Energy check on pump installation at food manufacturer's site
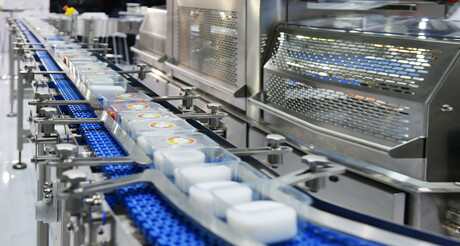
Grundfos performed an Energy Check Advanced on the pump installations of one of the world’s leading food manufacturers and established that even with minor improvements there would be considerable savings.
A Grundfos Energy Check Advanced provides users with an overview of the life cycle costs of their pumps. It gives an indication of possible energy savings and helps users make decisions on future pump replacements.
It can help users find hidden savings in their organisation by providing detailed information about energy-saving potential; actionable sustainability areas to improve environmental profile of a facility; and a prioritised installation list that details the pumps and systems which could benefit from an upgrade.
By improving or replacing just 10 pumps, the leading food manufacturer saved over AU$47,549.45 per year.
After inspection of 10 pumps, it was found that by investing in more energy-efficient pumps and performing other small improvements there was a potential for savings of AU$48,281.44 annually. The savings were owed to a reduction in energy usage by 448,207 kWh per year.
The initial outlay for the equipment and improvements was AU$217,842.10.
When the savings were factored in, the payback time for the optimisation was 3.59 years.
Dairy case study
In another case study for a dairy factory, a new control panel and four new pumps have been installed.
The dairy factory uses a clean water booster to feed water around the factory. The performance and dependability of this system is critical to the entire production.
Grundfos performed an Energy Check Advanced on one such system. The four-pump solution’s control panel was obsolete and one of the pumps had already failed. The user wanted reliability and peace of mind, and to have the pumps working close to their BEP with lower OPEX costs.
The new system comprised four pumps, installed with cascade operation based on flow demand — duty, assist, assist, assist. The previous system’s energy consumption was an estimated 133,240 kWh and the new system’s energy consumption is estimated at 80,517 kWh.
Phone: 08 8461 4611
ProfilGate clean-off zones
The ProfilGate brush-and-tray system is designed to help keep facilities clean by removing dirt...
RIDAQuick Gluten Quant & Smart Box
The RIDAQuick Gluten Quant & Smart Box from R-Biopharm Australia is used for quantitative...
Endress+Hauser Micropilot FMR43 radar sensor for hygienic processes
The Micropilot FMR43 is a compact radar used for continuous level measurement in hygienic...