Products
The Neogen Megazyme K-LOLAC test kit is a widely used enzymatic assay for the quantitative...
Complete processing lines for savoury snacks: challenges and opportunities
The global savoury snack market faces several challenges and opportunities.