Factors to consider when choosing between bubble leak testers or vacuum decay leak detectors
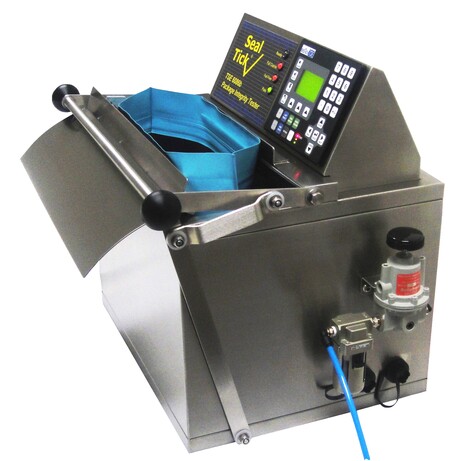
Ensuring package integrity has always been a critical concern for food manufacturers as a leaking package can compromise the quality of their products. They utilise special testing systems to develop test standards to ensure that a package is leak-proof and has maximum shelf life. The tests are performed before products are dispatched and sent off to the market.
There are two commonly known leak testing systems; bubble leak testing and vacuum decay leak testing. Bubble leak testing is the simplest and cheapest leak testing system in which leak testing is performed by submerging packages underwater and checking for bubbles. On the other hand, vacuum decay leak testing is non-destructive and it relies on measurement of vacuum decay using a highly sensitive differential pressure sensor to detect leaks in the package.
There are several key points to be considered when choosing the suitable system for your process.
Labour & cost effectiveness
The bubble leak tester heavily relies on the operator to make judgement. Operators can easily operate this machine without training and discard the packages after testing. The test results are subjective and are not very reliable when the same operator operates the equipment for long period of time. This system is also not suitable when a large amount of testing is required.
The vacuum decay leak tester offers quantitative results and does not rely on operators to make judgements. It can finish one test in less than 15 seconds, allowing large numbers of tests to be conducted. This gives more confidence to the manufacturers about the seal integrity of their packaging passing the standards.
Waste
Using bubble leak testers also introduces more waste in the production process. When packages are submerged underwater and put under vacuum, it compromises the package and its content which makes it unsuitable for consumption. There is also the risk of cross-contamination between multiple products. Therefore, the tested package must be discarded after testing.
This testing system is inefficient when large numbers of testing are required. It is also not suitable for testing high-value products such as milk powder.
The vacuum decay leak tester utilises the non-destructive testing principle by measuring the vacuum decay to identify leaks in the packaging. Therefore, the packages are not compromised and can be returned to the production line if they pass the test. It is also optimised for testing large numbers of packaging and can be easily implemented in many production lines as each test can be completed in less than 20 seconds.
Quality control
The results obtained from the bubble leak tester are subjective and operator-reliant. The results need to be manually logged for operators to identify the test results. Vacuum decay leak testers are semi-automated systems that offer quantitative results that can be logged into the internal memory of the machine. The data can be easily exported to PC via USB or ethernet interface for quality control and traceability.
Packaging design
Manufacturers should also consider whether it is essential for them to identify the location of leaks in the packaging. The location of leaks may indicate faults in the packaging line which assists the engineers to troubleshoot the issue.
The bubble leak testing system is a more suitable option for this application as leak locations can be visually observed by the operators. The vacuum decay leak detector can only determine whether the package leaks, however, it is unable to tell the exact leak locations.
In most applications, it is beneficial to have both testing systems in the production line. The vacuum decay leak tester can be used for rapid leak testing and quality control. If the packaging fails the test, the compromised packages can be tested in the water bath leak testing system to identify the location of leaks.
Circular Solutions for Packaged Waste
Australia's food and beverage industry is increasingly focused on improving sustainability by...
Safer, Smarter Labelling from PPC
As awareness of food allergies grows and regulations around food safety become more stringent,...
Stay Ahead of Food Safety Regulations with PPC's Allergen Management Labels
PPC's card printer-based price tag solution allows users to produce hygienic, food-safe...