Ishida delivers flexibility and quality to muesli manufacturer
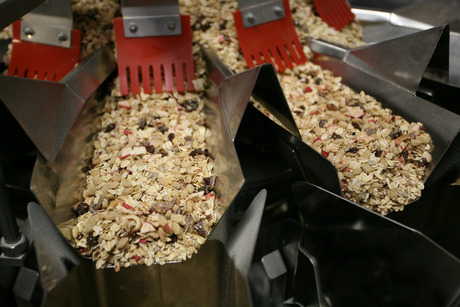
To cope with high demand for its products, German oat flakes and muesli producer Peter Kölln required a packing solution that was able to process a wide range of pack formats and be equally suitable for muesli and extruded cereals. In addition, the company was seeking a high-performance quality control system.
In collaboration with its customer, Ishida Germany devised a high-performance packing line comprising fully automatic multihead weighers and inspection systems to provide flexibility and enhanced quality control.
The Ishida solution, comprising two CCW-RS multihead weighers, an IX-GA-4075 X-ray inspection system and a DACS-G checkweigher, is able to handle a variety of different types of muesli and extruded cereals (which the company markets under the name ‘Fleks’) in different pack formats, with fill weights ranging from 325 g to 1 kg.
The line is capable of speeds of up to 140 packs/min (70 weighments/min/machine), with accuracy to within 0.5% of the target weight. The only factor that prevents the weighers from achieving an even higher output is the low fall speed of the lightweight products.
The pre-mixed muesli and Fleks are fed via a bucket elevator onto the two weighers. The cereals pass through inlet chutes onto the dispersion tables, where the sensitive Ishida loadcell with feedback to the infeed ensures there is an even and consistent product flow to the radial feeders.
All hoppers are equipped with sift-proof hopper doors to prevent fine product from leaking during the weighing process.
A microprocessor rapidly calculates the optimum combination of hoppers that comes closest to the target weight. These dosed portions are then released directly into the packaging machine via a timing hopper. Aluminium-coated film is used for the Fleks, while muesli products are packed into clear plastic bags and later into cardboard boxes.
One particular challenge created by the fully automatic weighing of these cereal products is the amount of dust generated. While the design of the CCW-RS weighers ensures gentle product flow, all contact parts are also electrostatically polished so that dust traps are minimised, preventing product residues suddenly coming loose and landing in a different pack as unwanted cereal clumps. In addition, to prevent dust pollution in the factory, the weighers are housed in a special dust enclosure with air extraction.
After weighing and filling, the packing line, which until then has been split, converges and the products undergo a thorough inspection process. The Ishida IX-GA-4075 X-ray inspection system detects stone, glass and metal foreign bodies that can occur in products containing raisins and nuts. Bags containing product clumps, which are also regarded as a quality defect, are eliminated using an integrated airblast nozzle.
The technology behind Ishida’s X-ray inspection system is based on software featuring an intelligent genetic algorithm. By analysing image data over a number of generations, the machine achieves a high level of inspection accuracy.
Since similar contaminants are usually found repeatedly in food manufacture, the system can, with each inspection procedure, create an increasingly accurate comparison log. A data log collects this valuable information and helps to eliminate recurring sources of contamination.
Products undergo a further quality check before end-of-line packing, where an Ishida DACS-G checkweigher rejects packs that do not meet the correct specifications. The checkweigher is also equipped with a metal detector, which is used when processing muesli for a further foreign body check.
Peter Kölln is already benefiting from its high-performance packing line. Technical project planner Denise Stoldt said that the system is running “really smoothly” in three-shift mode and has reached a stable output. “The crucial factor is the enormous flexibility offered by the new line, which allows us to process a very wide range of products on one system at high speed.” The technical upgrade has also enabled the company to add a new oat flake product to its range.
Phone: 07 3877 6333
ProfilGate clean-off zones
The ProfilGate brush-and-tray system is designed to help keep facilities clean by removing dirt...
RIDAQuick Gluten Quant & Smart Box
The RIDAQuick Gluten Quant & Smart Box from R-Biopharm Australia is used for quantitative...
Endress+Hauser Micropilot FMR43 radar sensor for hygienic processes
The Micropilot FMR43 is a compact radar used for continuous level measurement in hygienic...