Bacon maker goes linerless with its packaging
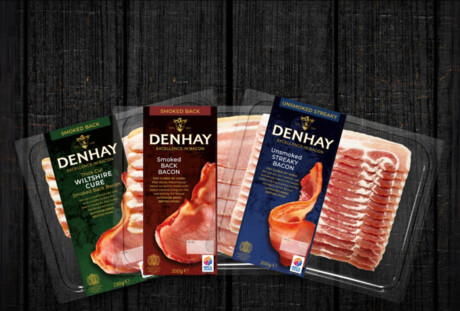
Based in the UK, Denhay Farms has been producing bacon using its own curing process for almost 30 years. The business has now fully automated its packaging operations by integrating Ravenwood’s linerless technology for its bacon sleeves. The move has resulted in a reduction in labour and a boost in production line efficiency.
Two Ravenwood Nobac 5000 linerless applicators have been installed by the bacon business, and it has also partnered with a UK-based linerless printer, ProPrint Group, to produce the new linerless sleeves.
The linerless sleeves resemble traditional hand-applied sleeves but come supplied on a roll.
“We’re absolutely thrilled with how seamlessly the linerless applicators and our new linerless sleeves have integrated into our production process. The machines have transformed our labelling operations, making it faster and more efficient, while the sleeves provide a premium, high-quality solution that perfectly complements Denhay’s brand,” said Jim Loescher, MD of Denhay Farms.
Prior to linerless, employees spent long hours performing repetitive manual sleeving tasks. The transition from labour-intensive hand sleeving to fully automated labelling has been implemented across all Denhay’s own-label sliced bacon including the Spoilt Pig brand, and wholesale catering packs.
The two Nobac applicators have fully optimised the production lines. They can sleeve a variety of fixed-weight pack formats and tray sizes, linking seamlessly to weigh scales for variable weight packs as well as check weighing. However, in this particular application they are not connected.
Denhay wanted to achieve a premium look for the packaging. Ravenwood’s linerless sleeves, supplied on a roll and cut to size by the applicator, are designed to meet these aesthetic standards. The pressure-sensitive board reels are available in slideable or non-slideable versions, to provide a seamless finish. With no backing paper, linerless can also provide a sustainable solution.
The transition to linerless has not only improved packaging efficiency but also reduced storage and shipping space due to the compact nature of linerless reels compared to traditional manual sleeves.
“This transition has been a true ‘win-win’ — not only have we enhanced our labelling processes, but our team is also much happier with the new system. We’re so impressed with the results that we plan to expand the use of linerless technology across other products in our bacon range,” Loescher said.
Phone: +44 1284 749144
Henkelman Titaan 110 automatic belt chamber vacuum packer
The Henkelman Titaan 110 is a fully automatic single chamber vacuum packaging machine.
Domino Mx Print & Apply Labelling
Domino's Mx-Series Print & Apply Labellers are designed to improve labelling accuracy and...
Paksmart PC40 Cartoner
Paksmart PC40 Cartoner is designed to provide budget-friendly automation with rapid ROI.