How to expand your plant without disrupting production
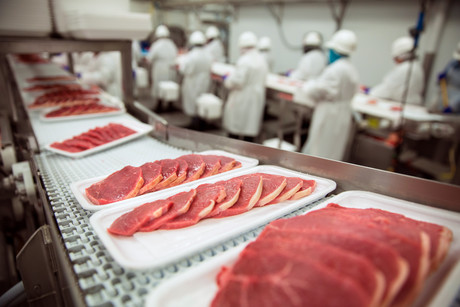
At a large-scale meat processing plant, current production levels were fast becoming unsustainable without expanding operation in the key area of boning. But with operations running continuously at the facility, the challenge was to find a solution that could be implemented with minimal impact on the business.
For any successful business functioning in a production-critical industry, the need to expand operation is often tempered by the prospect of lengthy, unscheduled downtime, disrupted productivity and diminishing profits during the expansion period. The impact of an expansion project can weigh heavily on many companies’ short-term profitability and often delays the decision to expand at all, limiting a business’s growth and, ultimately, its success.
Advanced technology working hand in hand with existing equipment
The existing boning room at the plant was operating at full capacity but simply couldn’t meet current processing demand. All variable frequency drives are housed in the temperature-controlled motor control centre.
Scott designed, manufactured, installed, modified and commissioned a complete turnkey solution for the plant’s process equipment electrical control system. From project inception Scott worked closely with project managers, all the major equipment manufacturers and the plant’s staff: positive and open communication was the key to an effective control system solution designed for the success of the expansion project.
Developing a thorough understanding of all aspects of design fundamentals and operational functions was an essential component in ensuring that Scott manufactured and programmed an operation and control system that would be user friendly, safe and functional within the plant. The control system was designed to incorporate all new and existing equipment to ensure commonality of component supply, operations and controls.
System integration achieved without interruption to beef processing
In order to achieve installation without unscheduled downtime, Scott pre-wired and pre-programmed the equipment prior to installation. Due to the size of the facility, and the location and quantity of I/O required, a fieldbus communications system with distributed I/O incorporating IP66 plug and cable connection systems for I/O devices was used to minimise the amount of field cabling and termination required, and to simplify fault finding and maintenance.
Due to the production-critical nature of the plant, all hardware and software designs focused on ease of fault location, speed of fault resetting by the operator using a touch screen and ‘workarounds’ for when equipment failures occurred. Variable frequency drives networked on DeviceNet were installed in the majority of motors; this ensured the plant operators could tune the operation to various production environments from a user-friendly touch screen.
Maximising downtime minimises disruption: planning for prompt installation
With uninterrupted operation a priority for this project, the installation was scheduled during the only window of opportunity available to them — the Easter public holiday shutdown. Throughout the entire project period the existing boning room, with the exception of the public holiday, remained fully operational. The new boning room meanwhile was readied and in full operational mode in the month prior to Easter to allow for prompt connection of the existing boning room to the new boning room during the public holiday shutdown. Product integration and commissioning followed.
Adding up the benefits
The prompt and fully operational turnkey solution for the process equipment electrical control system expansion project delivered a range of benefits including:
- A user-friendly, safe and functional operation and control system, using proven technology and advances in automation systems.
- Ease of operator use with all faults logically displayed on the touch screens and able to be reset without maintenance involvement.
- Disruption-free plant operation.
- Completion within all project timeline requirements.
- Compliance with all relevant Australian Standards and client specifications.
- Total system reliability and safety.
- Detailed occupational health and safety records and work procedures.
Technology at work
- The system comprises a high-speed, high-performance Allen Bradley ControlLogix PLC platform, featuring common program architecture and common communication networking using DeviceNet for drives and I/O devices.
- For easier connectivity and communication speed, the human machine interfaces (HMIs) utilise Ethernet capabilities; the HMIs are constructed from stainless steel to withstand the 82°C washdown environment.
- The safety system is designed using a Pilz PSS to uphold all safety requirements without diminishing the practicality of overall system operation.
- The complete system is designed in a modular format to provide easy expansion and modular replacement capabilities for maintenance or future system enhancement requirements.
- Where practical all devices and modules comprise a plug-and-replace style format providing quick replacement functionality in the unlikely event of component failure.
- The functional design layout of the Motor Control Centre (MCC), operating consoles and enclosures, and incorporated air-conditioning units ensure ease of operation; the air-conditioned environment within the MCC enclosures provides a stable operating temperature.
- Standardisation of control devices ensures straightforward servicing.
- Where practical, all control concepts remain similar to the existing installation to provide common operational procedures and reduce training requirements.
Originally published here.
Phone: 02 9748 7001
ProfilGate clean-off zones
The ProfilGate brush-and-tray system is designed to help keep facilities clean by removing dirt...
RIDAQuick Gluten Quant & Smart Box
The RIDAQuick Gluten Quant & Smart Box from R-Biopharm Australia is used for quantitative...
Endress+Hauser Micropilot FMR43 radar sensor for hygienic processes
The Micropilot FMR43 is a compact radar used for continuous level measurement in hygienic...