Efficient process-controlled access guarding without muting sensors
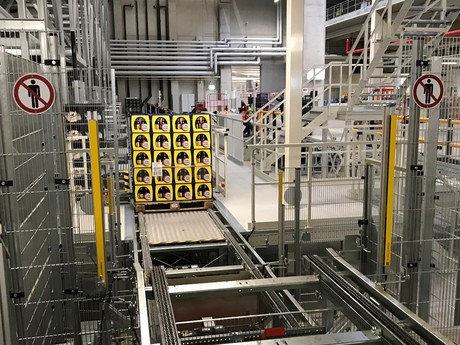
Based in Germany, WITRON specialises in the planning and realisation of warehouse and order picking systems in the field of intralogistics. The company is constantly striving to develop better, more cost-efficient and safe logistics solutions for its customers. In the area of automation and further optimisation of warehouse logistics, the selection of suitable partners also plays a decisive role.
When man and machine meet in a mechanised environment, it must be possible to stop machine and system parts within a fraction of a second. “The safety of all persons who work in one of the many logistics centres of our customers around the world — whether in industry, retail or service — is the asset most worthy of protection,” explained Stephan Schmid, Project Engineer in the area of development and control technology at WITRON. This means that appropriate areas are equipped with safety devices or fencing that meets the applicable standards and norms so as to eliminate accident risk before it can even occur.
But because it is not possible to completely fence in all areas in which man and machine meet in a networked, mechanised system, WITRON is working on systems such as conveyor lines with safety light curtains that must reliably distinguish between people and merchandise.
Especially in intralogistics and in the automotive and packaging industries, affected areas must be safeguarded by optical safety sensors.
To unambiguously recognise transported goods as they approach a protective field and to bridge this for passage of the goods at the proper time, muting processes with signal-emitting muting sensors have been used across the industry in the past. These sensors were installed in addition to the safety light curtains and enabled pallets and transported goods to move in and out without interruption. In front of and behind the safety light curtain, however, quarters are usually a bit tight. The additional use of bridging sensors often required more space, leading to a less compact system design. The installation and service effort for the additional set-up, alignment and realignment of these sensors also resulted in additional work. “This led WITRON to search for a solution that combines process reliability, system availability and easier operation with one another,” Schmid explained.
At that time, Leuze electronic did not yet have a practical answer to this requirement, but did already have a project idea. The idea, known as ‘Smart Process Gating’ is based on its MLC safety light curtains. Leuze electronic presented this to WITRON in a very early development phase. WITRON was quickly convinced of this idea and assisted Leuze’s development in numerous practical tests. Smart Process Gating (SPG) was then put through its paces by WITRON on its test tracks in its company headquarters, where it was further optimised.
“The result is impressive: a clever solution was created that combines the requirements for safety at work with high process reliability and system availability,” explained Josef Apfelbeck, Key Account Manager and Specialist for Intralogistics at Leuze electronic. With SPG a new process was created that enables muting processes to be executed more easily, more compactly and more stably. With the SPG principle developed on the basis of Leuze’s MLC safety light curtains, it is possible to completely forego the previously necessary muting sensors. Conveyor systems can thus be made more compact. During the operating phase, the risk of misalignment or damage to the sensors is also eliminated as are the costs for their maintenance and servicing. The availability of the entire safety device is thereby increased and other practically oriented risks reduced.
With SPG, the first muting signal comes from the process control (PLC), while the second muting signal is generated by the protective field itself. SPG requires a controlled material flow so that the necessary PLC control signals are made available in the expected time window. The MLC 530 safety light curtain variant with SPG is TÜV certified for safety.
In combination with a standard control, a performance level PL d can be achieved, which is sufficient for many applications in intralogistics. With a safety control, performance level PL e is also achievable.
Originally published here.
Phone: 1300 538 933
Timmer quickLIFT and heavyLIFT vacuum hose lifters
Timmer has a range of vacuum hose lifters for safely lifting and lowering heavy goods.
Key Technology Iso-Flo, Impulse, Zephyr and Marathon vibratory conveyors
Key Technology introduces high-capacity vibratory conveyors for advanced food-handling applications.
Sidel RoboAccess_Pal S robotic and cobotic palletising solution
RoboAccess_Pal S, Sidel's latest robotic and cobotic palletising solution, will be in action...