From roasting to seasoning: snack food maker controls automation
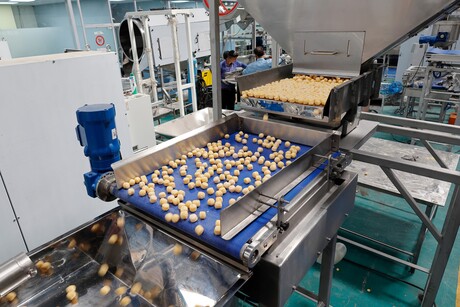
Siddhi Vinayak Agri Processing (SV Agri) uses Mitsubishi Electric’s factory automation (FA) products, such as programmable controllers, servos and displays, to build machines and conveying systems for producing snack foods from a variety of ingredients such as pulses, maize, millet and potato derivatives.
Based in Pune, India, the SV Agri is expanding its business all over the world, from the United Arab Emirates to Germany and the Philippines. More than a supplier, the multidisciplinary company comprises agriculture support, snack production and engineering services. While the company was founded in 2008, the engineering division only started operations in 2012, offering consultancy and sharing know-how with food production companies. Over time the engineering division expanded its scope to provide engineering and systems services that are focused on the snack food manufacturing industry.
Ram Manohar Singh, head of the company’s engineering division, noted that the relationship with Mitsubishi Electric factory automation started during the COVID pandemic, when SV Agri was searching for an alternative automation supplier.
There was a steep learning curve for SV Agri as it started to use Mitsubishi Electric’s FA products. However, Mitsubishi Electric India’s engineers supported SV Agri at every step, resulting in a strong bond of trust and collaboration between the two companies.
“One of the first areas that SV Agri’s engineers applied Mitsubishi Electric’s controllers and interfaces on was the roasting line,” Singh said.
Before installation, the heating temperature of the roasting line was set at a static 100°C. However, this did not reflect the real operational needs, which had to cope with varying production volumes from 200 to 1000 kg/h. To put this challenge in context, Singh said “the changing volumes can affect the roasting time and thoroughness of the applied roast”.
Furthermore, a variety of ingredients also needed to be catered for as the roasting qualities and parameters for nuts are different to those of beans and pulses.
The application of programmable logic controllers and servo systems has now helped overcome these issues. With a combination of research and development, and automated feedback control using PID, the roasting line can now flexibly adjust timings and temperatures to deliver the perfect produce with the required colour, texture and crispiness regardless of the volume, raw material or environmental conditions.
“Through our collaboration with Mitsubishi Electric, we could adjust the heating cycles to the required levels and provide our clients with the results they wanted,” Singh said.
Despite the steep learning curve, the engineering team at SV Agri has put a lot of effort and diligence into creating their control systems.
In addition, the new control methodology has also stabilised product quality, and lowered energy consumption, which for a roasting line is a high proportion of the operating costs. These added benefits are significant for operators in the food industry where low margins per unit produced are the norm.
Looking ahead, Singh said that his team was now investigating the use of robots in combination with the company’s equipment. “I’m looking to create a unique robot application dedicated to the needs of the snack food industry. I’m not interested in anything else, only producing snack foods,” Singh said.
Phone: 02 9684 7777
NORD Drivesystems NXD tupH surface treatment
The NXD tupH surface treatment has been developed by NORD to make aluminium as resistant as...
igus D1 motor control with certified PROFINET
The igus D1 motor control can now be integrated into higher-level control systems from Siemens,...
Protect-Air HoseGuard Air Safety Fuses
Protect-Air's HoseGuard is designed to enhance workplace safety by automatically responding...