Streamlined canning line concept: Carlsberg projects in China
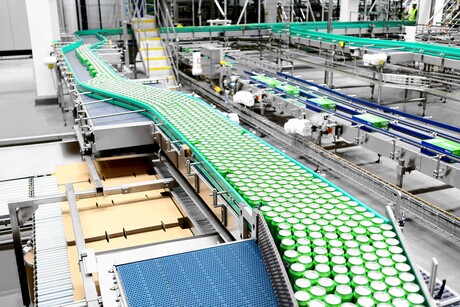
Two KHS Group canning line projects designed to focus on a streamlined layout and production design will act as a role model for all of Carlsberg’s Chinese factories.
Carlsberg was one of the first international breweries to start exporting beer to China about 150 years ago. For several decades now the company has been represented by a number of sites on the Chinese market, with numerous traditional operations spread across the country procured at various stages to augment its network. The enterprise, one of the leading beer companies in China, aims to improve the quality of local beers in the long term and grow together with its partners, suppliers and employees. This is to be brought about by modernisation of existing plant equipment and the introduction of new, advanced technologies.
KHS recently installed two canning lines at Carlsberg Dali Brewery (Dali City, Yunnan Province) and at Carlsberg Yibin Brewery (Yibin City, Sichuan Province). Despite the restrictions imposed by the pandemic, the new canning lines were commissioned before the agreed date.
In this large-scale project Carlsberg found it important that its new canning lines have a clear and streamlined layout. This was also to be as identical as possible at the two Chinese sites. “We succeeded in quickly implementing an intelligent, space-saving line concept in close cooperation with the customer’s project team,” said Norman Gras, global key account manager at KHS.
The heavily reduced number of buffer and conveying segments in the new line design make higher demands of the system control and machine availability — the shorter distances between the individual stations on the line tolerate no faults in the production processes. However, the high degree of reliability and ease of operation and maintenance of KHS’s technology proved convincing.
“The reject rate is under 1% and the level of efficiency is over 95% — and is even 100% in Yibin. These are fantastic figures,” said Paul Kime, asset and projects director at Carlsberg Asia. The filler is also compelling with its high capacity.
The heart of the line is the Innofill Can DVD can filler that processes up to 90,000 0.33 L cans or a maximum of 60,000 0.5 L cans per hour, ranging from local brands to Carlberg’s products.
The concept also incorporates an Innopas SX tunnel pasteuriser and a packaging system comprising an Innopack SP shrink packer at each respective plant plus two wraparound packers in Yibin and one in Dali, where several years ago KHS installed three returnable glass lines.
With its state-of-the-art robot grouping, palletising with the Innopal PB1 RG2 gives Carlsberg the flexibility it needs to also cope with possible future tasks. The total package is rounded off by a wide range of safety equipment such as a key-in-pocket door safety system and extended protective housing.
Another feature of the current project was the request for a lubrication-free container conveying concept and a dry production environment. “Normally we work with belt lubrication to minimise wear and keep the coefficient of friction constant,” Gras explained. “At both plants the beverage cans run dry on the belts.”
In opting for this solution KHS has disproved an ancient dogma — in the past brewers were absolutely convinced that the floor had to be wet — and helps Carlsberg in its striving for greater sustainability by saving water.
“The entire project was ideally executed and is an important role model for future canning line set-ups,” Gras said.
Phone: 03 9335 1211
NORD Drivesystems NXD tupH surface treatment
The NXD tupH surface treatment has been developed by NORD to make aluminium as resistant as...
igus D1 motor control with certified PROFINET
The igus D1 motor control can now be integrated into higher-level control systems from Siemens,...
Protect-Air HoseGuard Air Safety Fuses
Protect-Air's HoseGuard is designed to enhance workplace safety by automatically responding...