Modern odour control for the food factory
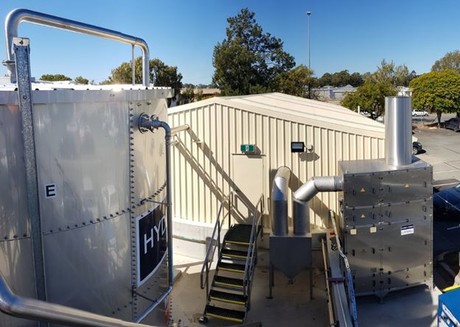
Traditional odour control systems involve a biological or chemical process whereby odorous compounds are broken down by a form of oxidation. For biofilters and bioscrubbers, this is accomplished by organisms that obtain their energy from exothermic oxidation reactions, whilst reagents such as sodium hypochlorite are responsible for the oxidation in chemical scrubbers.
An exciting alternative odour control technology that uses UV light and a catalyst as the means of oxidation is called Photoionisation. Photoionisation is relatively new to Australia and New Zealand but has been well proven in Europe and elsewhere for many years with many hundreds of installations worldwide.
Photoionisation is ideal for treating odours generated from wastewater and sludge process operations. With its high performance and small footprint, it is proving to be popular in a wide range of industrial and municipal applications.
Photoionisation is based on the application of UV light and a catalyst. The first part of the process mimics natural reactions that occur in the upper atmosphere by the interaction of air and UV light from the sun. In the Neutralox photoionisation system, odorous air passes through a chamber where it is exposed to intense UV light creating free radicals, (O2-, OH-, O3, etc.), which immediately begin oxidising the odour causing compounds.
The air then passes to a catalyst, where any remaining odorous compounds are adsorbed and broken down by the constant flow of free radicals present in the air from the UV section.
Photoionisation has been proven to be at least equal to and often a more effective odour control technology in many applications and, as the footprint is very small, it is ideally suited to industrial sites where space can be an issue. The unit starts to function immediately after it is switched on and it can effectively treat very high levels of odorous compounds, especially reduced sulphur compounds, ammonia and methyl mercaptan. Unlike other odour control systems, it is not affected by variations in air quality or temperature and humidity.
The system requires a very small amount of energy to operate and does not use any chemicals. The two-step process recharges itself and requires no more than a day of service per year. UV lamps require replacing every 10,000 hours and changing the catalyst is usually less frequent.
Hydroflux are the exclusive agents for the Neutralox photoionisation process in Australia, New Zealand and the Pacific Islands and have odour specialists who are available to discuss your odour issues.
Heat and Control expands thermal range with Tek-Dry acquisition
Earlier this year, Heat and Control announced the acquisition of UK-based company Tek-Dry Systems...
OD200: New Compact Distance Sensor Raising the Bar in Performance and Reliability
Launching in June 2025 from SICK’s HQ in Waldkirch, the new OD200 miniature distance sensor...
Key benefits of METTLER TOLEDO's product inspection solutions
In the fast-paced Food and Beverage industry, ensuring the safety and quality of products is more...