How Handtmann protects the environment and saves money in the dairy and food processing industry
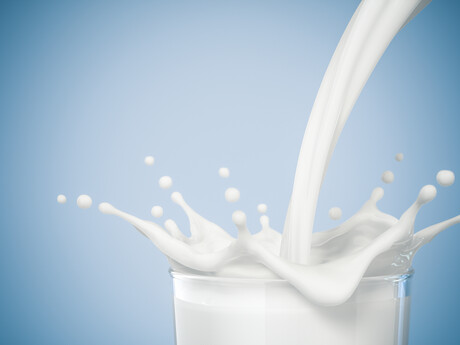
In the bustling world of food production and distribution, every detail matters. For Parmalat S.p.A., a renowned global player in the food industry, the need for efficient and eco-friendly solutions is paramount. Producing a wide range of everyday essentials including milk, dairy products, and fruit beverages, Parmalat always seeks ways to optimize their processes. Enter Handtmann — a name synonymous with innovation and sustainability in food processing equipment.
THE CHALLENGE: ensuring processing equipment is thoroughly cleaned, particularly in processed cheese production. Traditionally, this required a two to three percent caustic solution, which once used, was usually discarded.
THE SOLUTION: Albert Handtmann Armaturenfabrik GmbH & Co. KG. With their expertise in recycling and innovative crossflow system, Parmalat can now recycle dirty caustic and return it for re-use, reducing caustic consumption and thus reducing costs.
The Handtmann CF (crossflow) system is a triumph of environmentally conscious technology. The system filters and purifies the caustic solution, returning it to the central tank, creating a cost-effective and eco-friendly recycling closed loop process. Thanks to this system, Parmalat significantly reduces its chemical waste and costs, conserves water consumption, most importantly reduces discharge to wastewater treatment and energy cost for reheating new caustic batches. Connecting a CIP to a buffer tank is only one option. Alternatively, the customer can operate without a tank or connect multiple CIPs to a single tank.
Crossflow Process, Single Tank with connection to one or more CIP Units
Transform your operations and move toward sustainability with the Handtmann System — a revolution in filtration efficiency.
With a remarkable filter efficiency of 99%, a mid-sized Handtmann system can process approximately 20 cubic metres of contaminated caustic into pure filtrate daily. Handtmann isn’t just a solution for Parmalat; it’s a game changer for various industries. From southern Germany’s processed cheese production to countless other applications, the Handtmann system is proving its worth.
One of our satisfied customers required that the caustic loss should not exceed one percent — a demand met effortlessly by the Handtmann system, but we didn’t stop there.
A bigger Handtmann system was set to a filter capacity of 5.000 litres per hour. Even more impressively, we’ve managed to permanently reduce the COD value (Chemical Oxygen Demand) over 68%, maintaining it well below the limit of 3,500 mg/L set by the relevant wastewater authority.
Imagine a filtration system that works around the clock, seven days a week, and completely automated. A system capable of operating independently, or connecting to other systems via a central, overarching parent system. A system that ensures continuous operation even in the face of unexpected tank failures. This is the reality with Handtmann’s Crossflow Filter Technology. At the heart of Handtmann’s CF system lies the ceramic membrane, a powerful component that can be utilized for microfiltration or ultrafiltration, up to a best case separation limit of 5 kDa (kilodaltons), based on the task at hand. This robust membrane navigates the filtration process with such ease that the alkaline solution passing through it at a temperature of approximately 60 degrees Celsius is a testament to its prowess.
So, what about the Future? Parmalat and Handtmann continue to collaborate after installing Handtmann systems for caustic regeneration in five of nine Parmalat’s Italian plants in 2021 and 2023. The Handtmann system is more than just a piece of equipment; it’s a solution that meets the demands of today and the challenges of tomorrow. It’s a testament to the power of innovation and the importance of sustainability in the food industry.
The CF system’s capabilities extend beyond its impressive operational efficiency. The ceramic module within the system boasts high thermal and chemical resistance, making the CF filter technology not only suitable but also exceptionally durable for corrosive filtration in the food and beverage industry. Our case studies with long term customers demonstrate this durability, with the ceramic membrane performing reliably for more than 10 years so far without exchange. Maintaining peak performance is simple, by weekly descaling of the ceramic module with acid. During this one-hour process, the CF system is temporarily disconnected from the plant. But rest assured, this short break is the only pause in the system’s otherwise relentless operation.
Today, Handtmann’s revolutionary technology is being transferred from the German and European market to global leaders in the food and beverage industry, dairies, and processing production. As regulations for environmental protection increase, and caustic concentrate prices increase, the need to use resources sparingly and sustainably has never been more crucial.
Experience the Handtmann difference firsthand. Now available in Australia & New Zealand to buy or rent for tests. Discover how Handtmann’s technology can benefit your business. After all, every step towards a more sustainable future is a step in the right direction. It’s not just a product, it’s a promise for a smoother, more efficient, cost effective and sustainable operation for your business.
Need more? contact:
i.A. Marc Pfeilsticker
Jr. Area-Sales Manager Asia Pacific
Arthur-Handtmann-Str. 11, 88400 Biberach/Riss, Deutschland
Tel.: +49 7351 342-4535
Mobile: +49 151 7464 7492
Marc.Pfeilsticker@handtmann.de
Sandy Ross
Official Handtmann representative Australia & New Zealand
Rossbrew
58 Walana St, Geilston Bay, Tasmania
Mobile: +61 403 005 248
sandy@rossbrew.com.au
Beyond Dairy: Bega's Commitment to Safety
To support Bega's Safety Principles, Pilz was commissioned to conduct plant assessments...
Welcome to the Family — Neogen Petrifilm Bacillus cereus Count Plate
Last year marked the fortieth anniversary of Neogen® Petrifilm® Plates.
How Bottoms Up Beer saves $12,000 a month with Fishbowl
Unique drafting beer system Bottoms Up Beer handles its ever-increasing order volume with ease...