Top 10 considerations when moving to heat pumps
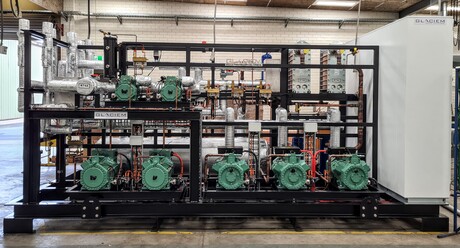
Transitioning from burning fossil fuels to electricity requires new technologies, and in particular heat pumps. Heat pumps can replace boilers of all kinds in buildings for heating but also in industrial processes. This is a challenge for many commercial and industrial heat users because heat pumps are “unfamiliar territory”. So what are the “Top 10” considerations when moving to heat pumps?
1. Get to a solution
“Analysis paralysis” afflicts the heat pump transition like many other business decisions. Heat pumps that have been common in the HVAC and refrigeration sectors are new and different for the industrial sector. Steam, hot water boilers, gas, diesel and coal burning are the norm.
Heat loads are characterised by demand (the heating rate), load (the amount of heat), and Delta-T — the difference between input and output temperatures. Heat sources need to be assessed — the ambient conditions across the year, the waste heat opportunities, and other sources (eg, water, etc). All of these have load profiles — the load over time. Without load profiles we only see peak requirements, and the peak demand is often quite transient.
By evaluating all your loads, you can work to a solution that optimises the input energy (recovered heat and eventually electrical power) required.
2. Take off the “boiler blinkers”
Our natural inclination is to think in terms of what we know — our current heat architecture. We think the problem is, “We need to replace the boiler with a heat pump”. In fact the problem, usually is, “Decarbonise by 2030!”. This requires a different perspective — a change of paradigm. Instead of “How do we replace the current equipment?”, begin with “What do I use heat for?”, and “What is my heat demand?”. Begin by understanding the application and from there work to a solution that aligns with the capabilities of heat pumps. Looking at heat pumps through “boiler blinkers” will only rarely bring you to a workable solution.
3. Modulate the load
Installed boiler capacity is often a multiple of the actual demand, and boilers are rarely operated at capacity.
It is not unusual to see heat capacity confused with the actual heat demand. Thermodynamics is usually straightforward. The expected heat demand of industrial processes is amenable to analysis and prediction, even without expensive monitoring equipment. This analysis can highlight how to improve efficiency and eliminate losses. In the past, capital investment decisions were based on, for instance, the marginal cost of using more heat from a boiler. We thought of hot water and steam from boilers as a “free” commodity. Even today with rising gas and fossil fuel prices this no longer holds, yet the thinking often remains.
Usually, we can modulate the load and thus reduce the actual demand required from a heat pump solution.
Begin with the analysis and modulate the load.
4. Use the free cooling
Many industrial processes requiring heat also need cooling and refrigeration. This is common in food and beverage where product is heated for cleaning or cooking, and then chilled or frozen for packaging, storage and distribution. Pharmaceuticals and other industrial applications similarly use both chilled water and heating in their industrial process.
Heat pumps use the refrigeration cycle to produce heat. They can be configured to support the refrigeration demands nearby. Today that demand is currently met by chillers supporting chilled water or glycol loops configured as “secondary refrigerants”. By using the “free cooling” from heat pumps the cooling demand can be offset. This reduces the need to run the chillers, hence reducing the energy cost and extending the chiller life. All of these improve the efficiency of the heat pump solution and improve the business case for heat pumps.
5. Go higher! (temperatures)
Glaciem CO2 heat pumps can produce hot water as high as 95°C at marginal additional cost. Further, they can produce sensible heating of air, many oils and other materials up to 120°C. They can be configured to serve all of these from one heat pump using a range of heat transfer technologies including heat exchangers and coils at the same time as cooling down to -50°C. Some heat pumps can only produce lower temperatures and being constrained by a technology choice like this limits system efficiency. Many industrial production processes have been designed around technologies that have a high cost for higher temperatures. The availability of heat pump technologies that produce higher temperatures at similar cost and higher efficiency leads to best practice that reconfigures the heat demand to accept the highest reasonable temperatures.
6. Go for scale!
In the past every heat or cooling demand had its own system. Each system was over-sized. Today, by incorporating all your available heating and cooling demands into one heat pump solution you can optimise for “diversity” (the reality that not all demands peak at the same time). One system with different operating modes provides all of your differing demand profiles.
The result is larger heat pumps with lower heating unit cost. Glaciem CO2 heat pumps are multi-megawatt systems that are deployed into a range of flexible configurations depending on plant room and space constraints.
7. Level the load with Stratified Thermal Storage
Stratified hot water storage tanks allow heat pumps to be sized for a consistent capacity that “levelises” the energy requirement from the heat pump whilst providing for the peak demand of the application. Further stratified hot water storage allows for return temperatures and off-takes to vary without affecting heat pump efficiency.
8. Maximise use of renewables with Thermal Energy Storage
Behind the meter renewables like solar PV naturally produce low or marginal cost electricity when the sun is shining. Using such power when it is available to run your heat pump means that you need to be able to utilise the heating and cooling even when it does not match your load profile. Thermal energy storage with phase change materials like that of Glaciem enables dense storage of cooling to offset cooling demand at a different time. Similarly, stratified hot water storage can be used to store heat for when it is required.
9. Kill the parasites
Heating and cooling architectures traditionally have been designed around processes that made assumptions about how heat was best delivered for technologies related to boilers. When analysed there are usually huge parasitic loads like pumping power and fan power that are not assessed when people are evaluating the cost of energy for heating demands.
Producing higher temperatures and higher Delta-T reduces the power required for pumping without affecting “off-coil” air temperatures thus reducing the fan power needed to heat air to the required temperature.
Avoiding secondary refrigerants where possible (eg, using the heat pump’s CO2 refrigerant directly as the heating or cooling fluid) can eliminate pumping power and dramatically reduce the fan power required.
10. Engage heat pump experience
Companies like Glaciem Cooling Technologies have a wealth of experience in designing and configuring heat pumps for commercial and industrial applications. There is also a growing network of energy and mechanical services consultants who understand heat pump capabilities and are experienced in their application. Reach out to them for help.
CO2 heat pumps are industrial refrigeration systems with the same general architecture, maintenance requirements and integration requirements as systems that have been deployed into many refrigeration applications in various industries. These contractors and skills are readily available to support the installation, commissioning, service, and maintenance of heat pumps in industrial settings.
Advanced Manufacturing for local industry
APS Industrial's state-of-the-art Manufacturing Centre in Adelaide forms a national benchmark...
The Importance of Blast Freezing for Food Products in Australia
The benefits of blast freezing extend beyond quality preservation.
Growing Demand for Chilled and Frozen Food Storage in Australia Drives Americold's Expansion
As the demand for cold and frozen food storage reaches new heights in Australia, Americold is...