Delta intelligent facility process cooling water control solution for beverage factory
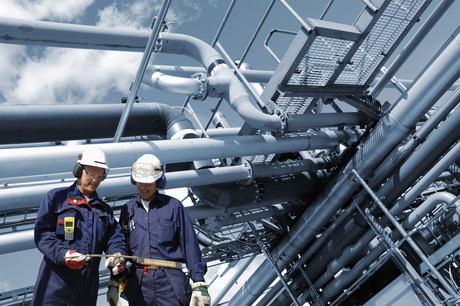
Introduction
-
Function
Before improvement, the water supply pressure and flow of the boiler and filtered water for the beverage production line and factory area were controlled via a water tower with a height of 20 m, utilising high/low water level of the water tower to start/stop the lift pump in order to keep the water pressure stable.
After improvement, with intelligent variable-frequency control, the system provides more accurate constant pressure control solution with less footprint.
-
Application
The constant pressure water supply solution for process cooling water can be widely used in the food processing and chemical fibre industry.
Process
-
Description
With the same fluid, pipe size and switch state, the flow rate remains unchanged under the same outlet water pressure.
Therefore, after switching from water tower to direct water supply, it delivers the same flow rate in the field pipeline as long as the water supply pressure remains the same.
This solution features the mid-range PLC AH500 to control three sets of variable-frequency water supply systems, and sets the manual/automatic mode and parallel standalone mode over the central monitoring system (DIAView).
-
Control instructions
Automatic mode: Execute the constant pressure control program in automatic mode. Select the parallel mode to automatically increase/decrease the number of water pumps, and feed back 4~20 mA pressure signal to the PLC via the outlet pressure sensor for cooling water. The PID performs calculation and sends the output frequency signal to the motor drive as the constant pressure output. Increase the number of paralleled variable-frequency water pumps via loading conditions if the pressure is insufficient even under full load.
Manual mode: The operator sets the operation frequency on the HMI directly without performing constant pressure control.
Constant pressure water supply system | Water supply by water tower | Traditional direct water supply | Variable-frequency direct water supply |
---|---|---|---|
Pump start/stop basis | Water level of water tower | Outlet water pressure | Outlet water pressure |
Sensing element | Liquid level sensor | Mechanical pressure sensor | Electronics pressure sensor |
Precision | Good | Medium | Excellent |
Pump operation mode | 0/100% | 0/100% | 0/50~100% |
Pressure change | Good | Medium | Excellent |
Delta total solution
Equipment list
Name | Function | Model | Quantity |
---|---|---|---|
Industrial HMI software | Process, boiler and filter water supply monitoring | DIAV-xxxxx0000B | 1 |
High-performance mid-range PLC | Constant pressure control and parallel control for process cooling water | AHCPU500-EN (32DI,32DO,8AI,8AO) | 1 |
Vector control drive | Pump motor control for process cooling water, boiler water and filtered water | C2000 | 7 |
Multifunction integrated meter | Electric metering for process cooling water pump | DPM-C530A | 1 |
Features and advantages
Further upgrade of device architecture
- Intelligent, precise and instant control architecture for higher process water supply stability and less equipment footprint.
- Integrated communication among the drive, controller and HMI software for visualised operation.
Flexible extension
- The PLC supports different communication protocols including Modbus TCP, EtherNet/IP, Modbus RS485, etc., for quick extension and integration with peripheral devices in the future.
- The HMI supports OPC communication protocol (OPC Server/OPC Client), allowing future data integration and data analysis with energy management systems.
Complete and professional solution from Delta
- Comprehensive consideration for both the system and control, offering different operation modes.
- Modular programming is used for system set-up. Users can program function blocks for different processes or actions separately, for easy read/write and maintenance.
- Delta IA solution is highly integrated, offering high precision, stability, synchronisation and flexibility.
Heat and Control expands thermal range with Tek-Dry acquisition
Earlier this year, Heat and Control announced the acquisition of UK-based company Tek-Dry Systems...
OD200: New Compact Distance Sensor Raising the Bar in Performance and Reliability
Launching in June 2025 from SICK’s HQ in Waldkirch, the new OD200 miniature distance sensor...
Key benefits of METTLER TOLEDO's product inspection solutions
In the fast-paced Food and Beverage industry, ensuring the safety and quality of products is more...