Environmental and efficiency benefits of low temperature adhesives
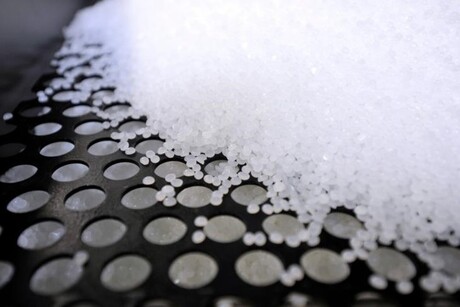
In today’s competitive economy, manufacturing is all about efficiencies and throughput as they work to supply retailers with consumer goods. However, manufacturers also need to consider environmental objectives and targets, as well as customer expectations. Increasingly, consumers are concerned about the environmental consequences of packaging, with many consumers preferring sustainable, eco-friendly options. Therefore, sustainability must be a priority for businesses.
Packaging materials such as paper, wrap around cases, carton and cardboard require bonding in a fast-paced environment. Ideally, these applications use hot melt adhesives, however, the application process tends to involve high temperatures (typically applied at 177°C) possibly causing health and safety hazards and resulting in high energy consumption. With more than one-third of carbon emissions coming from electricity consumption, huge emission reductions and therefore savings can be made by improving the energy efficiency of businesses, says WWF Australia. When overheated or left in the melter for extended periods of time, traditional hot melts are prone to degradation, which can result in charred fragments causing plugged nozzles to pop open during production. These problems undoubtedly increase machinery downtime and operational cost which hurt the efficiency of manufacturing.
Fortunately, it is possible to choose low application temperature hot melts, which help overcome those issues. The world leading adhesive manufacturer Henkel plays a role in reducing environmental impact, improving production efficiency and worker safety with their latest development TECHNOMELT® Cool hot melt adhesives, which are applied at lower temperatures — up to 40% less compared to conventional hot melts. Simultaneously, they allow for higher machine speeds, contributing to increased energy efficiency and productivity for packaging lines.
“Laboratory research and tests at our customers’ sites have confirmed that every 20°C decrease in hotmelt application temperature halves its chemical reaction speed. This leads to multiple processing and performance benefits, like better thermal stability, shorter machine start-up time, longer usability of the adhesive and last but not least, lower risk of char build-up leading spare part cost savings,” said Gunter Hoffmann, Head of Hotmelt R & D Henkel.
This reduced application temperature maintains adhesive stability, prolongs equipment life, decreases maintenance costs and improves start-up times. Melting point is 38°C less than conventional hot melts, the TECHNOMELT Cool drops below burn temperatures nine times faster and avoids potential burn hazards. They require less energy to melt and enable manufacture to reduce the brand owner’s carbon footprint along the lifecycle of the adhesive. At the same time, they are easy to apply and cure fast. This combined with the minimised maintenance intervals results in improved overall performance of the packaging line. Additionally, the lower melt point makes TECHNOMELT Cool adhesives suitable for temperature-sensitive contents like frozen foods and confections and reduces the risk of heat transfer.
More than ever, “consumers, brand owners, regulators and the industry demand change, and the use of bio-based material in consumer goods and packaging is an important driver for sustainable sourcing and a lever to reduce environmental footprint”, explains Jenna Koenneke, Global Head of Market Strategy for Consumer Good Adhesives at Henkel. For example, 70% of consumers are willing to pay more for a sustainably sourced and manufactured product. The TECHNOMELT Cool Adhesives can assist businesses in achieving a more holistic sustainable packaging option, which consumers are increasingly prioritising.
For more information, visit our website www.henkel-adhesives.com/au/en/insights/technomelt-cool-sustainability.html or email: solutions@henkel.com.
Circular Solutions for Packaged Waste
Australia's food and beverage industry is increasingly focused on improving sustainability by...
Safer, Smarter Labelling from PPC
As awareness of food allergies grows and regulations around food safety become more stringent,...
Stay Ahead of Food Safety Regulations with PPC's Allergen Management Labels
PPC's card printer-based price tag solution allows users to produce hygienic, food-safe...