Water injection automation in coffee production
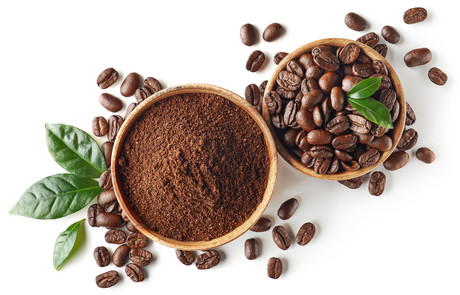
Controlling and measuring exact amounts of condiments, spices and ingredients directly determines important quality factors in the food industry, such as consistency, flavour and processing times. During its manufacturing process, coffee should be roasted in specific temperature ranges, with its taste and quality connected to its moisture content.
Group Instrumentation was asked by a coffee producer to supply a measurement system that could monitor moisture levels in coffee after the final roaster. During this process, to ensure the optimum taste it is essential to keep good moisture characteristics for conveying until the packing process. The coffee producer required a moisture range between 3.5–5% and functionality to control water injection into the roaster.
The solution
The M-Sens 2 continuously measures up to 65% of moisture content in materials conveyed on different devices, such as screw feeders, conveyor belts, slides and more. The M-Sens 2 monitors the moisture levels of coffee grains by controlling injection into the roaster. Measuring the moisture makes it possible to determine when and how much water should be injected into the final coffee roaster. After the automatic control, the manufacturing process becomes more reliable due to online measurement that updates a new set point for the water injection lines when a change in moisture content is detected. By automating and monitoring the water injection in coffee production, coffee producers can determine a fixed moisture range for their products, between 3.5–5%.
The M-Sens 2 provides online control of the water injection and allows users to avoid missing moisture changes in their product by measuring moisture levels through the coffee beans.
Phone: 07 3255 5158
NORD Drivesystems NXD tupH surface treatment
The NXD tupH surface treatment has been developed by NORD to make aluminium as resistant as...
igus D1 motor control with certified PROFINET
The igus D1 motor control can now be integrated into higher-level control systems from Siemens,...
Protect-Air HoseGuard Air Safety Fuses
Protect-Air's HoseGuard is designed to enhance workplace safety by automatically responding...