Maximising yield and minimising waste in dairy processing
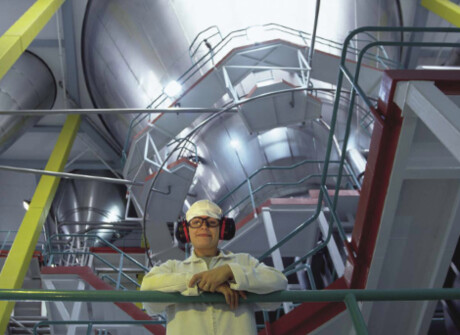
In an environment of high land prices, supply chain challenges, inflation and material availability challenges, dairy manufacturers are looking to make the most out of their existing facilities through optimisation.
One way to optimise dairy processes, reduce waste and maximise yield is to use data to analyse the current situation and make recommendations for improvements.
Rockwell Automation’s FactoryTalk Analytics Pavilion8 Model Predictive Control (MPC) can provide an intelligence layer on top of automation systems which is designed to continuously drive the plant to achieve multiple business objectives — cost reductions, decreased emissions, consistent quality and production increases — in real time.
“Rockwell’s MPC team conducts a full study upfront to show the value that this technology can bring to an operation. In most cases, total ROI is achieved in less than 12 months, and additional value continues to be realised after that,” said Steve Simpkin, Solution Executive – Advanced Process Control, South Pacific, Rockwell Automation.
“This evidence-based approach typically looks at a full 12 months because that takes into account natural variability. In the dairy industry, there’s usually a peak from spring into summer, followed by a quieter period after that, so it’s essential that these variations are part of the overall plant optimisation plan,” he said.
Dairy industry challenges
The dairy industry is faced with unabating pressure on raw materials, maintenance costs and energy costs, all while market competition drives prices down. Additionally, Australian milk production is expected to fall 1% in 2024–2025 with the number of dairy cows in Australia expected to fall 1.6% in this period, according to Agriculture Australia.
If a dairy company experiences undesirable process variability with any continuous process, it could lead to diminished performance, below plant capacity and targets, further exacerbating problems in a tough market.
“With all these pressures facing dairy companies, investing in expensive new capital equipment can be too big of a risk. Instead, it makes good sense to squeeze more out of the existing equipment through process improvements,” Simpkin said.
Rockwell’s MPC technology is designed to continuously assess current and predicted operational data, compare this to desired results, and drive new control targets to reduce process variability, operate within equipment constraints and improve performance.
Sustainability benefits
“Yield and improving the bottom line are often the motivating factors behind utilising MPC technology, but there are sustainability benefits that go hand in hand with process optimisation,” Simpkin said.
“By utilising equipment more efficiently, it can reduce energy consumption and emissions, it can reduce total materials needed, and reduce waste produced, too. You’re doing more with less, so your footprint is lower,” he said.
Pavilion8 is designed to provide real-time data and reporting, so any sustainability benefits can be documented for environmental, social and governance (ESG) reporting.
The technology can also be used in a variety of other food and beverage applications, as well as other industries.
Phone: 03 9757 1111
ProfilGate clean-off zones
The ProfilGate brush-and-tray system is designed to help keep facilities clean by removing dirt...
RIDAQuick Gluten Quant & Smart Box
The RIDAQuick Gluten Quant & Smart Box from R-Biopharm Australia is used for quantitative...
Endress+Hauser Micropilot FMR43 radar sensor for hygienic processes
The Micropilot FMR43 is a compact radar used for continuous level measurement in hygienic...