Meat processing: do you know which cut is more profitable?
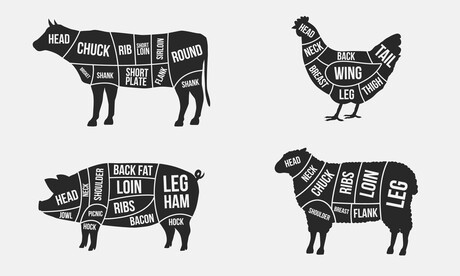
Visibility of actual daily costs by work centre are critical for large-scale meat processing plants.
Many red meat processors have prioritised investment in new equipment, automation and robotics to reduce direct labour costs — in preference to sophisticated costing systems. But Peter Daniliuc, Managing Director of Profit Channels Management, explains how costing modules can provide the accuracy and granularity required to drive genuine product mix optimisation.
Using a lamb processing example, he said: “The relative range and complexity of cuts can generate over 10,000,000 individual carcase cut combinations. And with carcase profit contribution so dependent on yields and processing times, the accuracy of costing data by SKU can often be the difference between profit and loss, when fixed overheads are taken into account.”
“Consider the high-level process flow of a typical lamb processing plant and focus on one particular area, the boning room (processing and packaging).
“For many manufacturers, variable costs — direct labour, utilities, consumables, indirect labour, packaging, etc — are allocated to a carcase, primal or linear cut level.
“Factors that are often overlooked or are grouped as general allocations include:
- individual cut complexity
- variations in yield between cuts within the same linear group
- impact on boning room throughput volumes
- packaging complexity and risk of damage/leakage
- order quantities and impact on labour planning.
“Variations in excess of $1.00/kg for essentially the same product, in a single work centre, can lead to significant opportunities to optimise carcase cut combinations.
Daniliuc said this costing variation can lead to significant opportunities to optimise carcase cut combinations, which can realise savings without the need to invest in new equipment or personnel.
Case study: Poultry processor uses costing system
In 2009, a large Australian-based poultry processor installed the ImpactECS system by 3C Software to solve an issue with insufficient visibility into product costs associated with assembly and disassembly processes.
The processor was experiencing limitations with its home-grown system and spreadsheets. It was unable to forecast fully costed optimal production using its cost-based data.
ImpactECS is a dynamic cost and profitability system which provides an environment for users to rapidly implement a costing system. The system was installed for the poultry processor to deliver product costings, scenario analysis and detailed profitability analysis.
The system can calculate costs for raw material yields for both disassembly and reassembly processes based on cut, range and location at the plant. It can also:
- determine standard versus actual cost variances at BOM level
- calculate complex meat valuation based on market price, sales price and actual cost
- allocate labour on a variety of methods, departments and rates (per bird, kilogram, and tray)
- develop costing analytics sandbox for product development to calculate costs from concept to finished product.
Scenario analysis can be performed to test the effects of changes to material, labour, overhead and other KPI changes on profit performance. This can help to determine optimised production outlook based on forecasted cost data and enables granular level operational modelling to predict outcomes, compare or simulate revenues and costs at any stage across the value chain.
The results
The system provided a fully costed production plan for the poultry processor, which was designed to optimise material value, labour efficiencies and process flows. The results included:
- optimised production efficiency with the primary poultry processing time at every plant reduced to just 2 hours
- detailed activity cost data provides P&L visibility for individual products and locations
- scenario analysis capabilities provide ability to rapidly predict how market changes will impact performance.
The ImpactECS system by 3C Software is distributed in Australia and New Zealand by BMA Group.
Phone: 02 9884 8499
Timmer quickLIFT and heavyLIFT vacuum hose lifters
Timmer has a range of vacuum hose lifters for safely lifting and lowering heavy goods.
Key Technology Iso-Flo, Impulse, Zephyr and Marathon vibratory conveyors
Key Technology introduces high-capacity vibratory conveyors for advanced food-handling applications.
Sidel RoboAccess_Pal S robotic and cobotic palletising solution
RoboAccess_Pal S, Sidel's latest robotic and cobotic palletising solution, will be in action...