Improving production capacity with beer canning line
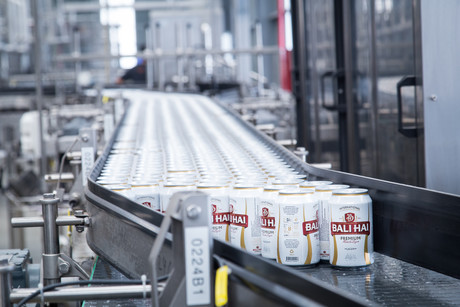
Independent Indonesian brewery Bali Hai Brewery has installed a canning line, designed and supplied by Sidel, to accommodate a higher production capacity in response to increasing consumer demand. The line runs up to 33,000 cans per hour for the 33 mL format and features a compact layout to facilitate the brewery’s space constraints.
The family-owned brewery has been developing and distributing a range of beer brands since 1975, with products sold in more than 20 countries, including Russia, Singapore, Thailand, Japan, Korea and New Zealand, as well as different regions of Africa.
As part of their investments in the past few years, the company decided to upgrade its canning line, managing 330 and 500 mL formats, to fit its needs for higher efficiency.
“Despite the fact that we were initially planning a line delivering 24,000 cans per hour (cph) for the 500 mL format, we eventually trusted Sidel’s engineers and went for a complete line that is able to reach up to 29,000 cph, thus securing high-capacity production for the coming years,” explained Daniel To, Technical Director at Bali Hai.
“The installation of the line was completed in a short period of time. The floor space available at our plant is limited; therefore, we needed a very compact solution that did not compromise on efficiency and flexibility,” To said.
The brewery opted for a complete line, reaching 29,000 cph, to provide a higher production capacity, and to run the canning line in three shifts, as opposed to the previous line, which ran in two shifts. The upgraded canning line includes 13 different machines, laid out in six larger production modules: the de-palletiser, the filler and seamer, the pasteuriser, the dryers, the shrink-wrapper and the tray shrink-wrapper, plus conveying systems.
Protecting beer quality is mainly achieved through the integration of two specific solutions in the line: Sidel’s volumetric electronic filler for cans and its PAMA pasteuriser that is designed to provide consistent beer quality.
“We opted for this Sidel filling technology largely because of the very low total oxygen pick-up it ensures, which ultimately leads to high product quality. Plus, we now use a volumetric technology, so as to guarantee that our cans all have the intended quantity of product when reaching the shelf. This way, there is no risk of product waste,” said Blegog Sugiono, Packaging Manager at Bali Hai.
The PAMA pasteuriser features Sidel’s PRINCE Plus software. The outfeed of the pasteuriser also allows the beer cans to be cooled, reducing the risk of unstable quality. The technology enables manufacturers to adjust and control the pasteurisation unit in accordance with the specified settings. The increased size of the pasteuriser also accommodates future production increases.
“A ‘Design to Cost’ approach has been applied to deliver a strong quality-price-performance ratio for shrink-wrapping at speeds of up to 60 cycles per minute. We also implemented a simple conveying solution to feed the shrink-wrapper: this way, the customer was able to save some factory floor space. In addition, we removed the need for a divider by orienting the lanes of cans differently. The customer is therefore able to manage eight pack configurations easily and efficiently. For greater versatility, the system can manage both packs and lose cans,” said Stéphane Séné, Key Account Manager at Sidel.
The upgraded canning line increases production output from 500 to 1450 trays per hour. With two different can formats (330 mL and 500 mL), nine different recipes and various secondary packaging options, the brewery can accommodate 18 SKUs. The canning line improves flexibility at the secondary packaging stage, with minimal impact on the brewery’s footprint. The brewery also shifted from RSC cases to film for economic benefits, installing the Sidel EvoFilm Access, a shrink-wrapping solution for low- to medium-speed applications during its renovations. The brewery also widened its secondary packaging solutions offered to customers, including multipacks.
“With the new line, we have a tray and film solution that we can apply to produce various packing alternatives; for example, four- or six-packs wrapped on one tray containing a total of 24 cans, run on one solution. If multipacks are not requested, products can bypass the tray and film packer directly to the shrink-wrapping system,” Sugiono said.
Phone: 02 9899 4642
Key Technology conveyor systems for poultry processing and packaging
Key Technology is introducing vibratory conveying systems for poultry processing and packaging...
tna intelli-assist XR solution for food manufacturers
TNA Solutions has launched the tna intelli-assist, an immersive Industry 5.0 extended reality...
Alfa Laval ThinkTop V55 sensing and control unit for diaphragm valves
The Alfa Laval ThinkTop V55 hygienic diaphragm valve sensing and control unit is suitable for the...