Keep it cool, lower energy costs, with effective refrigeration motor and drive technology
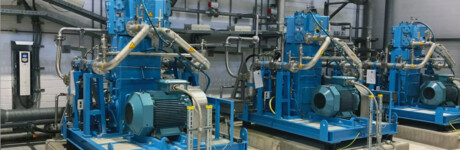
The global food and beverage sector consumes approximately 30% of the world’s energy. It is also responsible for 20% of all greenhouse gas emissions. As consumers and governments call on all industries to limit their emissions, the food and beverage sector must find ways to operate as efficiently as possible.
In many facilities, refrigeration and cooling consumes a significant amount of power — in some cases, up to 60% of the total energy budget. Much of this energy goes to powering motors, which drive cooling compressors, pumps, evaporators and condensers.
While the load varies, many motors used in refrigeration applications run at a constant speed. This wastes energy and results in unnecessary emissions. It also contributes to high operating costs, especially as the price of electricity continues to rise.
Fortunately, the latest generation of high-efficiency motor and drive technology enables facilities to significantly reduce energy use, among a range of other benefits.
Efficient motor technology
In many countries, energy efficiency classes are set out by the International Electrotechnical Commission (IEC). The least efficient motors are classified as IE1, while the most efficient models are IE5 class. With an increase in IE class, such as from IE2 to IE4, a motor achieves 20% lower energy losses.
Synchronous reluctance motors (SynRM) offer an even higher level of efficiency — IE5. Upgrading from an IE3 motor to an IE5 cuts energy losses by 40%. Continuing to use older, less efficient motors is a false economy — the power savings achieved by modern SynRM motors quickly pay for the cost of upgrading, often in just months. In other words, the financial and environmental case for upgrading only becomes stronger as energy prices rise.
As well as being significantly more energy efficient, there are several additional advantages to SynRM technology for refrigeration applications. Compared with other types of motors, SynRM motors achieve lower winding temperatures and bearing temperatures, reducing the amount of heat transferred into the refrigeration system. This reduces the risk of failure and extends the equipment’s lifespan. SynRM motors are also quieter than other types of motors.
Greater efficiency and control with variable speed
Additional energy savings are possible when motors are paired with variable speed drives (VSDs). Without a VSD, a motor runs at full speed regardless of the load. Operators then control the output by throttling flow downstream, such as by using valves. This is like keeping one foot on the accelerator pedal of a car and controlling its speed using the brakes.
With a drive, an operator can precisely adjust a motor’s speed to the exact requirements of the process. Any time it is not operating at full speed, it is saving power. Pairing a motor with a drive delivers energy savings of approximately 25%.
Since drives provide a high level of control over the motor’s speed, they also enable greater control over a refrigeration or cooling system’s performance. With VSDs, the system can adjust to variations in the external temperature caused by the weather, season, or other factors. This ensures that the products remain at exactly the specified temperature, improving quality and reducing waste.
ABB’s ACS580 drive includes features designed specifically for cooling and refrigeration applications in the food and beverage sector. The cooling compressor control feature enables easy setup, editing and continual control of a system’s temperature range.
Real results from Campbell’s Australia
Campbell’s Australia’s Shepparton plant in Victoria has been producing its much-loved range of soups, stocks and meals for Australian households for almost 60 years. They replaced a single refrigeration compressor motor with an ABB SynRM IE5 motor-drive package which has resulted in reduced energy costs by 14%, eliminated 131 tons of CO2 emissions and saved the operator over $10,000 USD per year.
Additionally, a major dairy product manufacturer with locations all over Australia has, with its own commitments to improving sustainability and reducing environmental impact, installed ABB’s high-efficiency motors in one of their production facilities. The high-efficiency motors were implemented to replace their traditional motors which were running the refrigeration compressor application for product cold storage.
They had noted that the compressor’s power consumption costs were exceeding that of the product production itself. Impressed by ABB’s packaged turnkey installation offering, they also implemented ultra-low harmonic VSDs to further increase energy saving potential.
Food and beverage businesses have a major opportunity to improve the performance of their cooling and refrigeration systems while also cutting energy costs and associated operating expenses — a clear win-win.
Rory Paltridge, Division Manager for Motors at ABB Australia, said, “The processes that consume the most electricity in the food industry relies on motors. Readily available technology enables opportunities to save energy, especially in processes that do not run full speed all the time. Companies now have a chance to accelerate their transition to sustainable food production by replacing legacy motors with SynRM and drives. It’s a simple way to upgrade, modernize and reduce wastage.”
Submit an inquiry to ABB Australia
For more information please visit:
Flexible Biogas Solutions For The Food Sector
Anaerobic Digestion can be used to treat organic waste and produce renewable energy that can be...
Flexible Biogas Solutions For The Food Sector
Anaerobic Digestion technology can treat organic waste on-site to produce renewable energy that...
Plug and Play Solutions for a Greener Future
Are you encountering large trade waste and energy costs? Are you watching dollars literally go...