Flour mill implements data management tool
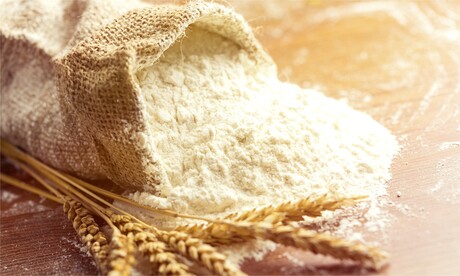
North American flour supplier and grain innovator Ardent Mills needed a system to organise sample management and tracking across laboratories. After meeting with Autoscribe Informatics, the company implemented its Matrix Gemini Laboratory Information Management System (LIMS) across the three laboratories in its Denver-based Innovation Center.
In an implementation process taking just six months, the LIMS has not only improved the efficiency of sample management and tracking within the laboratories but is feeding information into the company’s data warehouse to facilitate key business decisions.
Background
Ardent Mills was established as a joint venture between ConAgra Foods, Cargill and CHS in 2014. With more than 35 community flour mills and blending facilities throughout the United States, Canada and Puerto Rico, the company has a range of multi-use flours, whole grains, mixes and custom multigrain blends.
In 2016, it opened its Innovation Center in Denver, Colorado, USA, to drive product development, grain quality and culinary creativity. The Center features lab-size test mills, a wheat quality laboratory and a product evaluation bakery. It also has a variety of other testing and research and development facilities within the complex.
Challenges
The laboratories at the Innovation Center receive around 200–300 samples per day for various tests. Typically, each sample will have between 3 and 10 tests performed. Samples come from all of the group mills. Near infrared (NIR) testing, which can measure parameters such as moisture, fat and protein, is carried out at each mill, but samples are also sent to the laboratories to check NIR calibration and for many other measurements.
Testing raw materials determines their quality while testing baked products evaluates the materials used and the baking process itself.
The Center faced two significant challenges.
First, there was a need to significantly improve the management and tracking of samples through the laboratories. Sometimes, mills would send a sample that was not received, or occasionally, a sample that had been received could not be traced. This caused disruption and delays. The company would have to troubleshoot to find out what had happened to the sample.
Second, there was a need to use laboratory data to monitor and improve laboratory efficiency, including sample turnaround times, and provide trending information on different sample parameters, such as evaluating crop quality at harvest time. Test results were being recorded in spreadsheets which did not offer the flexibility to do this. The company uses several business analytical tools, and the laboratory data needs to be accessible to these tools.
Solution
The decision of how to fit laboratory management data in with the other tools being used was a complicated process. A list of functional requirements (‘must-haves’ and ‘likes’) was produced first, together with a detailed analysis of how the system should work and the number of different levels it should deliver. Completing the user requirement analysis took around three years, and during this process, a lot was learned about the potential problems and how to address them.
The user requirement analysis was an essential precursor to the selection of the LIMS. The first stage was to talk to all of the LIMS vendors at a local trade show. As a result of these discussions, three vendors, including Autoscribe Informatics, were shortlisted to demonstrate their systems.
This was when the Matrix Gemini LIMS was selected.
Despite the project’s complexity, all of the specialist screens for the LIMS could be generated by Autoscribe’s configuration team using Matrix Gemini’s built-in configuration tools. The graphical editor provides access to several controls that can be used any number of times to define specific screens and workflows with different configurations.
The ‘drag and drop’ approach to creating screens has no impact on the underlying core code, which both simplifies and speeds up development and allows rapid demonstration of the functionality within a screen. This is unlike developing a system using a programming or scripting language where a change made to a function to meet one specific requirement can have huge implications throughout the rest of the system.
This all helped significantly to meeting the six-month completion deadline.
Benefits
Sample management and tracking have been significantly improved through the introduction of Matrix Gemini LIMS. Sample labels can be created, giving details of the sample and the tests required, and these are affixed to the samples before shipment. The samples are then time-stamped and an automatic email notification issued on receipt. This ensures that the senders know that their samples have been received, and by time-stamping, turnaround times can be monitored and evaluated.
Overall, this has meant that the samples can be tracked throughout the testing process, and results and final reports can be accessed as required.
Another major benefit is that all the data from Matrix Gemini is imported to a central data warehouse. It can now be used in conjunction with all of the other data available in the warehouse to enhance data discovery and understanding using business intelligence tools such as Microsoft Power BI and Tableau.
One example of this is that the laboratory receives hundreds of samples from different areas over a 2- to 3-month period around harvest time. Test results can now be analysed according to zip code, allowing an assessment of crop quality from individual regions.
Overall, the generation of clean data, and the ability to store and extrapolate it, has allowed Ardent Mills to implement important flour and grain milling business decisions.
This was achieved by the Matrix Gemini Laboratory Information Management System (LIMS), which was implemented by Autoscribe Informatics in six months.
Phone: +61 404 084 077
Key Technology conveyor systems for poultry processing and packaging
Key Technology is introducing vibratory conveying systems for poultry processing and packaging...
tna intelli-assist XR solution for food manufacturers
TNA Solutions has launched the tna intelli-assist, an immersive Industry 5.0 extended reality...
Alfa Laval ThinkTop V55 sensing and control unit for diaphragm valves
The Alfa Laval ThinkTop V55 hygienic diaphragm valve sensing and control unit is suitable for the...