A peeling waste solution for fruit processor
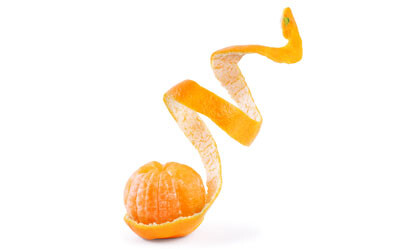
A New Zealand food processing company will implement a sludge dewatering technology engineered to cost-efficiently reduce the sustainability footprint of food, beverage and wastewater treatment.
The NZ producer — which cannot be named because of contractual confidentiality provisions — is installing a KDS multidisc Roller system from CST Wastewater Solutions to dewater wet sloppy screened waste from the peeling process.
This transforms fruit waste from a wet and sticky heavy mass to a much drier product that is less messy and easier to handle and transport for stockfeed or landfill.
The technology is designed to reduce fruit waste volume by up to 90%, thus reducing transport costs and helping prevent any potential spillages during transport.
CST Wastewater Solutions Managing Director Michael Bambridge said the processing company has committed to environmental excellence and has become the country’s first adopter of a sludge dewatering technology.
“Heavy cakes of by-product from growers and food processors can cost upwards of $150 a ton to dispose of, including the specialised transport from the places where trade wastes are generated to centres where compacting, drying, recycling and disposal can take place in controlled environments,” Bambridge said.
The NZ producer is adopting its KDS technology to handle a highly variable quality and volume of up to 5 m3/h.
“This first NZ adopter of the KDS technology had previously tried alternative technologies, but none handled the variable volume involved or dewatered the fruit waste enough to prevent excess water and product from creating an unhygienic site and causing leakage,” Bambridge said.
The NZ producer selected a model SS611 KDS with a longer press zone, to achieve dewatering of the sloppy and wet mix of peelings, leaves and pulpy fruit material.
“The dewatering concept being employed in this instance is to spread the waste over the table width and dewater a mat of material, to maximise the surface area and minimise water retention,” Bambridge said.
Suitable for the food and beverage industry, the largest KDS unit can handle about 100 kg dry solids an hour at 98% solids capture. It uses minimal energy, consuming as little as 0.06 kW per hour of electricity and operates at low (63 dBa) non-intrusive noise and vibration levels.
Phone: 02 9417 3611
NORD Drivesystems NXD tupH surface treatment
The NXD tupH surface treatment has been developed by NORD to make aluminium as resistant as...
igus D1 motor control with certified PROFINET
The igus D1 motor control can now be integrated into higher-level control systems from Siemens,...
Protect-Air HoseGuard Air Safety Fuses
Protect-Air's HoseGuard is designed to enhance workplace safety by automatically responding...