Coca-Cola chooses CompAir compressor for Turkish plant
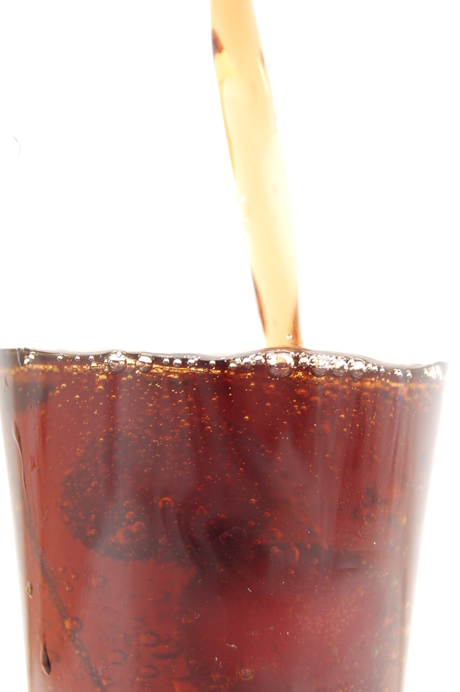
Coca-Cola Icecek produces nearly 60% of all bottled carbonated drinks consumed in Turkey, operating six facilities across the country.
In a sterile bottling environment the need for clean air is paramount, but manufacturers also need to conserve energy.
The company’s Corlu plant produces 50 million cases of soft drinks every year, and energy costs in Turkey are high — around US$0.10 per kWh. So, when selecting new compressors for the factory, reliability and energy efficiency were key considerations.
Josef Tari at CompAir’s Turkish distributor, Tahas, explained: “With no oil being used in the CompAir D75H SR oil-free compressor at all, plus water-lubricated bearings, there is no risk of product contamination and no environmental costs associated with oil disposal”.
He continued: “The CompAir D75H SR oil-free compressor, with its efficient, switched-reluctance, variable-speed motors balances energy input to air demand, ensuring that energy isn’t wasted and reducing running costs.”
The new Cold Aseptic NR PET line (CAF) and the new PET line are using sterile oil-free air.
If both production lines are working, a turbo compressor provides the majority of the compressed air with top-up air supplied by the D75H SR. When only the PET line is in operation, just the D75H SR is used, supplying all the air needed.
Selim Mizrahi, Coca-Cola Icecek’s engineering services manager, said: “As with most beverage processing plants, we have variable shift patterns that result in inconsistent demand for compressed air. To ensure efficient compressed air operation, we chose a variable-speed compressor from CompAir to work alongside the fixed speed turbo compressor, to achieve optimum energy and operational cost savings.”
Phone: 1800 634 077
ProfilGate clean-off zones
The ProfilGate brush-and-tray system is designed to help keep facilities clean by removing dirt...
RIDAQuick Gluten Quant & Smart Box
The RIDAQuick Gluten Quant & Smart Box from R-Biopharm Australia is used for quantitative...
Endress+Hauser Micropilot FMR43 radar sensor for hygienic processes
The Micropilot FMR43 is a compact radar used for continuous level measurement in hygienic...