Moving into a smarter world with pneumatics
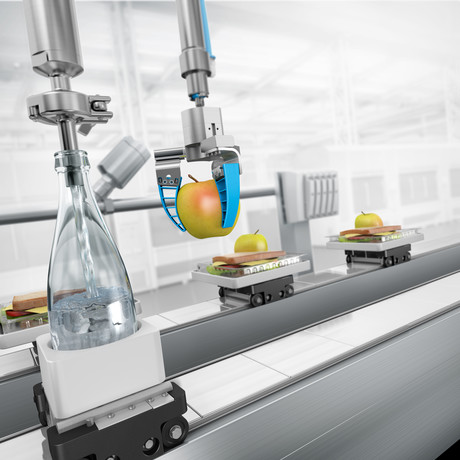
Industry 4.0, the Industrial Internet of Things (IIoT) and digitalisation is the biggest story in manufacturing today and is affecting both OEMs and end users in the food production sector. The goal is that production and the digital world will come together to make automation more flexible, increase energy efficiency, optimise logistics processes and add flexibility to the value chain.
In addition to meeting regulatory requirements, food manufacturers and processors must be able to respond quickly to retailer brand requirements for conformity and customer expectations regarding safety. And if something does go wrong, accurate data about batch numbers and distribution patterns is critical, to enable a swift and thorough recall of any substandard product.
Industry 4.0 and the concept of the smart factory has much to offer the food sector. The adoption of more connected production, packaging and labelling technologies offers the potential to improve production efficiencies, reduce costs and be more receptive to customer demands. So why does the industry seem reluctant to implement the changes that will deliver these long-term benefits? At one end of the supply chain food manufacturers are waiting for machine builders to offer ‘features’ that will deliver the Industry 4.0 workplace, while machine builders are waiting to be told what features the food processors are actually looking for before investing in their development. The good news is that it does not require investment to build a new facility or replace obsolete equipment to embrace Industry 4.0 principles: it is possible to implement positive change in a modest way and scale up gradually.
Indeed, benefits can be derived by updating existing equipment through the retrofitting of additional sensors and data logging facilities. Simple examples include checkweighers equipped to communicate with filling machines in order to adjust variations in fill levels without stopping production, or an intelligent valve that monitors the air consumption of a machine to better predict and schedule servicing.
Benefits through technological advancement
While maintaining affordability, Festo by no means falls short of providing advanced solutions to customers who convey a desire for cutting-edge technology. Festo continues to invest time and resources in R&D to stay ahead of the market and provide its customers with tailored solutions to meet their demands. Advancements through intelligent pneumatic components and systems are available today that can deliver both factory automation and process automation in food applications. For example, the pneumatic pinch valve VZQA provides hygienic and reliable dispensing of food and offers a N/O variant with a silicone diaphragm that is FDA certified involving direct contact with food products. There is an increasing demand for modular components which can be converted quickly and easily depending on the requirements. For example, the sturdy and powerful angle seat valve VZXA for the fast and reliable control of media flows. Its carefully thought-out product architecture and patented interface enable valve bodies and actuators to be freely combined. This provides even greater flexibility for any application.
New technologies and proven components lead to pioneering products like the 2-channel safety valve MS6-SV, which permits a very smooth pressure build-up and fast, safe venting to Performance Level e. In addition, the energy efficiency module MSE6-E2M prevents undesirable compressed air consumption by interrupting the compressed air supply when the system is at a standstill. It allows important operating parameters such as flow and pressure to be monitored, thus sustainably increasing the process reliability of production. Significant energy savings can be made: refer to the case study from Ben & Jerry’s here. These modern air preparation components clearly show that security and efficiency, combined with competency and simplicity, are now the minimum requirements for air preparation.
Festo’s automation solutions allow users and designers to create decentralised installation concepts without a control cabinet in harsh and intensively cleaned environments in the food and beverage industry close to the application for lower energy losses and high cycle rates: either as a solution without a control cabinet, with the Clean Design valve terminal MPA-C offering the ideal degree of protection IP69K, or with the valve terminal VTUG in a control cabinet with a multi-pin plug, for all standard fieldbus systems or IO-Link.
Meanwhile, the CPX terminal can act as an automation platform, valve terminal partner or remote I/O. It can be used to integrate pneumatic and electrical control chains easily, quickly and seamlessly, as well as providing the open communications and flexibility to meet company-specific standards.
However, Festo’s most recent development will in the future aid the transition to the smart factory. The VTEM Motion Terminal is a pneumatic automation platform that can be controlled by apps. This means that, for the first time, the functions of a pilot valve can be changed via software — using the same hardware. The VTEM therefore offers the flexibility to respond rapidly to changing customer demands. Because new functions can be added quickly via apps, machine developers can create a basic machine type and then select the relevant apps to equip it with different functions and features in accordance with customer requirements. The apps replace over 50 individual components. Paired with the CPX automation platform, the solution offers modular remote I/O, comprehensive fieldbus options, optionally embedded CoDeSys controller and IoT gateway, a controller for electric drives with stepper motor and servo controllers and, last but not least, Industry 4.0 pneumatics.
So technology has advanced to the point that the smart factory is not something we need to wait for. The technology is already available to make step changes in automation and, because it can be adopted incrementally, it is also affordable. Festo is already offering technology with smart functionality to respond to the major issues that Industry 4.0 presents, such as process reliability and safety engineering. With its hygienic products and solutions, from valve terminals featuring a hygienic design right through to electric or pneumatic drives, Festo helps its customers in the food industry meet high standards of quality.
Pacific Automation: Automation Components and Solutions for Australia's Food Processing Industry
Pacific Automation is positioned as a trusted partner for delivering high-performance, innovative...
Managing Food Safety Risk Efficiently with Data Automation
Data is only valuable if it is actionable.
Introducing Tool-Free Mounting and Reduced Service Times with Bürkert's Direct Acting Service Valves
In the bustling world of beverage manufacturing, efficiency and reliability are paramount.