Quality control for baked goods
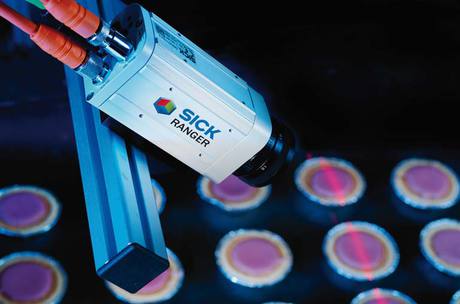
In the production of baked goods, higher brand awareness and customer satisfaction are an increasingly important factor for the manufacturers of baked goods. That’s why these manufacturers are looking to make detailed improvements to the pre-packing quality control process for goods such as bread, cookies and doughnuts to enable the rejection of items which lack the proper shape or colour, before they are packed. Together with additional demands for cost efficiency, this means that optical quality control must be automated and performed at high speed.
Food measuring in 3D and colour
These improvements have to take a wide range of quality aspects into consideration, such as product shape, thickness and colour. Additionally, the presence and amount of topping, as well as the presence and quality of imprinted patterns and logos, must also be monitored. The level of completion of the baked goods and any foreign objects they may contain both need to be identified. In order to take all these attributes into account, the control system must have the capability to measure both 3D and colour attributes at a high resolution. Moreover, the system needs to analyse the measurements and make the correct grading or sorting decision within a limited window of time. The sorting station also needs to include a device for rejecting inferior items.
The need for high speed
System integrator Adbro Controls developed a high-speed rejection system that handles quality control in the food industry. It works with conveyor systems and is designed for integration into existing production lines. The application is built around the ColorRanger E 3D camera from SICK, which provides simultaneous 3D and colour images at high speed. It also features two light sources: one white light source for colour recognition and one line-projecting laser for 3D measurements according to the laser triangulation method. The camera offers a high degree of flexibility, which means that the measuring speed, resolution and field-of-view size can all be adjusted.
Image data from the camera is sent to a PC (host), where software performs image analysis and compares the scanned data with a pre-programmed range of ideal data in order to either feed the item to the next process step or reject it. HALCON’s camera support enables quick software development in the machine vision library. The system tracks the exact position of goods on a conveyor belt and sends the grading decision to an array of pneumatic nozzles mounted in slots above the belts. The nozzles then use compressed air to blow the inferior item off the belt.
Phone: 1800 334 802
Tecpro Australia RB35 washdown gun
At just 440 g, the RB35 washdown gun is designed to provide good performance while also being...
Astech F-Dicer frozen meat dicer
The Astech F-Dicer is designed to cut frozen meat into cubes.
TREIF HAWK portion cutter
CBS Foodtech has introduced the TREIF HAWK portion cutter, which is is suitable for food and meat...