Brewery safeguards beer quality with glass filler
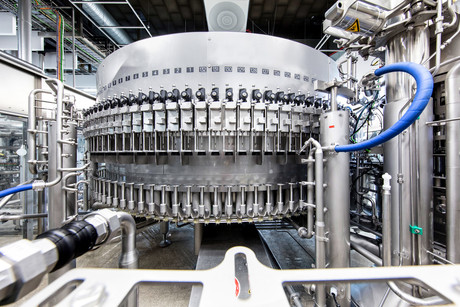
German brewery Rothaus has installed an upgraded glass filler from KHS to ensure high-performance beer bottling.
KHS’s Innofill Glass DRS filler has been adapted with a number of new features, and Badische Staatsbrauerei Rothaus AG is its first customer. The flexible inline machine has 132 filling stations for up to 50,000 bottles per hour, and allows Rothaus to fill 0.5 and 0.33 L bottles. KHS said it provides hygienic filling with low CO2 and product consumption.
Fast format part changeovers ensure a high level of flexibility during production planning and line efficiency. According to KHS, the hygienic QUICKLOCK fast-acting locking system cuts conversion time for fillers with a crowner by up to 33% to just 15 or 20 minutes.
“Simple lever knobs not only release and lock parts, they’re also robust and can withstand broken glass or chemicals,” stated Ludwig Clüsserath, Head of Filling Technology Development at KHS.
Bottle breakages are prevented with the patent-pending SOFTSTOP system. This compact, hygienic bottle flowgate is activated at full power. A light barrier measures the distances of the containers as they are fed into the filler, and a brake wedge then gently decelerates the bottle flow. The filling process and foaming can take place at a high output, ensuring stable filling quality, and the new braking ramp means that there is no additional scuffing and less noise.
The DIAS diagnostic assistance system logs the filling process. Pressure sensors in every filling valve monitor the pressure, time and step sequences without interruption, so any deviations from the target values are immediately recognised. The evacuation and CO2 purging processes are monitored to ensure low oxygen pick-up. Broken bottles are consistently detected across the processing angle and a bottle burst routine triggered. The sensor data can be invoked as a pressure graph on the monitor.
“This gives operators the chance to detect any faults as quickly as possible,” said Clüsserath.
It makes fast, targeted repairs possible, relieves operator workloads and provides a basis for preventive maintenance. By evaluating the data, future sources of error can be eradicated in advance, ensuring consistent quality and the continuation of ongoing operation.
In the camera-controlled OPTICAM HPI control system, the foam generated by HPI displaces the residual oxygen from the bottle. As the foaming is dependent on various parameters in the filling process, the OPTICAM system enables the head of foam to be constantly monitored and regulated irrespective of the machine operator. This means that Rothaus can not only prevent undue beer loss due to excessive foaming, it also detects and rejects bottles with insufficient foaming. If the beer error rate becomes too high, production is stopped and the operators can read off the cause of the fault from a clear analysis report.
With the inclusion of the SOFTSTOP, DIAS und OPTICAM options, the KHS system at Rothaus safeguards the quality of the beer throughout the entire filling process.
Phone: 03 9335 1211
Henkelman Titaan 110 automatic belt chamber vacuum packer
The Henkelman Titaan 110 is a fully automatic single chamber vacuum packaging machine.
Domino Mx Print & Apply Labelling
Domino's Mx-Series Print & Apply Labellers are designed to improve labelling accuracy and...
Paksmart PC40 Cartoner
Paksmart PC40 Cartoner is designed to provide budget-friendly automation with rapid ROI.