Finding the ROI in EMP
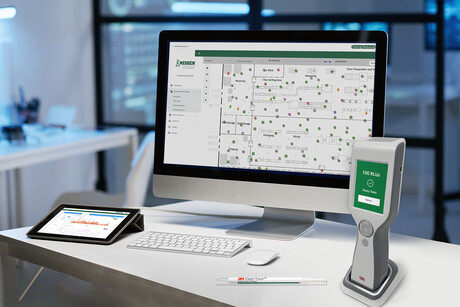
For many manufacturers, food safety is often considered to be little more than a necessary cost centre. Their reactive approach is to try and spend as little as possible while still satisfying regulatory compliance.
However, there are a growing number of forward-thinking food suppliers who have discovered that taking a different approach, using advanced workflow and analytics technology, can lead to greater ROI.
Food safety issues can affect a business in multiple ways. Perhaps the most direct impact comes from wastage. For example, in the United States, one-third of all food manufactured is scrapped. Much of this due to preventable food safety and quality issues.
In processing or manufacturing food, the later that issues are discovered, the more waste is produced. Therefore, rapidly identifying and responding to food safety issues is critical to reducing the costs associated with wastage.
Another costly impact comes from disruption. When a pathogen is found to be present within a production environment, a series of corrective actions must be launched. As corrective actions are being deployed, disruption to production is an almost certain result.
The accumulation of downtime over the course of a year can be staggering. Research conducted in the US found some manufacturers were losing 500 hours annually due to food safety issues, with overall costs estimated to be around $20,000 to $30,000 per hour on average.
While not everyone is operating on that scale, it remains easy to see why the ability to reduce production downtime has become an important focus for the industry. By eliminating just a few delayed starts or unplanned re-cleaning instances, the financial gains can be significant. A business that can recover just one hour of unnecessary downtime per week, could be saving up to $1.5m per year.
Environmental monitoring programs (EMPs) are a standard component of a modern food or beverage production line. They serve to verify that cleaning and sanitation are effective and result in food production environments that produce food safely, free of pathogens, bacteria, and other contaminants that could harm consumers.
However, food suppliers generally lack rapid access to the information and visibility to relevant data that is required to reduce reaction times. Many EMPs are managed via a weekly reporting process that involves collecting data from texting activity, aggregating it, analysing it, and reporting on it on a weekly basis. These information management tasks are often managed within a combination of paper and spreadsheet-based files.
At this pace, several days of production can be at risk of being scrapped when pathogen and bacterial contamination issues are discovered during a weekly review process. The incremental visibility to relevant data needs to be accelerated to near real-time. But with thousands of tests occurring during an ever-moving production schedule, how can food safety and production teams keep pace?
Automated EMP systems enable the realisation of this goal. An automated solution should enable the data itself to drive alerts and point to issues as they are discovered, leaving the weekly reporting and analysis cycle behind. This is accomplished through the definition of rules that trigger the system to analyse diagnostic results data. Any time a value is discovered to be out of range, or outside of the rules (such as a positive diagnostic finding for a pathogen, or a bacterial count above acceptable ranges), the system automatically alerts stakeholders to the existence of such information. This enables near real-time reaction to occur, and the affected food product to be identified and quarantined before the production run is entirely wasted.
To fully realise the potential of current technology, EMP data can be fed into an analytics program that allows food safety professionals to discover the root causes and trends that lead to issues in the first place. In this way, businesses can be more proactive and head off issues before they cause production delays and shutdowns.
Colour-coded test points on your floor plan enable you to visually assess the state of your plant at a glance. You can easily generate schedules to support your company’s environmental testing plan, and with all your testing and corrective action data in one spot, you can filter and print what you need for any audit in minutes.
Forward-thinking food brands and ingredients producers around the world are already realising the ROI benefits that come from the adoption of workflow automation, data gathering, and advanced analytics capabilities.
Neogen is a global leader in food safety, with a product range that protects and enhances all stages of food and beverage manufacturing and a strong local team on hand for advice and support. Our environmental monitoring and analytic solutions, including the Clean-Trace, AccuPoint and Neogen Analytics systems, are versatile and can be customised to meet the specific needs of your business. Let us show you the benefits of reliable and rapid results combined with easy-to-use proactive management of your entire program.
To find the ROI in your EMP — visit Neogen.
Smart AI solutions shaping Australia's food future
With Australia approaching a federal election in the coming months, the government is stepping up...
Detection and Quantification of Lactose in Dairy Products
The Neogen Megazyme K-LOLAC test kit is a widely used enzymatic assay for the quantitative...
Complete processing lines for savoury snacks: challenges and opportunities
The global savoury snack market faces several challenges and opportunities.