Ishida introduces the latest in bagmaking innovation
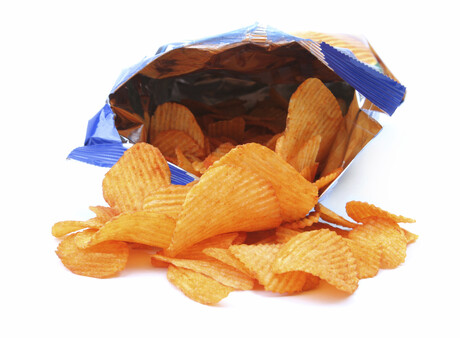
Ishida’s bagmakers are already recognised by snack food processors as the industry benchmark in packaging technology: the popular Atlas bagmaker revolutionised snack bagmaking technology on its release in Australia in 2005 and quickly became an industry benchmark in high-speed snack operations. Its versatile twin-jaw system and continuous back seal system were key to its success in the industry.
Always seeking to improve, Ishida has now released a new model known as the Inspira to provide a solution to industry’s call for more automation and improved efficiency.
The design of Inspira seeks to improve all the most critical areas of the snack bagmaking process: product and film handling, seal quality, accuracy, efficiency, weigher interface, changeover, and control and communication functions.
Improved maintenance accessibility
While the previous Atlas model only allowed access from the front of the machine for maintenance such as changing the forming tube, the Inspira model now has an open frame design with side access with wide opening doors, reducing reach and increasing worker efficiency and safety.
New maintenance features help an operator to act more quickly and more intuitively, removing the need for complex decision-making and unnecessary physical exertion. Among the changes is an LED light in the jaw area to help operator visibility during machine maintenance, and allowing the operator to see jaw surface conditions.
The system can also now be constructed from 316 stainless steel to better support food hygiene requirements.
Innovations in film loading and splicing
Of primary importance in the design of Inspira was improving the efficiency and safety of film changeovers. A new roller design means that film changeover can now be completed with reduced risk of jamming fingers, and enabling the loading of rolls with both hands while increasing the maximum roll diameter to 500 mm. The number of tension rollers has also been reduced from eight to five, further reducing the operator’s workload in feeding the film, and tension rollers raise and lower with the push of a button.
An optional auto splicer has been introduced, which keeps production running by automatically joining the end of the expiring web roll to the leading edge of the new roll, removing the need for operator involvement. Auto tracking enables the new roll to track correctly, and registration mark recognition splices the two rolls together to minimise film waste during changeover.
When the splice cycle is complete, the accumulator is re-filled, and the expired roll can be changed while the new roll is running. Film splicing only takes 20 seconds (as opposed to up to two minutes for manual splicing), and the auto splicer helps prevents human error and reduces film loss. Rapid ROI is possible because of reduced production downtime by 85%.
Improved speed and efficiency
The Inspira bagmaker has been designed to deliver improved packaging speeds, and when integrated with other Ishida equipment, offers a consistent forming and sealing performance of up to 180 bags per minute in production. It can also support bag sizes down to 50 mm.
Higher levels of efficiency and seal quality are achieved with new motor and drive technology, also improving the positional jaw control at the point of sealing. Detection of product in the seal on the Inspira machine has also improved and can detect which jaw (upper or lower) is detecting product in the seal, so a minimum only one bag is rejected (previously two bags).
Inspira also offers reduced energy and air consumption and lowers operating noise levels, with 16.8% less power consumed during operation, 24.8% less power consumed on standby, and a 20.7 db reduction in noise levels.
More intelligent operator interface
One of the biggest areas of improvement is in the machine’s software and HMI.
The HMI screen is now larger at 15.3″ with capacitive touch, and offers easier, more user-friendly operation and flexible screen customisation. Four levels of security (operator, maintenance, engineering, Ishida) give maximum control over the operation and management of the system.
Overall operation can now be customised for specific application needs, whereas previously customisation needed to be performed by Ishida. Up to 500 preset configurations are supported for fast changeovers.
The system also now supports greater levels of maintenance information, adding servo motor speed and torque waveforms, and the machine can self-diagnose and store data for remote maintenance.
Innovation on display at APPEX
After many years of success with the Atlas model, Ishida has continued to invest heavily in R&D and tasked their engineers to continue to explore and to refine its machines in order to provide a solution to industry’s call for more automation, lower maintenance costs and greater sustainability. The result is the Inspira bagmaker that offers a new level of automation and efficiency to consistently produce quality bags, dramatically increasing production efficiency for snack food manufacturers.
The Ishida Inspira auto-splice bagmaker will be on display this year at APPEX, 12–15 March at the Melbourne Convention and Exhibition Centre.
Smart AI solutions shaping Australia's food future
With Australia approaching a federal election in the coming months, the government is stepping up...
Detection and Quantification of Lactose in Dairy Products
The Neogen Megazyme K-LOLAC test kit is a widely used enzymatic assay for the quantitative...
Complete processing lines for savoury snacks: challenges and opportunities
The global savoury snack market faces several challenges and opportunities.