Milk processor saves time, chemicals and water by cleaning with Gamajet
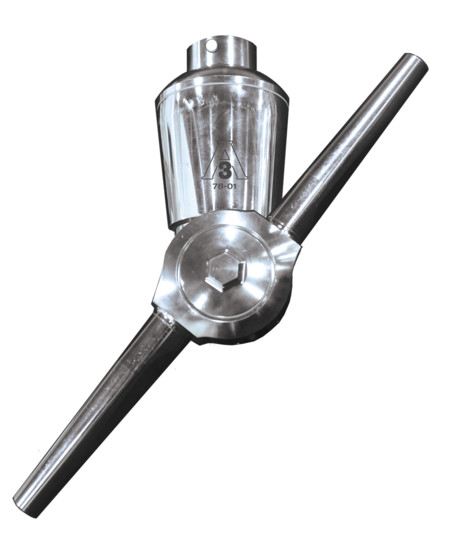
A milk company based in Pennsylvania, US, utilises vertical spray dryers to produce large quantities of milk powder. With sizes of up to 6.7 m in diameter and up to 18 m high, the facility’s spray dryers can produce a total upwards of 4000 kg of milk powder/h.
During the manufacturing process, fluid milk is evaporated to 50% solids and then injected under high pressure into the 200°C environment inside the spray dryer where it flash dries. The dry milk then drops to the bottom of the unit and is discharged into bulk containers.
Vibrators help remove any powder which may adhere to the sides of the cone. However, over time, the milk builds up on the inside of the dryer and must be removed during routine cleaning. In order to maintain high production efficiencies and product quality, close attention is paid to maintaining the cleanliness of the spray dryer interiors.
Until recently, the company utilised traditional spray balls and high-pressure water injection to clean the dryers. The routine cleaning cycle usually consisted of two 45 min wash cycles utilising a 2% sodium hydroxide caustic solution and a 1% nitric acid wash, interspersed with 20–30 min rinses. A thorough cleaning of the entire unit often required up to 16 separate insertions of the spray ball by cleaning personnel into various openings throughout the dryer. This was a very time-consuming and labour-intensive operation to ensure that all the areas were cleaned. Water usage throughout the process was approximately 950 L/min.
With a standard cleaning process to measure against, the company’s manager of engineering and maintenance had the opportunity to install and utilise two rotary impingement cleaning machines manufactured by Gamajet Cleaning Systems, Inc. The Gamajet 4 and Gamajet E-Z8 fluid-driven tank cleaners utilise the cleaning solution for power and provide 360° cleaning with low flow rates and high speed.
The Gamajet 4, because of its greater cleaning power, was inserted inside the large upper chamber and dome of the spray dryer, while the Gamajet 8 was positioned in the smaller-sized bustle and cone located at the bottom of the unit. During the new cleaning cycle, each Gamajet unit is inserted only once resulting in immediate savings in time and manpower.
Results
With the new units, wash times have been reduced to a 15–30 min cycle and often only one wash is necessary. Because of the Gamajet’s high-powered cleaning force, water usage is now estimated to be about 380 L/min. “We estimate that by using the two Gamajet units, we save about two and a half hours in time and around 28,000 L of rinse water per clean up,” the manager said. “And, we also save on the amount of chemicals we use.”
Phone: 03 9583 2368
ProfilGate clean-off zones
The ProfilGate brush-and-tray system is designed to help keep facilities clean by removing dirt...
RIDAQuick Gluten Quant & Smart Box
The RIDAQuick Gluten Quant & Smart Box from R-Biopharm Australia is used for quantitative...
Endress+Hauser Micropilot FMR43 radar sensor for hygienic processes
The Micropilot FMR43 is a compact radar used for continuous level measurement in hygienic...