Meet the new 'ZR' rotary oil-free screw air compressor
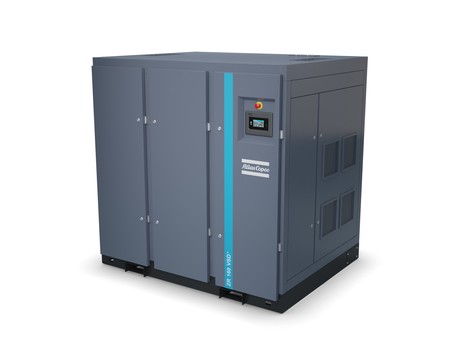
Setting the standard in energy efficiency, quality and reliability
The shortest route to superior productivity is to maximise output while using the minimum amount of inputs. The Atlas Copco ZR 90 - 160 VSD+ compressor series is focused on delivering the greatest volume of 100% guaranteed oil-free compressed air while using the least amount of electrical input energy and with minimal amounts of maintenance intervention.
And not just today, but day after day, year after year, with built-in reliability and durability to ensure very long, trouble-free service life.
Highest reliability
For over 50 years, Atlas Copco Z compressors have set the benchmark for durability. They are built using long-standing internal engineering practices, and are designed and manufactured according to ISO 9001, ISO 14001, ISO 22000 & OHSAS 18001. The high-end ZRVSD+ uses time-proven state-of-the-art screw technology, in-house designed and manufactured electric motors and inverters and provides you with the highest reliability and durability.
100% oil-free compressed air
The ZR 90 - 160 VSD+ offers you 100% pure, clean air that complies with ISO 8573-1 CLASS 0 oil (2010) certification. This means zero risk of contamination of compressed air; zero risk of damage to your products; and zero risk of damaging your company’s hard-won professional reputation.
Maximum energy efficiency
The ZR’s superior oil-free screw elements provide the optimum combination of high Free Air Delivery (FAD) with the lowest energy consumption. Ample sized cooling, low pressure drops and an extremely efficient drive train including motor and inverter result in the highest compressor package efficiency.
The most complete package
With the ZR compressor, Atlas Copco provides a superior solution without hidden costs. The totally integrated, ready-to-use package includes internal piping, coolers, motor, lubrication and control system. The Full Feature version even integrates an IMD or IMDG adsorption dryer to deliver dry compressed air for even the most sensitive applications with virtually no dryer energy consumption. Installation is fault-free, commissioning time is short and no external instrument air is required. You simply plug and run.
Global presence — local service
Our aftermarket product portfolio is designed to add maximum value for our customers by ensuring the optimum availability and reliability of their compressed air equipment with the lowest possible operating costs. We deliver this complete service guarantee through our extensive highly trained service organization, maintaining our position as leader in compressed air.
Your benefits
100% Oil-free Air (Class 0)
- Next generation world class compression element.
- Unique Z seal design guarantees 100% certified oil-free air.
- Atlas Copco superior rotor coating for high efficiency and durability.
- More compact, improved rotor profiles and cooling jackets for maximum efficiency and durability.
Advanced touch screen monitoring system
- User-friendly Elektronikon® Touch, with enhanced connectivity potential.
- Integrated smart algorithms to optimise system pressure and maximise energy efficiency.
- Included warning indications, maintenance scheduling and online visualisation of the machine’s condition.
High efficiency motor
- IP66 Permanent Magnet water-cooled motor with oil-lubricated bearings.
- Class-leading efficiency (IE5 – 97%) and rock-solid reliability.
- Full regulation between 15 to 100% of the maximum capacity.
Optimal control
- Dual motor drive design incorporating Atlas Copco’s most sophisticated Variable Speed technology.
- Reduced energy consumption, operating costs and environmental impact.
- Constantly optimising the motor speed by ensuring optimum performance for every single pressure and flow.
Reliable cooling
- Cooler with highly efficient water separator for higher reliability.
- Stainless steel enlarged surface coolers to ensure top performance over a long lifetime.
- Pipes with star profile form bi-anodised aluminium for preventing corrosion and maximised cooling surface.
- Easily removable for quick, cost-efficient maintenance.
Compact design
- Smallest possible machine footprint on the market.
- Saves valuable and often expensive floor space in a facility.
- Highest ratio flow/footprint on the market.
For more information, visit www.atlascopco.com/en-au or email compressorsau@au.atlascopco.com.
Smart AI solutions shaping Australia's food future
With Australia approaching a federal election in the coming months, the government is stepping up...
Detection and Quantification of Lactose in Dairy Products
The Neogen Megazyme K-LOLAC test kit is a widely used enzymatic assay for the quantitative...
Complete processing lines for savoury snacks: challenges and opportunities
The global savoury snack market faces several challenges and opportunities.