Application report: best quality beer, non-stop
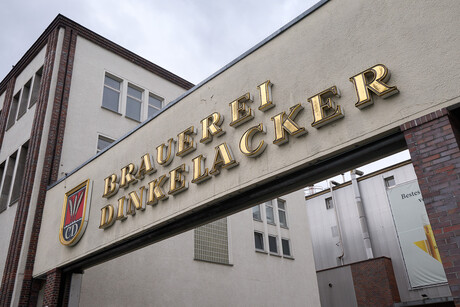
Best quality, non-stop
Beer lovers in South West Germany are familiar with these traditional brands: Dinkelacker, Wulle Biere, Schwaben Bräu, Sanwald, Cluss or Haigerlocher. They are all regional beer specialties, and are brewed by Dinkelacker. The family brewery has been in existence since 1888. It was founded by Carl Dinkelacker in the Tübinger Strasse in the heart of Stuttgart and it is still headquartered there today. Dinkelacker has long made use of application know-how and sensor technology from Leuze.
Indispensable sensor technology
Dinkelacker uses technology from Leuze at almost every station along its beer bottling line.
“The sensors must withstand severe vibrations and frequent cleaning processes,” said Florian Fahr, Head of Technology at Dinkelacker.
Only selected sensor solutions can rise to the challenge.
“Primarily, retro-reflective photoelectric sensors of the Leuze PRK series were installed here. These are particularly well suited for applications in the beverage industry. The metal housing of the optical sensors is resistant,” said Andreas Eberle, Local Industry Manager Packaging at Leuze.
Furthermore, the devices detect even highly transparent objects such as bottles and glossy plastic crates.
Material flow without jamming or collisions
The Leuze sensors are installed at various points along the filling installation.
“The PRK optical sensors on the individual conveyor sections detect pallets, barrels, beer crates or even bottles,” said Frank Karle, Head of Electrical Workshop at Dinkelacker. “Thus the speed of the conveyor belts is automatically regulated to prevent jamming and collisions.”
In the barrel filling section, Dinkelacker has installed about 100 sensors on the conveyor belts. Two new robots support the employees: they lift the empty or full barrels and place them on the conveyor belt or on pallets. Leuze multiple light beam safety devices of type MLD secure the work area against access from outside. Two PRK sensors which are arranged crosswise in front of each of the robots detect an incoming pallet. They then start the muting function, which bridges the safety light barriers so that the pallet can pass through.
Freshly filled
On the filling installation, the reusable bottle system fills the clean beer bottles — up to 66,000 units per hour. The swing-top bottle installation works on a separate production line. PRK sensors detect whether every filled reusable bottle has been correctly fitted with a crown cap or whether swing-top bottles have been closed correctly.
Every crate in view
After labelling, a machine fills several crates simultaneously with 20 beer bottles. Here, sensors detect in a fraction of a second whether a crate is completely full. If a bottle is missing or in a horizontal position, the crate is rejected and the error is corrected manually by an employee. When crates are filled with swing-top bottles, they are aligned so that their labels face outwards. Leuze sensors detect the labels on the bottles and assist the machine in positioning.
Efficient production
Dinkelacker has successfully modernised its production facilities. The Sensor People from Leuze make an important contribution to efficient production with their reliable and robust sensors.
Heat and Control expands thermal range with Tek-Dry acquisition
Earlier this year, Heat and Control announced the acquisition of UK-based company Tek-Dry Systems...
OD200: New Compact Distance Sensor Raising the Bar in Performance and Reliability
Launching in June 2025 from SICK’s HQ in Waldkirch, the new OD200 miniature distance sensor...
Key benefits of METTLER TOLEDO's product inspection solutions
In the fast-paced Food and Beverage industry, ensuring the safety and quality of products is more...