Keeping milk fresh with an automated order picking system
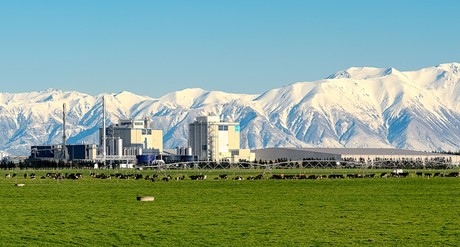
New Zealand-based Synlait Milk will improve material flow and throughput from production to dispatch at its new liquid milk production facility at Dunsandel using an automated order picking system.
Synlait produces a range of nutritional milk products; since 2008, its Dunsandel site has grown to become one of the largest integrated infant formula sites in the world. To expand its product portfolio to include liquid milk, the company is building a new production and packaging facility.
Cimcorp, a manufacturer and integrator of turnkey robotic order fulfillment and tire-handling solutions, will install its MultiPick materials handling solution at the new facility, enabling Synlait to transport 1800 crates from inventory to loading every hour and easily meet production rates of 7000 crates per day. As part of a project with food packaging and processing integrator Tetra Pak, it will fully automate Synlait’s order picking process.
“We’re excited to work with Cimcorp and Tetra Pak to automate the order picking process within our new production facility,” said Neil Betteridge, Synlait’s Director Operations. “The speed and precision offered through automated materials handling will help us streamline operations and maximise the freshness of our new liquid milk products. It will also improve the health and safety of our people, as staff will not be required in cold storage areas for long periods of time. We’ll have a modern facility, ready to meet the demands of today’s food supply chain.”
At the core of the solution will be Cimcorp’s Warehouse Control System (WCS), which will provide control over all inventory management, system functions and pick planning, as well as integration with the order management system.
Cimcorp Distribution Sales Manager Derek Rickard said, “With an automated picking process, Synlait will be able to significantly increase its order fulfillment speed and shorten its lead times, resulting in maximised product shelf life — a critical aspect of the dairy business. Moreover, the WCS software will help Synlait not only optimise material flow with advanced control over product movement and order accuracy, but also collect and provide traceable data to support food safety requirements.”
Installation of the system began in the first quarter of 2019.
ProfilGate clean-off zones
The ProfilGate brush-and-tray system is designed to help keep facilities clean by removing dirt...
RIDAQuick Gluten Quant & Smart Box
The RIDAQuick Gluten Quant & Smart Box from R-Biopharm Australia is used for quantitative...
Endress+Hauser Micropilot FMR43 radar sensor for hygienic processes
The Micropilot FMR43 is a compact radar used for continuous level measurement in hygienic...