Sort it out: blueberry processor uses sorter to remove FM
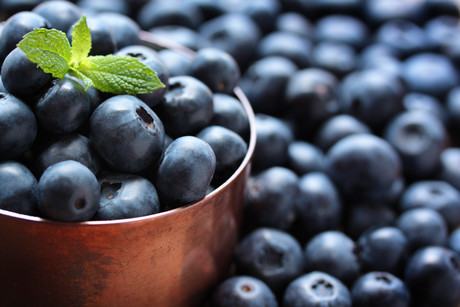
Quebec Wild Blueberries invested in a VERYX digital sorter from Key Technology in 2016 in order to aid the production process of its individually quick frozen berries. The new sorter, which replaced their existing laser sorter, removes more defects and foreign material (FM) from the berries and improves production efficiencies.
Pascal Hudon, director of operations at Quebec Wild Blueberries, praised the new technology for its increased accuracy.
“We improved our product quality and reduced false rejects. We also doubled our throughput with the same number of workers, which decreased our production costs,” he said. “Compared to our previous sorter, VERYX has increased our defect removal rate by about 3000%. It’s simply incredible.”
Tailored to suit their individual needs, Quebec Wild Blueberries chose the high-volume chute-fed VERYX C140, which was programmed to sort blueberries coming out of the freezer and remove twigs, bits of wood, stones, moss and other FM as well as any foreign berries. This particular model can sort up to nine metric tonnes of frozen berries per hour and features a 1400 mm-wide inspection area.
It is equipped with front- and rear-mounted laser sensors, which prevents any blind spots during inspection. The lasers work alongside colour cameras and the multisensor Pixel Fusion to detect the colour, shape and size of the product as well as its structural properties in order to determine whether there is any FM.
VERYX’s next-generation cameras and laser sensors offer twice the resolution of previous sorters, which increases accuracy and enables the detection of smaller FM and product defects.
“In addition to the power of Pixel Fusion, one of the first things that attracted us to VERYX was the precision of the ejection system. Other sorters space their air valves 10 mm apart, but Key designs VERYX with variable valve spacing that’s tailored to the application. For blueberries, Key recommended valves every 5 mm. With double the air nozzles, this sorter is more accurate in removing defects and FM and not ejecting good product with it. We’ve improved our defect removal rate at the same time we’ve virtually eliminated false rejects,” explained Hudon.
With detection and removal accuracy forming the most crucial aspects of their processing, Quebec Wild Blueberries also used Key’s Iso-Flo infeed shaker to separate and singulate product prior to VERYX. The Chycane chute features a concave shape that stabilises the product as it enters the inspection and ejection zones.
Hudson suggested Quebec Wild Blueberries rely on the data provided by the sorter, which is connected remotely to Key and the company’s plant-wide network, in order to produce reports and understand and control its production.
Using the VERYX sorter, one of the largest blueberry processors in the world is able to deliver high-quality blueberries with reduced risk of FM. Hudon explained that the sorter is easier to use than other sorters, allowing workers of various levels to easily understand and use the technology.
“Our clients’ quality requirements evolve as their customers get more and more demanding. We stay ahead by leveraging the most advanced technology,” noted Hudon. “Thanks to VERYX, we’re packaging the highest quality blueberries on the market.”
Phone: 03 8710 8200
Key Technology conveyor systems for poultry processing and packaging
Key Technology is introducing vibratory conveying systems for poultry processing and packaging...
tna intelli-assist XR solution for food manufacturers
TNA Solutions has launched the tna intelli-assist, an immersive Industry 5.0 extended reality...
Alfa Laval ThinkTop V55 sensing and control unit for diaphragm valves
The Alfa Laval ThinkTop V55 hygienic diaphragm valve sensing and control unit is suitable for the...