Increase your productivity: refurbish your equipment
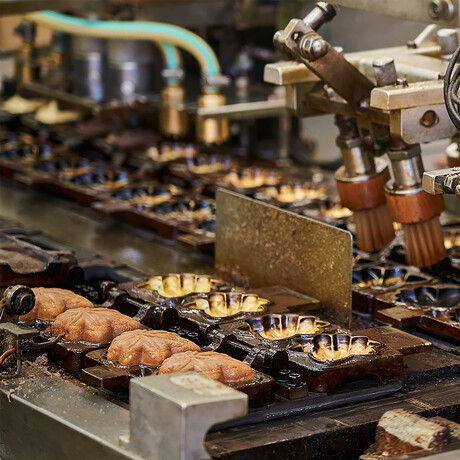
Keeping production lines going and machinery operational can be crucial for food manufacturers. Many food processing and manufacturing companies hinge on getting large orders out efficiently and without any major defects to their batches. Making sure your orders are processed on time and to customer specification can be difficult if parts of your equipment are starting to show their age.
Whether it is the non-stick coating on your food-contact equipment wearing away, or the vital components of your machine deteriorating and slowing down production, at some point you will need to consider restoring your equipment to its former glory.
Replacing your machine parts or equipment is often the first option that comes to mind — however, this can come with its own challenges, including long lead times and extended machine downtime.
Instead of undergoing the hassle of replacement, why not refurbish your existing equipment? Whether you need new baking trays, conveyor belts or metal machine components, recoating your existing parts can be a great way of increasing your productivity. Here are five reasons why you should consider refurbishment over replacement.
More efficient maintenance programs
Equipment maintenance can be a lengthy and costly business, particularly if you require replacement parts.
If you create a uniquely-shaped product that requires its own tray, or have an IP-protected part or mould, you will need to factor in design and fabrication costs when sourcing custom-made replacements. Machines often also have device-specific parts, which often need to be ordered from overseas. Wait times for overseas orders can take several weeks or even months — and that is before you factor in delayed shipping and delivery times due to COVID-19.
In the meantime, you will either need to use a backup set of equipment (if you have one) or your machine will have to undergo downtime, which could affect your ability to complete orders and cause delays to your lead times.
Refurbishment can take significantly less time, especially if you find a local supplier; it is far easier to restore unusual shapes or unique design devices with a fresh coating, rather than wait for new parts to be fabricated. A local finisher can turn your product around in a short period, helping you get back up and running sooner.
For a smooth maintenance operation, it is recommended you keep two sets of equipment and establish a program with a local supplier wherein you send one set for refurbishment at a time then swap them over. This ensures you will always have good-condition equipment at your disposal and you can run continuous operations if needed.
Higher quality products
When it comes to your food processing equipment, recoating your parts can make all the difference — not only to your machines, but to the products you manufacture.
If the original coating on your baking trays, moulds or conveyor belts has aged or worn away, you may be left with residue and food substances on the surface. If your products are sticking to the surface of your equipment, they are more likely to be damaged when you attempt to remove them from the machine and may not always come away in one piece. A fresh Teflon® or non-stick coating can allow your products to smoothly pop out of your trays intact, allowing you to provide better quality wares for your customers.
The same can be said for moving machine parts that have degraded over time — if your machine is not at optimum functioning levels, this can affect the quality of your end product. A hardwearing coating such as hard anodising can restore these parts, ensuring your machines are running smoothly and performing as they should be.
Long term cost saving
Refreshing parts with a new protective coating will not only save you time on ordering new equipment — it will also add extra durability and a longer lifespan to your parts. Quality coatings mean your equipment will last longer before it needs refurbishing again, and even longer before it eventually needs replacing, saving you significantly on maintenance costs.
Reduced wastage
Constantly sourcing new metal components can be a drain on the earth’s resources — and if you are throwing away perfectly good parts whose only flaw is a degraded coating, you are wasting potentially valuable material. If your parts have not worn through, but merely require a removal of surface contaminants or the replacement of an old coating, simply refinishing them can restore them to life and allow them to be used again, drastically reducing wastage.
Find a trustworthy local supplier
You get what you pay for when you choose a reputable Australian supplier. Using quality local suppliers not only reduces wait times — it ensures you are choosing a quality service every time. Reputable Australian coatings providers are more likely to test to and comply with the required standards, something not guaranteed if you purchase items through an overseas supplier. In addition, the fact that they are not far away gives you the opportunity to meet with your supplier in person and discuss your specific needs.
DECO Australia is a reliable, Australian-owned family business offering a range of recoating services ideal for food manufacturers. Their durable finishes offer maximum protection and performance for machine components that need to withstand hardwearing applications, harsh conditions of build-ups of sticky substances. DECO offers two different types of Teflon non-stick coatings as well as the unique, extra durable DecoUltra™ ZD hard anodised finish, as well as other finishes ideal for food processing applications.
DECO’s in-house testing systems and ISO 9001 accredited Quality Management System ensure all its finishing processes are of consistently high standard and compliant with Australian and international standards.
Visit DECO Australia’s website to find out more about the range of food-safe coatings we can offer to enhance your productivity.
Smart AI solutions shaping Australia's food future
With Australia approaching a federal election in the coming months, the government is stepping up...
Detection and Quantification of Lactose in Dairy Products
The Neogen Megazyme K-LOLAC test kit is a widely used enzymatic assay for the quantitative...
Complete processing lines for savoury snacks: challenges and opportunities
The global savoury snack market faces several challenges and opportunities.