Cleaning solution for food and beverage industry
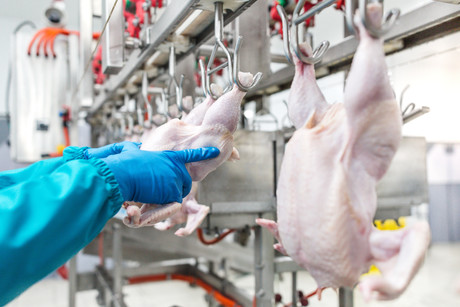
Hygiene and sanitation within the food and beverage industry is imperative to the quality of the output and general success of the operation, especially in terms of productivity, efficiency and effectiveness.
Spraying Systems Co has launched an innovative concept using electrochemical activation (ECA) technology to provide sustainable cleaning solutions for the food and beverage manufacturing industry.
The concept has been brought into two divisions that oversee the commercial and industrial markets with ultimately identical products: Klarion and PathoSans. Both divisions have a dedicated focus to ensure an effective and thorough clean with up to a six-log reduction to bacteria while remaining environmentally conscious about sustainability efforts.
Klarion and PathoSans are generated through the concept ECA technology, creating a powerful and effective two-step on-site generation system without the necessity for dilution or toxic chemicals due to the electrolysed water.
Electrochemical activation technology
Electrochemical activation (ECA) is a technology that utilises electricity to drive a chemical reaction that does not normally occur.
Klarion uses ECA technology to produce eco-friendly chemicals combining electricity, salt and water to generate two separate solutions. The salt used in the Klarion/PathoSans ECA process is 99.5% sodium chloride (NaCl) that is dissolved in water and generates both ions of sodium and chloride.
The Electrolytic Cell is where an electric field is present and allows the sodium and chloride ions to be separated through ion-selective membranes and react with water to create an alkaline cleaner (NaOH) and sanitiser (HCIO).
This is where two separate solutions are generated.
Sodium hydroxide (NaOH) (cleaner) is used as a the ‘general cleaner’ which has the ability to break down organic compounds such as proteins, fat, grease and oil; and hypochlorous acid (HOCl) (sanitiser) is a chlorine-based solution that kills a wide variety of bacteria, fungus and viruses including Listeria monocytogenes, Escherichia coli and Salmonella enterica.
When applied to a hard surface, the HOCI (sanitiser) acts as an oxidising agent. When reduced by the organic matter that it comes in contact with, it doesn’t leave any toxic residues and therefore doesn’t require a post-rinse method making the hypochlorous acid a superior operational solution, saving time, resources and enabling frequent, real-time application.
The design of the Klarion/PathoSans systems keep the salt in the brine solution separate from the electrochemically activated solutions used to clean, which helps in preventing the corrosion of stainless-steel materials.
As the application of ECA technology can vary, Klarion specifically uses superior electrolytic cell design, which additionally provides a longer cell life and a maintenance-free operation.
Production of these chemicals are based on a natural equilibrium. The management of the process is based on the sanitiser’s pH. This is because when in a controlled pH environment within the ideal ranges of 5 to 6.5, hypochlorous acid will exist as the dominant chlorine species allowing for a 30-day shelf life.
HOCI (sanitiser) kills target organisms between 10–60 seconds contact time, making it effective in its cleaning ability as an antimicrobial agent and acts as a significant contributor in the prevention of contamination in piping and clean-in-place systems.
As mentioned, both chemicals produced by this concept can completely replace traditional chemicals that contain toxic properties (which can cause long-term health effects with long-term exposure), so they can minimise workplace risks and improve the health and safety environment of the workplace.
Applications
Any operation that involves a form of cleaning process has the potential to be optimised with the use of ECA generated solutions. These operations include, but are not limited to:
- Beverage
- Poultry
- Meat processing
- Fish
- Hatcheries
- Bakery
- Confectionary
- Egg-shell washing
- Dairy
- General tank cleaning
- Ingredients and commercial applications such as restaurants and bars, etc.
Benefits of ECA
- Environmentally sustainable
- Improves work-place health and safety environment (eliminates need for heavy PPE)
- Allows for on-site and on-demand production of solutions
- Eliminates the usage of plastic containers and transportation of other toxic chemicals
- Reduces pollution associated with the production of traditional toxic chemicals
- Reduction in operating costs
- Reduces down-time for cleaning and maintenance related procedures
Smart AI solutions shaping Australia's food future
With Australia approaching a federal election in the coming months, the government is stepping up...
Detection and Quantification of Lactose in Dairy Products
The Neogen Megazyme K-LOLAC test kit is a widely used enzymatic assay for the quantitative...
Complete processing lines for savoury snacks: challenges and opportunities
The global savoury snack market faces several challenges and opportunities.