Premium snack maker meets growing demand
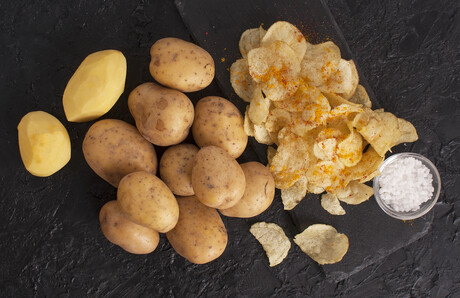
British chip manufacturer Burts has greatly increased production capacity at its manufacturing site in Plymouth, UK, enabled by the installation of the latest high-speed seasoning and packaging system from TNA Solutions.
A growing demand for premium snacks
Burts is a maker of high-quality hand-cooked potato chips based in Devon, UK.
Building on 20 years of experience, the company has a key mission to make delicious snacks for discerning consumers. Using Red Tractor-approved potatoes from local growers, Burts’ crisps have authentic flavours, often featuring ingredients sourced locally in Devon, which the company states are free from MSG, artificial colourings and flavours, and hydrogenated fat.
Since the installation of Burts’ very first seasoning and packaging system in 2006, TNA has worked with the company, providing additional systems as Burts has continued to grow. The latest installation of a ninth seasoning and packaging system at the company’s expanded production facility in Plymouth continues the strong partnership.
Challenge 1: Increasing factory output
As one of the UK’s fastest growing independent snack companies, Burts needed to increase its output to meet growing sales demand. Running 24 hours a day, six days a week, with over 100 SKUs, the company needed equipment that was easy to set up, operate and change over to allow for the many different product types produced at the factory. Given tight production schedules, it was important that equipment only required minimal maintenance to reduce downtime; for this reason, it was essential that the new equipment was reliable.
Solution
Burts opted for a TNA intelli-flav OMS 5 on-head seasoning system and its ninth TNA robag vertical, form, fill and seal (VFFS) packaging solution to be added to twin-lane TNA roflo HM distribution lines. This combination offers gentle product handing, flexibility, consistent seasoning and high-speed, high-quality packaging.
The high-speed bag maker features an extremely short vertical product transfer from the scale to the pack, helping Burts to maximise machine output while minimising product rejects. Operators can easily switch from one bag size to another on the same packaging line, thanks to the lightweight formers.
Meanwhile, TNA’S patented unload assist feature alongside auto-connect, one-touch recipe change functions and a twin film spindle has allowed Burts to maximise OEE with faster product changeover times. An extra benefit was that, as operators were already comfortable working with TNA equipment, operations were simplified post-installation as there was no downtime involved for training.
Challenge 2: Flavour flexibility
Burts’ many flavours, which include Guinness, Chilli & Lime and Maple Pigs in Blankets, are packed in a wide range of bag sizes and multi-packs. This meant a flexible packaging solution was crucial, as multiple flavours are often packed from one batch cook.
Solution
To maximise flexibility, Burts selected the intelli-flav OMS 5, which seasons products directly above the packaging system. The system incorporates tool-less changeover for all contact parts. Changeovers can be completed in under three minutes — significantly minimising downtime by allowing Burts to rapidly change between different-flavoured products.
Challenge 3: Delivering premium quality
Burts says it is committed to making sure every bite of its products delivers “real taste, proper crunch”. The seasoning is an important factor in helping the company deliver on this promise.
Solution
The intelli-flav system precisely controls the seasoning application within the flavouring drum, thanks to a responsive variable-mass seasoning system with a dynamic vibratory conveyor. This enables an accurate, proportional amount of seasoning to be evenly applied for consistent coverage and flavour dispersion.
A long-term partnership
“We place a huge emphasis on choosing the right suppliers and developing partnerships that can contribute to our company’s success,” said John Joseph, Operations Director at Burts.
“We’ve had a commercial relationship with TNA for 16 years, so we’re incredibly familiar with the brand and have seen first-hand the benefits of their cutting-edge solutions, which deliver unrivalled speed, performance and reliability.”
Joseph said TNA’s high-performance solutions had proven robust and reliable, enhancing Burts’ manufacturing capabilities and helping the company to expand operations.
“We are extremely pleased with the new installation and are confident that the new equipment will continue helping us cope with growing demand and meet our long-term goals,” he said.
Phone: 02 9714 2300
ProfilGate clean-off zones
The ProfilGate brush-and-tray system is designed to help keep facilities clean by removing dirt...
RIDAQuick Gluten Quant & Smart Box
The RIDAQuick Gluten Quant & Smart Box from R-Biopharm Australia is used for quantitative...
Endress+Hauser Micropilot FMR43 radar sensor for hygienic processes
The Micropilot FMR43 is a compact radar used for continuous level measurement in hygienic...