Screening tech at food processing plant regularly serviced
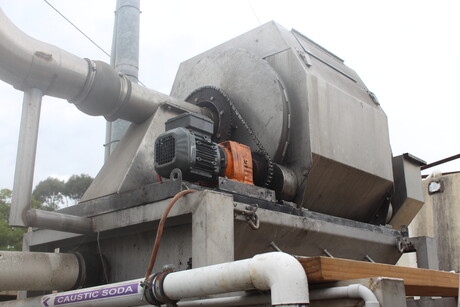
Australian food processor Beak & Johnston specialises in fresh-cut and value-added meat products, fresh soups, sauces and prepared meals. The family-owned business is extending the already decade-long service life of its CST Rotary Drum Screen by regularly conducting service and maintenance to optimise its performance.
CST fine screening technology is designed to avoid downtime, environmental spillage and OHS risks in food processing operations by acting to prevent clogging and breakdowns resulting from waste solids clogging downstream processes.
“Effective fine screening is an essential first line of defence to maintain the functionality and service life of vital food and beverage processing systems,” said Michael Bambridge, Managing Director, CST Wastewater Solutions.
Beak & Johnston’s RF6 model Rotary Drum Screen was first installed by CST Wastewater Solutions in 2010 and is still operating productively at the company’s Greenacre NSW site, where it removes meat and vegetable solids from wastewater.
“The wastewater screen has 0.5 mm wedgewire to separate the solids from the wastewater and was sized for four litres per second of pumped flow from the wastewater pit,” Bambridge explained.
In addition to supplying Australian manufactured screens, CST has an in-house Services Division, which helps companies to extend equipment life, avoid failures, and keep equipment and processes operating in optimum condition. The company can also conduct audits of wastewater treatment plants and processes in food and beverage, agriculture and other industrial applications. The audits are designed to determine where cost and production efficiencies can be gained or where environmental performance can be improved.
“This particular screen is mounted on a platform so that the screened flow can be gravity fed into Beak & Johnston’s downstream dissolved air flotation (DAF) unit,” Bambridge said.
“The robust construction and self-cleaning nature of the screen ensured minimal maintenance requirements for the first seven years, and then Beak & Johnston requested CST provide routine service and maintenance from 2017.”
The screen also has hot water showers, both inside and outside, to prevent fat build-up and blinding of the 0.5 mm aperture of the wedgewire.
The most recent service involved totally detaching the motor, chain and some guard covers to work on internal parts and optimise alignment to ensure continued performance.
“After each service, we provide Beak & Johnston with a full written report, check lists, Safe Work Method Statements, Job Safety and Environmental Analyses, site permits, and recently we’ve had to follow strict COVID site procedures for checking in and out of the site,” Bambridge said.
The latest CST Rotary Drum Screen design features all-stainless construction including base frame and is fully enclosed for OH&S odour and aerosol control.
Phone: 02 9417 3611
NORD Drivesystems NXD tupH surface treatment
The NXD tupH surface treatment has been developed by NORD to make aluminium as resistant as...
igus D1 motor control with certified PROFINET
The igus D1 motor control can now be integrated into higher-level control systems from Siemens,...
Protect-Air HoseGuard Air Safety Fuses
Protect-Air's HoseGuard is designed to enhance workplace safety by automatically responding...