Sausage production transformed with linerless labelling
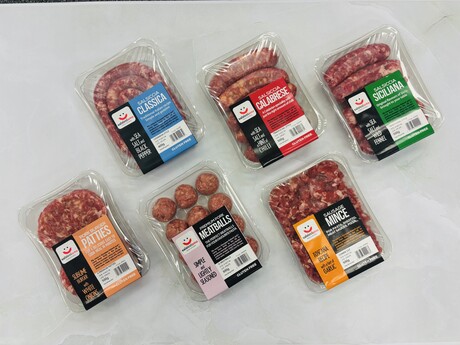
The switch to Ravenwood’s linerless technology and the integration of a Nobac 5000 linerless applicator has had a transformative impact across many areas of the UK-based Italian sausage producer’s business.
Salsicciamo, an award-winning artisan sausage producer, has switched to linerless labelling. The switch has streamlined business operations, and provided it with increased flexibility, cost savings, faster labelling application speeds and enhanced sustainability.
Giuseppe Roberti, Salsicciamo’s Founder, said: “We have seen numerous improvements, the most significant being our transition from manual label application to fully automated labelling lines.
“Since moving to linerless, we are now experiencing faster labelling speeds, enabling us to pack and label a wider range of products more time-efficiently.”
Application speeds have increased by 133%, which has enabled quicker order turnarounds for retailers. Previously, sausage packs were labelled by hand at a rate of about 15 packs per minute. Since fully automating with linerless, production has now reached 35 packs per minute.
Roberti added: “Linerless labels are extremely cost-effective and we are seeing a 50% saving on material costs when compared to the self-adhesive labels we were using previously.”
Linerless materials go directly from the mill to the printer, eliminating the need for costly conversion processes associated with self-adhesive labels. By eliminating the liner and silicone, no waste is sent to landfill.
When comparing self-adhesive to linerless labelling, the label dimensions of the self-adhesive labels were entered into Ravenwood’s CO2 calculator. These results showed that for each reel of 3000 labels, 13 kg of CO2 emissions are prevented from entering the atmosphere. Additionally, this also means that each reel saves 83 m2 of liner from being sent to landfill. On considering the full spectrum of benefits, Salsicciamo purchased a Nobac 5000 linerless applicator with a 53 mm coder.
Roberti said: “The Nobac 5000 can reach speeds of 100 packs per minute and has future-proofed our production line.”
Salsicciamo challenged Ravenwood to develop a single flexible labelling format that could accommodate multiple tray sizes. Their sausage products were packaged in four different trays, all with the same width and length but varying heights. Roberti also wanted the labels applied along the narrow edge to maximise shelf space in retail stores. Ravenwood’s Keyline Designer created a c-wrap linerless label design that meet these requirements.
Roberti said: “Using the same label size for all of our sausage products has made things so much easier. We no longer have to adjust the label applicator’s settings, which has really streamlined the labelling application process and enabled us to work much faster.”
Before adopting linerless labels, Salsicciamo used a self-adhesive desktop printer to print the self-adhesive labels, which were then manually applied. With the installation of the linerless applicator, labelling processes have been completely transformed. Previously, the staff found the manual application process to be slow and repetitive, requiring them to spend a significant amount of time in a cold environment. With more time freed up, staff are able to assist in other areas of the production line.
Founded in 2014 by Roberti, Salsicciamo operates under Carnevale and is headquartered in London, with a nationwide distribution. Its Italian sausages are crafted from UK-reared pigs and are ‘made by Italians in the traditional Italian way’.
Phone: +44 1284 749144
Henkelman Titaan 110 automatic belt chamber vacuum packer
The Henkelman Titaan 110 is a fully automatic single chamber vacuum packaging machine.
Domino Mx Print & Apply Labelling
Domino's Mx-Series Print & Apply Labellers are designed to improve labelling accuracy and...
Paksmart PC40 Cartoner
Paksmart PC40 Cartoner is designed to provide budget-friendly automation with rapid ROI.