Creating a model microbrewery
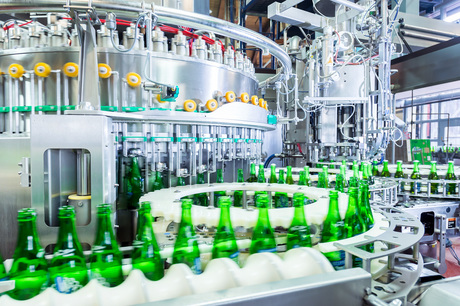
The Steam Whistle Brewery in Toronto, Canada, makes just one type of beer — a bottom-fermented pilsner.
“For our pilsner, we use 100% malt, not adding anything else. It’s a mixture of Canadian, German and Czech brewing methods. Light-tasting, not too dark, not too bitter, but still full-bodied,” explained brewmaster Marek Mikunda.
Brewery expansion necessitated the installation of a new bottle filler and bottle washer, so Steam Whistle turned to Krones, which had supplied a Volumetic VOC can filler with a Ferrum seamer a few years before.
The set-up has now evolved into a model filling operation for other microbreweries, according to co-founder and president Cam Heaps, with oxygen pick-up at the bottle filler only 17 ppb, and 50 ppb at the can filler. Heaps said the consistency of fill level accuracy has also been significantly improved, and the Lavatec E2 bottle washer runs without a hitch.
For brewmaster Mikunda, filling quality is paramount. “What’s crucial in my eyes is not the output but the low oxygen pick-up and the good overall microbiological situation. Our beer is not pasteurised but downstream of the bright-beer tank is ultrafiltered, using deep-bed filtration, arrives at the filler in zero-bacteria condition, and that is how we want things to stay.
“With the two Krones fillers, we can safely assume that even after eight hours of operation they are still in microbiologically flawless condition,” Mikunda explained. This is of particular importance, because at Steam Whistle the storage and fermentation area and the filling operation are not topographically separated from each other.
At present, the Modulfill HRS counterpressure filler runs at 12,000 bottles/h, with 18,000 bottles/h being the maximum output settable.
When Mikunda joined Steam Whistle in 2005, production output was 23,000 hectolitres. Since then, it has almost quadrupled, and any expansions have been handled during ongoing operation. The most recent addition was the commissioning of a semiautomatic Steinecker TFS filter, which “runs like clockwork”, he said.
Phone: 02 9475 9000
ProfilGate clean-off zones
The ProfilGate brush-and-tray system is designed to help keep facilities clean by removing dirt...
RIDAQuick Gluten Quant & Smart Box
The RIDAQuick Gluten Quant & Smart Box from R-Biopharm Australia is used for quantitative...
Endress+Hauser Micropilot FMR43 radar sensor for hygienic processes
The Micropilot FMR43 is a compact radar used for continuous level measurement in hygienic...