Bulk bag weigh batch discharger improves granular sugar re-bagging
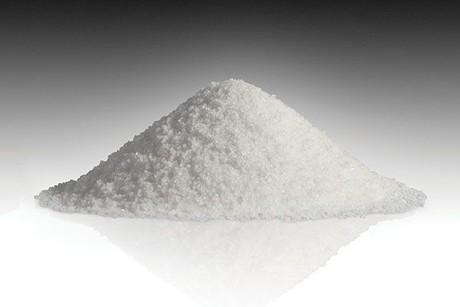
In the UK, Welcome Food Ingredients required a more efficient system to re-bag granular sugar used to manufacture its sauces, pastes, dressings and dips for food industry customers.
Food hygiene procedures require sugar and other granular ingredients to be decanted into food quality plastic bags weighing 10 kg, but previous methods proved complex and time consuming.
The company now accomplishes the task in one-third less time with less labour while meeting ATEX requirements using an automated bulk bag weigh batching system with integral flexible screw conveyor from Flexicon Europe.
Re-bagging was labour intensive
“With the old process, we received sugar on 1-tonne pallets, comprised of forty 25 kg bags,” said Tony Swann, Welcome Food Ingredients Safety, Health & Environment Manager. “We used a combination of vacu-lifters and manual handling in an eight-stage process to transfer the sugar into appropriately sized plastic bags before they could be loaded into the cookers. The new transfer system has reduced re-bagging to just three stages.”
Bulk bag discharger simplifies operation
One-tonne bulk bags are positioned alongside a Flexicon Bulk-Out BFC-S-X stainless steel bulk bag discharger, which has an integral cantilevered I-beam with an electric hoist and trolley. The bag straps attach to a cross-shaped lifting frame, and the hoist lifts the bag into position on the discharger frame. An ATEX-rated earth clamp is then attached to the bag.
The operator attaches the clean side of the bag spout to the clean side of the discharger by means of a Spout-Lock clamp ring, which is mounted atop a Tele-Tube telescoping tube that maintains constant downward tension on the bag as it empties and elongates, promoting material flow into the 110 L hopper.
Flexible screw conveyor transports sugar to weigh hopper
From the hopper a flexible screw conveyor that is 3.0 m long and 115 mm in diameter transports sugar to a 40 L capacity conical stainless steel weigh hopper resting on three load cells.
A gain-in-weight control system meters sugar into the weigh hopper at maximum feed rate. The load cells transmit weight gain information to the controller, which steps down the feed rate to a trickle and stops the conveyor immediately before reaching the target weight to compensate for material in flight.
Weighments of sugar are discharged dust-free through a slide gate and downspout into a 10 kg capacity blue plastic bag that is clamped beneath the weigh hopper. Once filled, the bag is manually tied off and placed in a plastic storage stillage. The weighing and filling cycle is repeated for subsequent bags.
Discharger, filler improve operating efficiency
“The bulk bag discharger and filling system has simplified and improved what was a complex, multistage handling process,” explained Swann. “Each week we typically re-bag around 30 tonnes of sugar, sometimes operating for 20 hours per day. With our old method, we were handling the equivalent of 100 tonnes of sugar per week.”
He said, “Our staff disliked having to manually handle 25 kg bags and are now more comfortable with packing 10 kg bags using the new equipment. It also offers benefits for the future as it can be extended if required. Additional items of equipment like sieves can be incorporated if our customers request their use.
“The fact that Flexicon could supply an ATEX-rated food quality handling system with all stainless steel components was of great importance to Welcome Food Ingredients. We’re pleased with the operating improvements it has allowed us to achieve.”
Phone: 07 3879 4180
Timmer quickLIFT and heavyLIFT vacuum hose lifters
Timmer has a range of vacuum hose lifters for safely lifting and lowering heavy goods.
Key Technology Iso-Flo, Impulse, Zephyr and Marathon vibratory conveyors
Key Technology introduces high-capacity vibratory conveyors for advanced food-handling applications.
Sidel RoboAccess_Pal S robotic and cobotic palletising solution
RoboAccess_Pal S, Sidel's latest robotic and cobotic palletising solution, will be in action...