Malt house retrofits 100 new drives
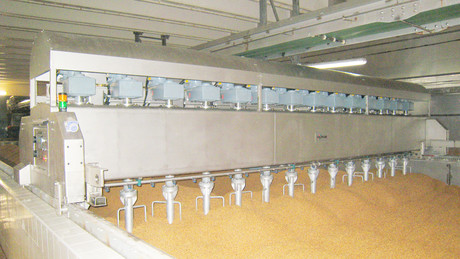
In the selection and configuration of drives for the food and beverage industry, food safety is the most obvious major concern. Various other issues must also be addressed with common challenges including adverse environmental conditions that must be kept under control from the outset. NORD Drivesystems has configured clean and resilient systems based on efficient smooth-surface motors for a Czech malt house.
Traditionally, beer brewers used to prepare their own malt. Now, specialised malt houses often handle this job for them. The processes in these facilities are largely automated and carried out with state-of-the-art equipment. One large, modern malt house can be found in Nymburk, near Prague.
In the first phase of processing, grain is steeped in water until it is ready to germinate. Next, the grain is placed in a so-called Saladin box, where it sprouts leaves and roots. Enzymes are formed and enriched. They convert the starch into malt sugar. All the while, the grain is regularly raked and aired. After about five days, the green malt is transferred to a drying kiln.
Retrofit with over 100 new drives
Before the advent of automation, turning the barley and clearing the malting floor were strenuous physical tasks that took many hours to complete. Modern malt houses have long ago switched to large mechanical turners, which enable production volumes of tens of thousands of tons per year. When the Nymburk malt house required a full-scale retrofit of these machines, they turned to Moravské potravinářské strojírny (MOPOS), a Czech OEM for the food industry with a particular focus on malt house and bakery machinery.
Eight turners, each over 7 m wide and weighing over 7.5 tons, were refurbished. A total of 120 drives had to be replaced with new, state-of-the-art systems. Each turner includes a main drive which moves the machine on rails that span the length of the Saladin box — over 53 m. These boxes are about 2 m deep. In addition, there are 14 individually driven vertical screws per turner. These rake the germinating grain once or twice per day as needed to keep it cool and aerated. Finally, a scraper mounted on the machine serves to discharge the green malt.
In this project, as the single source of drive solutions, NORD supplied 112 geared motors for the screw agitators as well as eight main drives with drive electronics for speed control. The drive manufacturer’s Czech subsidiary, NORD-Poháněcí technika, s. r. o., worked closely with its long-time customer MOPOS to configure these systems to suit the application.
The ambient conditions in the malt house are tough. The atmosphere is saturated with 100% humidity. Moreover, water vapour reacting with carbon dioxide also leads to the permanent presence of weak carbonic acid (H2CO3). Given these very tough operating conditions, MOPOS selected smooth-surface motors. In contrast to conventional motor types, the casings of these motors have no cooling fins, which eliminates typical dirt traps and surfaces prone to attract condensation moisture. The standard versions of these systems already provide IP66 ingress protection. Their terminal boxes are filled with solid resin. Both the rotors and stators are treated with a special, moisture-resistant lacquer.
Efficient thermal management
The smooth cases of the motors provide extra resistance against harmful influences as noted above.
However, this design requires careful thermal management, especially since the drives in the MOPOS machine run in continuous operation. The smooth-surface motors on the screw agitators feature a temperature sensor and a cooling fan. This allows for smaller sized motors without a risk of overheating. The motor on the main drive is non-ventilated and therefore solely cooled by surface heat dissipation. These motors are controlled by frequency inverters to be run at different speeds at various stages of the process.
Like all AC vector drives manufactured by NORD, the SK 500E units on the main drives use field-oriented vector control and partial load detection. Due to the harsh environmental conditions, the inverters are installed in a control cabinet.
Sturdy, food-grade drive configuration
Robust BLOCK series parallel-shaft gearboxes were selected for the main drives. These multistage gearboxes feature a high gear ratio to enable slow and gentle agitation of the grain. The parallel-shaft gearboxes on the agitators are filled with a fully synthetic oil certified for the food industry. They feature stainless steel output shafts. They ensure corrosion resistance as well as high resistance against cleaning chemicals used in the facility. All drives were supplied with a special coating adapted to the wet environment in malt houses.
Phone: 03 9394 0500
Key Technology conveyor systems for poultry processing and packaging
Key Technology is introducing vibratory conveying systems for poultry processing and packaging...
tna intelli-assist XR solution for food manufacturers
TNA Solutions has launched the tna intelli-assist, an immersive Industry 5.0 extended reality...
Alfa Laval ThinkTop V55 sensing and control unit for diaphragm valves
The Alfa Laval ThinkTop V55 hygienic diaphragm valve sensing and control unit is suitable for the...