Ensuring seal integrity of your food packaging
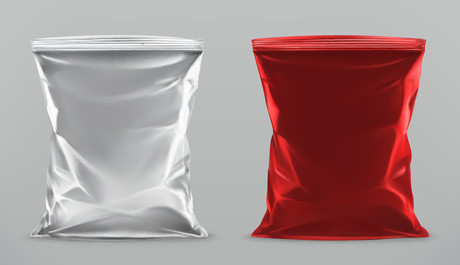
Food and Beverage manufacturers put the utmost priority on ensuring the seal integrity of their product package. Products such as to-go snack packets, milk or coffee powder, pet food, blood bags, blister packs are prone to contamination by organic compounds such as moisture or air. These foreign contaminants may leak into the packages and accelerate the food decomposition process. When it happens, consumers may find that their products have been compromised when they open the packages at home.
Therefore, it is an absolute necessity for manufacturers to ensure that the finished products are properly tested for seal integrity to allow the product to maintain its maximum shelf life.
Consequences of compromised packaging
In the scenario where contamination occurs, there is an increased possibility that the quality of the product has been compromised upon reaching the consumers. The consumers may or may not be aware of this fact, which significantly raises the risk for food poisoning. For high-risk individuals such as the elderly or children under 5 years, the consequences may be fatal. This will definitely result in massive product recalls and cause the company financial loss as well as tarnished brands or images. And, it is often not easy to recover from such situations.
Therefore, implementation of good packaging and seal integrity testing solutions in the production line is essential to ensure that the packages are properly sealed to avoid contaminations. Leak testing devices are one of the popular technologies that are used for this purpose. There are a wide range of leak testing systems available in the market. A device suited for one application may not be ideal for another. Manufacturers can decide which leak testing systems are best suited for their factory depending on the types of packaging and the testing requirement.
Conventional package leak testing method
Underwater leak tester is a traditional leak testing method by submerging the testing package underwater. The water-filled test case is supplied with a constant vacuum within the chamber and a steady stream of bubbles rising from the location of the leak is observed if any leaks are present in the package. The vacuum level can be freely adjusted depending on the testing requirement.
The underwater leak tester can be used for testing different types of packaging and multiple packages can be tested simultaneously. Examples include flexible packaging such as in snack food or health products and pharmaceutical packaging such as bottles or vials. However, the water bath testing system is destructive, which means the tested products are not suitable for consumption after testing and should be discarded. Furthermore, the testing process and leakage assessment are heavily operator-dependent as they need to manually observe the test package to determine leakage. This gives less reliability and more room for error during long-term testing as fatigue accumulates.
Quantitative, non-destructive leak testing system
The non-destructive package leak testing system is developed as alternative to the conventional water bath tester. The equipment generally operates on the vacuum decay testing principle. This testing method is generally suitable for testing the integrity of non-porous, rigid and flexible packaging. The test is initiated by placing the test item into a test chamber, which is evacuated to a preset vacuum level. The rise in the vacuum decay is monitored for a predetermined length of time using a differential pressure transducer. These parameters are used to determine leak in the package.
The non-destructive leak tester is reliable and able to provide accurate results in just 5–20 seconds. It is housed in a robust, stainless steel housing for applications in production and manufacturing environments. However, this testing method is not suitable for all types of packaging. Firstly, it requires the tested package to have a free head space. Therefore, it is not suitable for testing vacuum sealed products such as those used for packing meat products. It also requires the content of the package to be dried as presence of moisture may mask the actual leaks in the package.
What Bestech Australia can offer
At Bestech Australia, we supply an innovative leak testing system from Sealtick, ranging from the conventional water bath tester to the innovative non-destructive vacuum decay leak tester. Our non-destructive leak detection machines can test an item within 5–20 seconds and provide quantitative results which can be retrieved via Ethernet or USB for quality traceability. The test is completely dry and non-destructive and the tested packages can be returned to the chamber upon testing, which minimises waste in the process. This machine can be used for testing almost all types of packaging, provided the package contains headspace.
The testing reliability of this vacuum decay method depends on the free space in the chamber and the sensitivity of the pressure transducers in detecting the small rise in vacuum. To improve the testing reliability, Sealtick design different types of test machines which are optimised for testing different types of packaging such as cans, flexible bags and heavy bags. For testing can products, a support platform is inserted into the test chamber to minimize the air space between the chamber and the can. For testing heavy bags, the system is designed as a horizontal test bed to make it easier to put the packaging. Similarly, flexible packages can be tested in either our bench top unit or mobile trolley unit for testing a larger size package. Depending on the type of testing requirement you have, we have the solution for you.
Case Study: The Food Company — Scaling Production with Packserv
For nearly 45 years, The Food Company has been a trusted name in premium condiments, supplying...
Circular Solutions for Packaged Waste
Australia's food and beverage industry is increasingly focused on improving sustainability by...
Safer, Smarter Labelling from PPC
As awareness of food allergies grows and regulations around food safety become more stringent,...